Within the shortest period of time, the SMS group workshop in Tarcento, Italy, has manufactured 23 skids for 60 pumps for numerous projects in the USA and in Europe. The versatility of the XL Pro VACUUM design allows application in different processes, all aimed at the production of high quality steel grades. The assembled skids are especially earmarked for vacuum degassing (VD) and for the vacuum converter.
“Handling 23 skids - each one weighing more than 12 tons - is surely a special challenge. But thanks to an optimized scheduling and logistic planning, we were able to manage production without delays” said Franco Del Fabro, workshop manager in Tarcento.
Pumps, motors, valves and sensors are delivered as individual components and in the workshop, they are assembled into a proper skid structure by the SMS experts. This approach allows having direct control on the quality of construction and, at the same time, makes it possible to properly check alignment and tolerances. Once assembled, the skids are tested using calibrated nozzles in a dedicated area of the workshop. Motor control center, PLC cabinet and diagnostic software complete the test environment. Once the tests are finalized and the actual performances double-checked, the XL-Pro VACUUM units are ready for shipment. SMS personnel on-site look after the proper installation of the modules and carry out the performance test of the entire vacuum system.
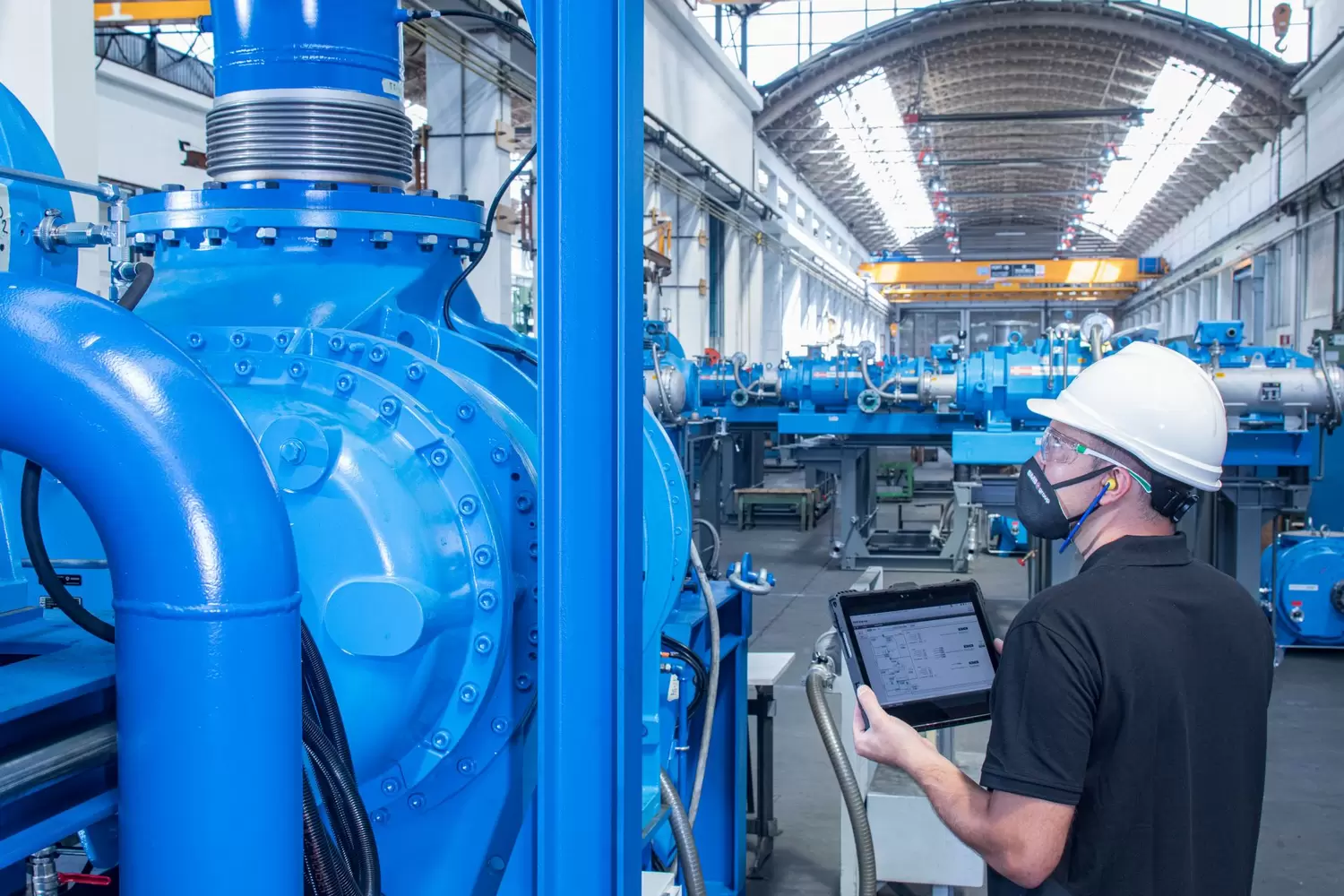
XL-Pro VACUUM pump
The XL-Pro VACUUM has a suction capacity of 40,000 m³/h at a delivery pressure of 0.67 mbar, and guarantees a very fast pump down time and consistent performances. Furthermore, the skid has the outstanding ability to react to sudden overpressure in the vacuum line: the control system is able to slow-down and re-accelerate the pumps in a very short time frame. Since 2014, SMS group has assembled and tested more than 40 skids at the Tarcento site.
“SMS group is in a position to merge technical and process competence in a unique combination for the benefit of our final users. After the first installation in Turkey in 2013, the decision to keep this core equipment in-house was welcomed by the market”; Andrea Lanari, General Manager Sales, summarizes the wishes of many Customers who do not only look for a vacuum machine, but for the related vacuum process, too.
“After being the first company to have adopted mechanical pumps in a steel vacuum process in Europe, we have decided to look for alternatives since the expectations of the steel makers were higher than the solutions available in the market. Thus our decision to bring in-house the responsibility of the system and not delegating the performance of our plant to external sub-suppliers”, underlines Guido Michelon, Vice President of Metallurgical & Environmental Plants.
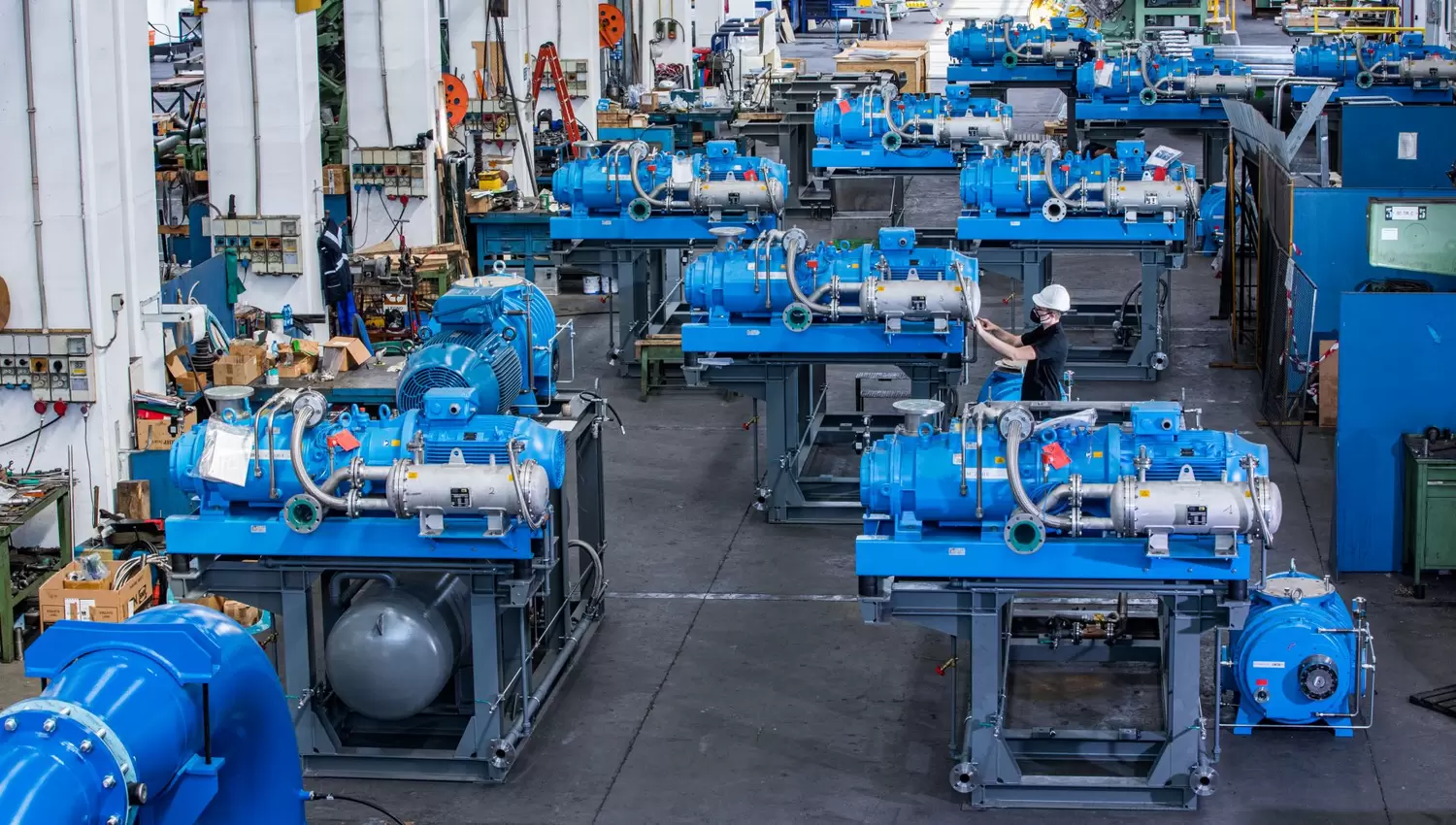