SMS group has been successful in establishing in the market its MultiFlex-Quench®, a new technology for plate cooling in heat treatment lines. Flexible cooling strategies allow standard and special materials to be produced as well as newly developed grades with high quality demands. In 2016 already, the new MultiFlex-Quench® at SIJ Acroni in Jesenice, Slovenia, processed the first heavy plate. To this customer, SMS group supplied a complete, new heat treatment line designed for an annual production of 80,000 tons of heavy plate At the beginning of 2020, the new heat treatment line of IlsenburgerGrobblech GmbH, a subsidiary of Salzgitter Group, will start operation. The production capacity there will be more than 200,000 tons per year. For that line, too, the innovative MultiFlex-Quench® technology was selected to make sure heavy-plate production at the Ilsenburg location in Germany satisfies future requirements. This means the MultiFlex-Quench® technology is used in the two cutting-edge heavy-plate heat treatment lines. From an economical point of view, the production of heavy plate will be particularly efficient, if it can also serve the growing market of new special steels and quarto plates. The high-strength and ultra-high-strength plates are used in the growth sectors of wind energy, power technology, tubes and pipes, mechanical engineering and crane building as well as the construction industry.
At the same time, these applications, demanding excellent ductility and good weldability combined with perfect flatness, push the advancement of the material steel. To produce state-of-the-art heavy plates all process parameters, from austenitization to targeted cooling at optimized cooling speeds and further to adapted tempering temperatures and times, must be in perfect harmony in order to tap the full potential of the material steel
Development of new cooling technology for heat treatment lines
High-quality heavy plates are produced in heavy-plate mills setting the material properties in a thermo-mechanical rolling process, or in special heavy-plate heat treatment lines where the rolled plates are reheated, precisely cooled and then tempered.
The key process to set material properties is cooling. Laminar cooling systems with U-shaped pipes have been widely used in heavy-plate mills since the 1950s. But when material advancement required ever higher cooling rates and more flexible cooling patterns, this prompted the development of spray cooling systems with pinch rolls. At the beginning of the new millenium, this technology, usually a combination of spray and laminar cooling, became state-of-the-art.
Advanced materials, however, demand for the microstructure to be precisely set, which can only be achieved in a heat treatment line. Since the 1960s, roller-type quenches with separate high-pressure (HP) and low-pressure (LP) sections have been installed in heat treatment lines for plate cooling. But this measure only covered a limited process window mainly comprising the abrupt quenching method.
SMS group picked up the vast experience gained from spray cooling systems in the heavy-plate sector and, on the basis thereof, developed a new flexible cooling system for heat treatment lines. This advancement of a proven technology generated the MultiFlex-Quench® in 2015.The new cooling technology permits numerous cooling rates and patterns to be applied in heavy-plate heat treatment lines and ensures a high degree of flatness.
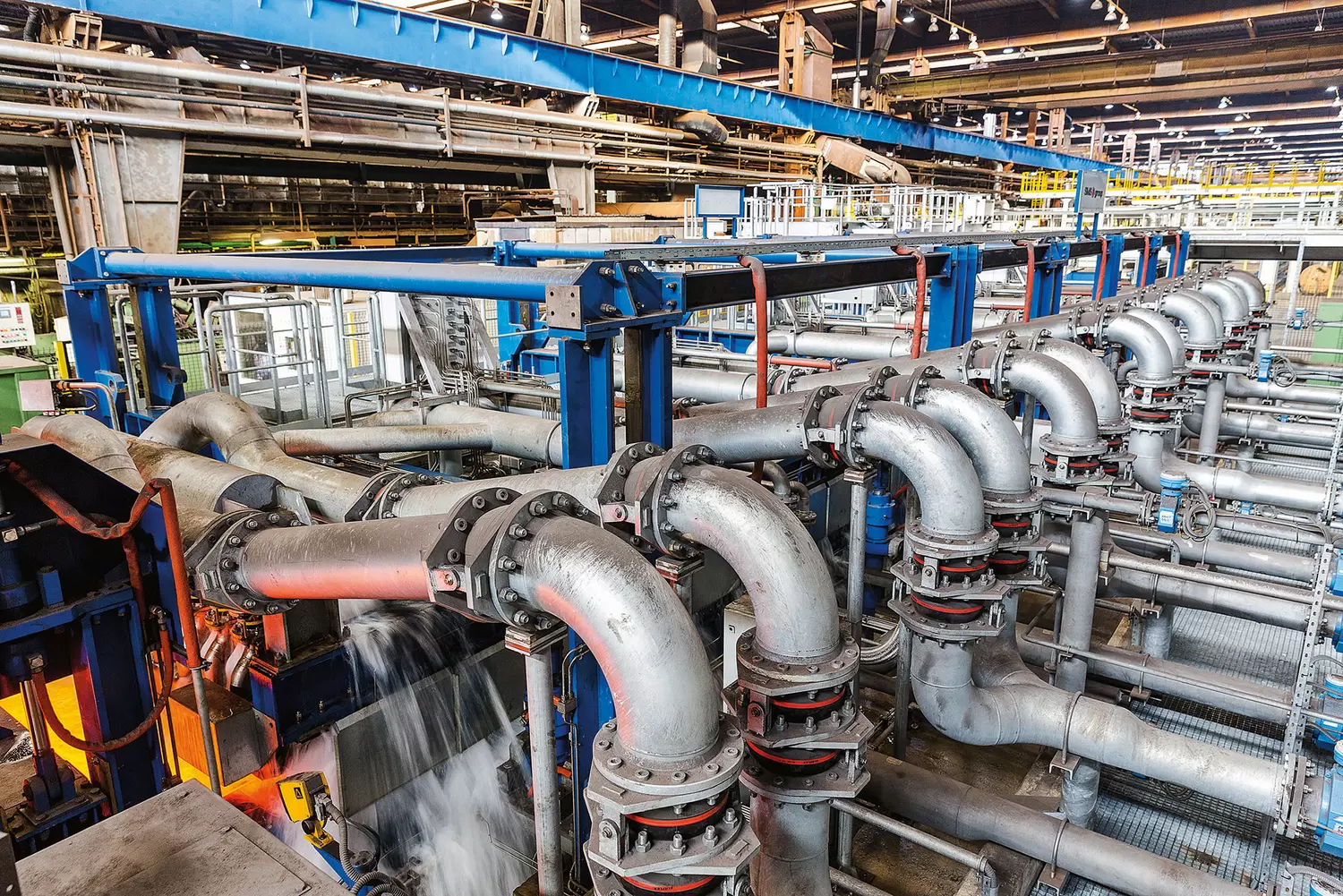
Flexible cooling with numerous options
The high degree of flexibility, the wide product portfolio and the very good flatness results of the MultiFlex-Quench® are mainly due to a variety of options for plate cooling, hydraulic plate clamping by pinch rolls and due to subdividing of all cooling headers into several zones over the entire width.
The MultiFlex-Quench® concept provides for multiple options and expansion stages depending on the customer’s needs and production program.
In the basic expansion stage, cooling header groups arranged in segments are fed with water from an LP system. This method is preferred for high-alloy steels where carbide precipitation after a solution annealing treatment is to be suppressed and also for crack-sensitive tool steels.
If necessary, it is possible to operate some of the cooling headers at higher water volumes and hence pressures in a customer-requested arrangement. This mode can be applied for wear-resistant steels with good ductility and for highstrength and ultra-high-strength structural steels. If surface hardness or hardness depth are to satisfy extreme demands, it will be possible to install a so-called slotted nozzle (curtain head) in the entry section of the quench. It provides the highest possible cooling rates. Such special applications are needed needed for special heat-treated steels of high wear resistance accompanied by high ductility at low temperatures.
For the treatment of crack-sensitive tool steels, the MultiFlex-Quench® may be equipped with a separate nozzle cooling system. Combined with the integrated cooling model, the system is able to exactly implement cooling rates and patterns. This helps substantially shorten the average period needed so far for cooling such materials in calm air or by compressed air. Several nozzle options permit a large cooling area to be covered and ensure maximum flexibility. All cooling headers are able to act upon a large area and come with a fine nozzle distribution and an optimized design.
Models and process development
The technological centerpiece is complex, thermal online process models for cooling strategies. They cover a broad range for the targeted setting of most different mechanical property combinations in the heavy plates. The use of proven physical Level-2 online models, such as the SMS cooling model, makes sure the process is precisely controlled. SMS group also supports its customers in the development of new material grades. The focus here is on new heat treatment cycles which will be deposited in the model after successful testing.
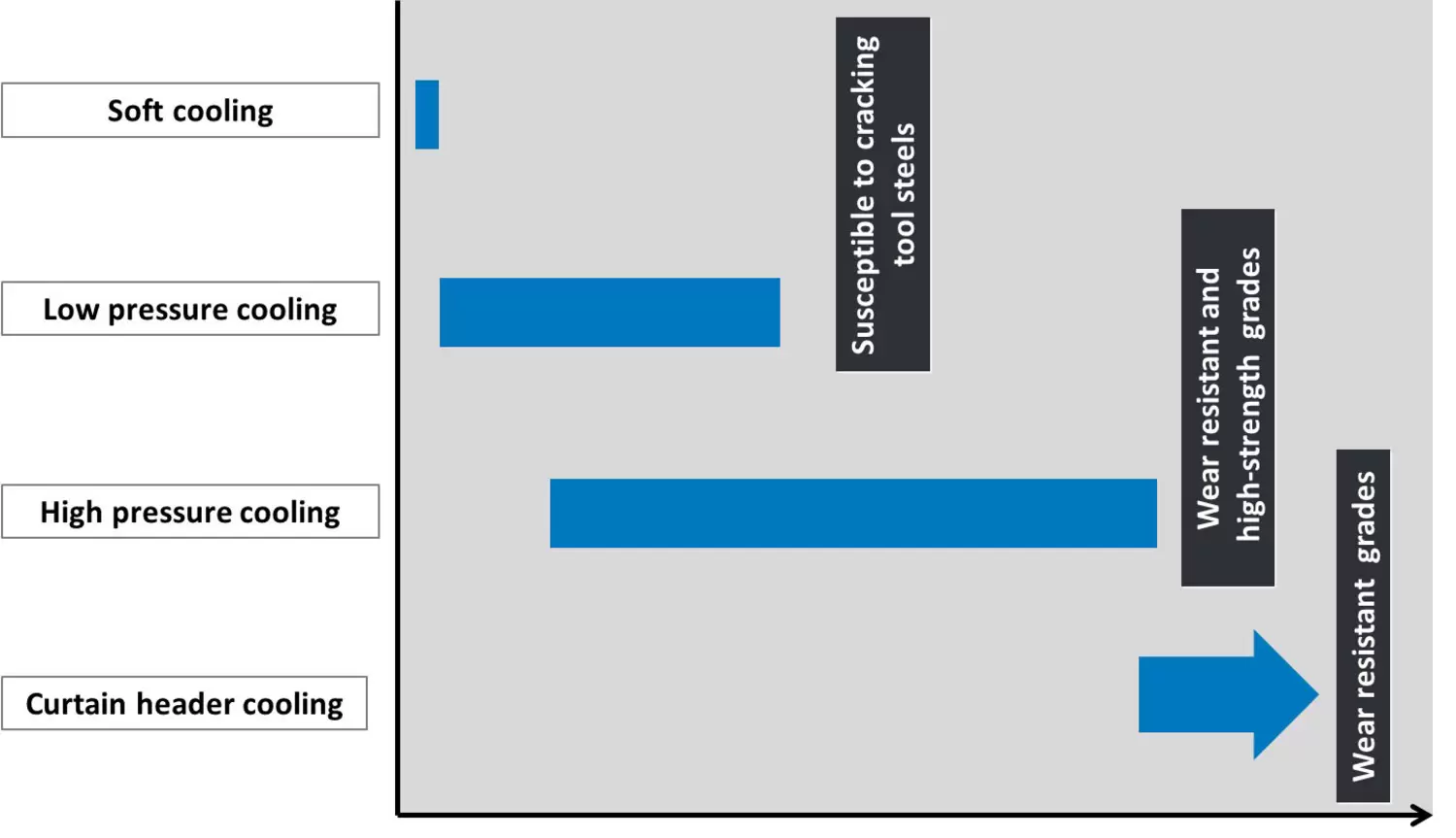
Operating results
The results so far obtained from operating with the MultiFlex- Quench® prove that a broad spectrum of steels with most different cooling requirements is feasible without neglecting homogeneous material properties or high flatness.
Numerous tests revealed that the flatness results meet the respective requirements independent of the thickness range and the cooling strategy. In many tests with a minimum demanded deviation of less than five millimeters per meter, for example, all measurements were below two millimeters per meter. Furthermore, the tests demonstrated that a narrow spread of surface hardness within ±5 percent is technically feasible.
In addition to an extensive product portfolio, the plates treated in a MultiFlex-Quench® convince with their excellent flatness.At SIJ Acroni, all options for targeted setting of cooling strategies as integrated in the MultiFlex-Quench® are applied with good results, including the model-based mode for interrupted cooling of crack-sensitive steels.
Compared to conventional roller-type quenches, the MultiFlex-Quench® offers a distinctly more flexible, uniform and efficient cooling technology for heavy-plate heat treatment lines.
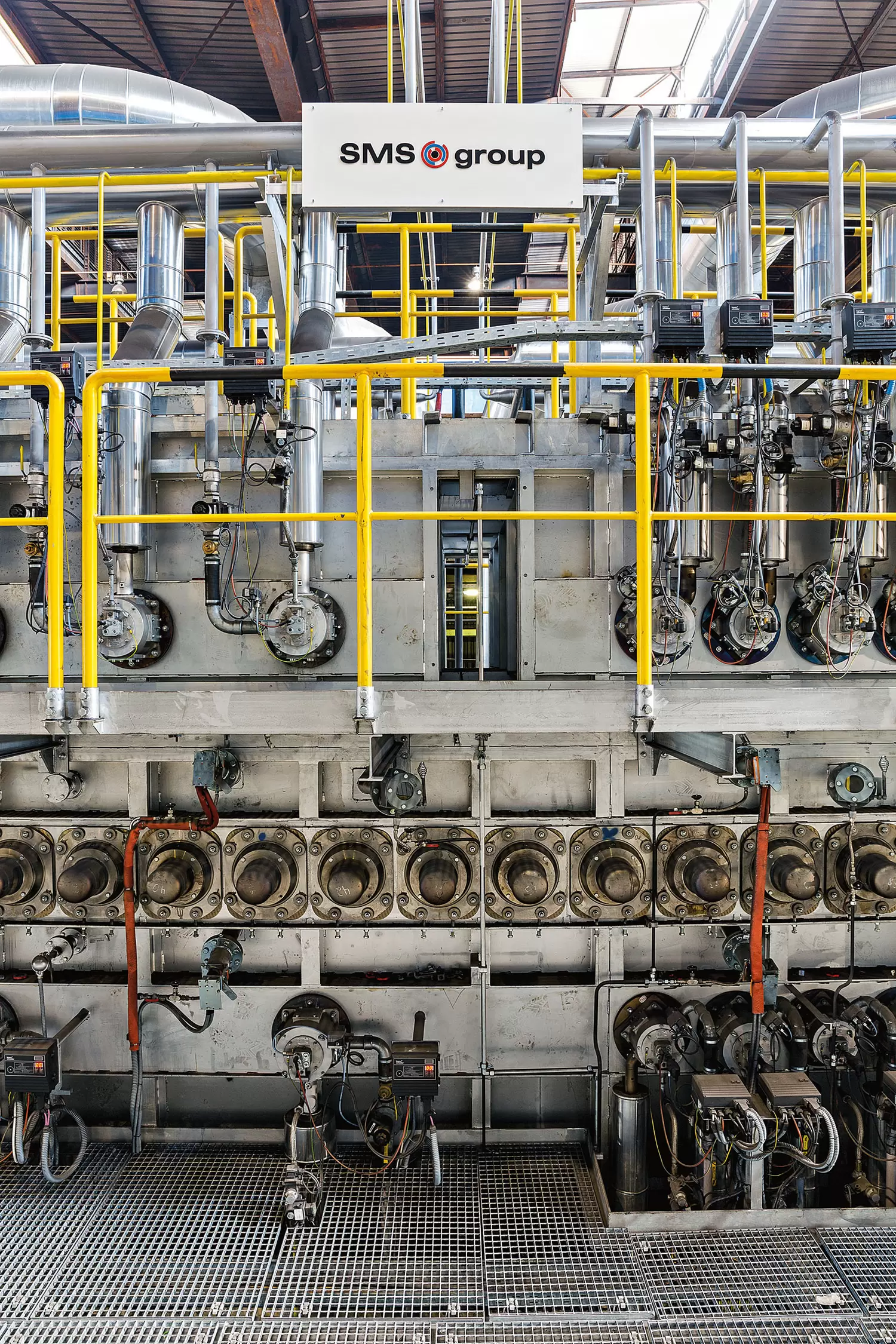