In the additive manufacturing (AM) process, the component parts are created with a 3D printer, based on digital design data, by layering the material. This is possible because of the perfect collaboration between intelligent machines, secure cloud technologies and modern 3D printing processes. This is how data from cyber-physical-systems (CPS) is collected in the cloud via the IoT, analyzed and used to optimize individual products.
Nowadays, metals, specific plastics, synthetic resin and ceramics are used as materials in the 3D printer. With AM, industrial companies are able to optimally incorporate the needs and requirements of their customers and to manufacture prototypes or spare parts affordably. In developing new products, presentable models are quickly available thanks to this process.
Advantages of additive manufacturing
Certainly, the main advantage of 3D printing is the fast and tool-free manufacturing of single parts. In addition, it is possible to directly involve the customer in the planning and adjusting of component parts or spare parts. The customer is the expert who knows the processes and requirements of his plant best. One further advantage is the immediate cost saving, not only during the production process but also due to very short delivery times and reduced warehousing. Single component parts can be produced on demand and regardless of location.
Furthermore, a significant reduction of weight of dynamically moved component parts or the integration of functionalities during the manufacturing process becomes possible. Not forgetting a considerable increase of energy efficiency thanks to flow and weight optimization. SMS group has produced plenty of 3D printed metal or plastic parts. This innovative solution is not only significantly less expensive for plant operators, but it also enables a novel, individually optimized design of component parts.
A practical example
Some of these component parts produced in an additive manufacturing process are already in use, as for example a spray head to cool forming dies in a forging press. The challenge therein was to improve the performance of a component part and thus to increase the productivity of the customer. The original spray head had been a massive and heavy component part. So, initially it was redesigned in close cooperation of the responsible department and the SMS group experts for simulations.
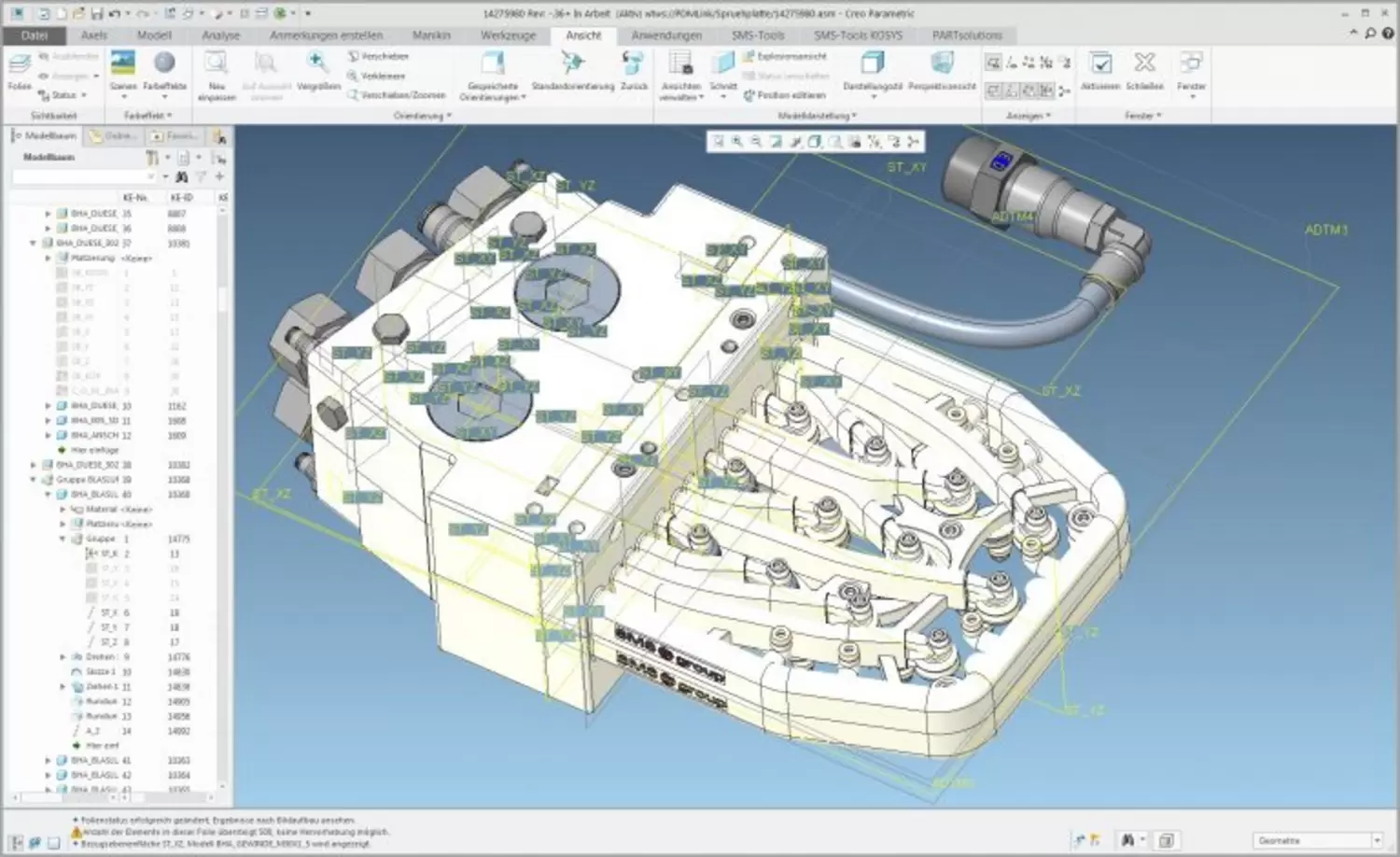
Due to AM the team was able to lay the channels in a flow-optimized way and leave out redundant and heavy materials. The spray nozzles were arranged to achieve the highest cooling capability at the temperature hotspot of the forming die. This lighter and individualized component part enables a faster and better cooling of the customer’s die now. In addition, it leads to a direct increase of productivity.
In a project for a copper wire rod mill, the challenge was to optimize an annular gap nozzle. In addition, the aim was to reduce the complexity of the adjustment of the component part. Annular gap nozzles are used to cool the wire and to skim water. The conventional part consisted of an assembly with multiple components and the adjustment of the gap for the airstream was done via a shim plate. The right adjustment of the part was highly complex. That is why this complex adjustment via the shim plate had to be eliminated.
The nozzle produced via additive manufacturing only requires 35 instead of 65 millimeters of installation space now. Furthermore, it weighs only 850 grams instead of 2.5 kilograms. The monolithic design of the nozzle consists of only one instead of six parts now. Consequently, the pre-assembly or adjustment of the nozzle prior to its installation in the plant is omitted. Additionally, the nozzles are made of a high-strength, wear-resistant material which extends their campaign life.
The results of the other projects are also promising: a new roll cooling pipe for wire rod mills provides a contour-adapted design with integrated nozzles. By using alumide, a blend of aluminum powder and polyamide powder, the new structure becomes lighter and cheaper than the conventional component parts.
In the steel-converter sector, it was possible to reduce the size of the SIS injectors by 60 %. They are now made of one piece instead of eight. Thanks to additive manufacturing parts, tube welding plants of SMS group will in future be able to produce tubes with a diameter of 14 inches or even less. With the hybrid way of construction, including additive and conventional manufacturing, smaller but still highly efficient oil rings for expanders become realistic. The technical service also benefits from lighter and faster deliverable connecting frames for loading belts in extrusion plants.
Cooperation of SMS group and Additive Industries
In another step towards Industry 4.0 a project of SMS group and Additive Industries combines two enterprises, that are specialized in the technology of additive manufacturing. This includes the production of metal powder and 3D printing. After the high-quality metal powder was produced it is melted in a powder bed based laser melting process. Subsequently it gets to the tempering station where it is annealed. Then the finished parts are automatically stored until delivery. This allows a highly efficient large-scale production in high quality.
The pivotal point of the cooperation between SMS group and Additive Industries is a joint pilot plant for additive manufacturing, in which the whole process takes place at one location. Subsequently the whole system can be scaled to industrial standard and be used as a turnkey solution at locations around the world.
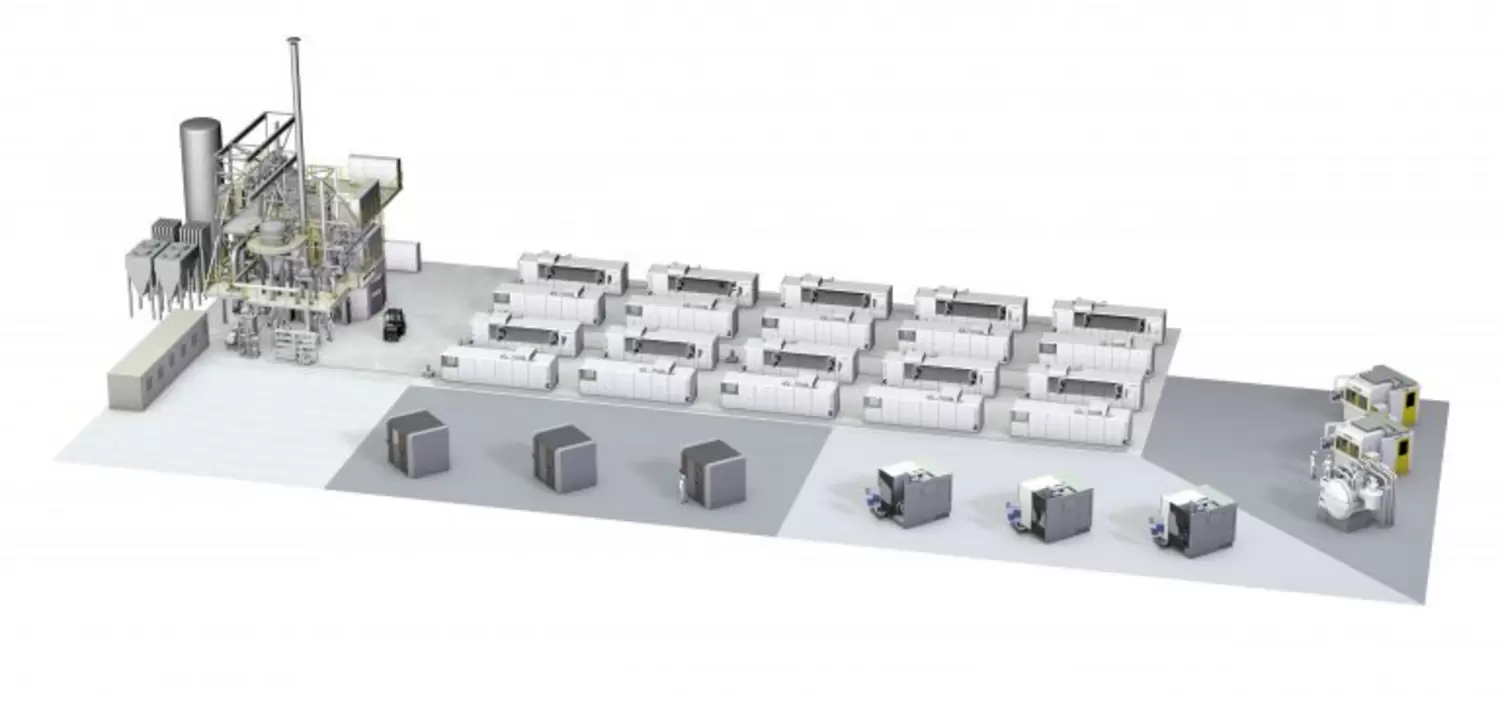
Conclusion
Industry 4.0 is based on many disruptive processes that industrial companies can directly benefit from. The advantages of additive manufacturing are of great interest to plant operators in particular. Spare parts can be optimized individually and be produced and delivered fast. This results in immediate and notable cost savings. With all the advantages, however, the secure data exchange is not to be underestimated.
In the development and optimization of component parts or spare parts, sensitive company data is the basis for 3D printing. This data must be protected during the whole process. For this purpose, as well as for other areas of industry 4.0, SMS digital has developed many specialized digital products. These applications are directly available in the Industry App Store and can be used via a digital platform, created especially for the metal industry. This way industrial companies can profit from the advantages of industry 4.0.
3D printing – how exactly does it work?
The most common 3D printing processes are the selective laser melting (SLM), the laser metal deposition (LMD) as well as the selective laser sintering process (SLS).
In the SLM process layer by layer a high-purity and homogeneous metal powder is melted with a laser in specific spots. This is how the component part is created bit by bit. This „powder bed process” makes component parts with complex and novel structures possible, that could not be produced with conventional methods.