Mr Winterfeldt, for three years you have headed the Forging Technology sector in SMS group, which also includes the extrusion business. How has the business sector developed since then?
Thomas Winterfeldt: In recent years we have developed further strategically and established ourselves at a much more international level. In our most important markets outside Europe – in China, the USA and India – we have built up an extensive network with our own staff, in order to be as close as possible to our customers in those regions. And besides classical mechanical and plant engineering we are developing new business fields, such as digitization and the Competence Centre for Additive Manufacturing, in which we also want to grow substantially with our eyes on aluminium as well.
In September 2020, SMS group increased its share in Omav from 25 to 100 percent. Since then, the Italian company Hydromec also belongs to SMS group by way of a 70 percent share owned by Omav. What advantages are linked to those takeovers?
Thomas Winterfeldt: Omav offers a broad spectrum of knowhow-rich products in front of and behind the extrusion press, which supplement the portfolio of the SMS group very effectively. For example, the company has an energy-efficient HP7 high-performance billet furnace characterized by high thermal efficiency of 75 percent and low average consumption of less than 18 Nm3 of natural gas per ton of log material. This is achieved in particular by a preheating zone in which the logs are preheated by means of the exhaust air of the combustion zone. In combination with the efficient induction units made by IAS GmbH which belongs to SMS Elotherm, both of them companies of the SMS group, we can also provide combined billet heating in a single line. And for section cooling Omav offers very temperature-precise quenching systems.
And even for the construction of extrusion presses there is the collaboration that leads to ‘SMS Presses – Made by Omav’. Reciprocal technology transfer is naturally the more easy, the closer the partners are financially connected with one another. However, the collaboration was already close in the past – for example for the 55-MN extrusion line for Thöni or the 45-MN line for Constellium in Singen, which began operating in the summer of 2020. In both extrusion lines the run-out behind the press came from Omav. What Omav has lacked until now was a globally established marketing network for the services business. Here, we want to involve our Italian friends in greater depth, which will certainly also contribute towards their further company development. Our customers will benefit both from the conjoint range of existing products and also from the world-wide servicing available from SMS group.
The same applies to Hydromec, the new group company. Hydromec is in the immediate vicinity of Omav, with workshops that supplement it. Hydromec is an efficient company in the fields of closed-die and open-die forging as well as ring rolling. With Hydromec we will follow the same successful path as with Omav in recent years. Now we have the possibility to serve the global aluminium market together and are in the aluminium market as system suppliers, beginning with the recycling and melting furnaces made by Hertwich Engineering, also an SMS group company, through extrusion and forging machines, and all the way to run-outs and heat treatment plants.
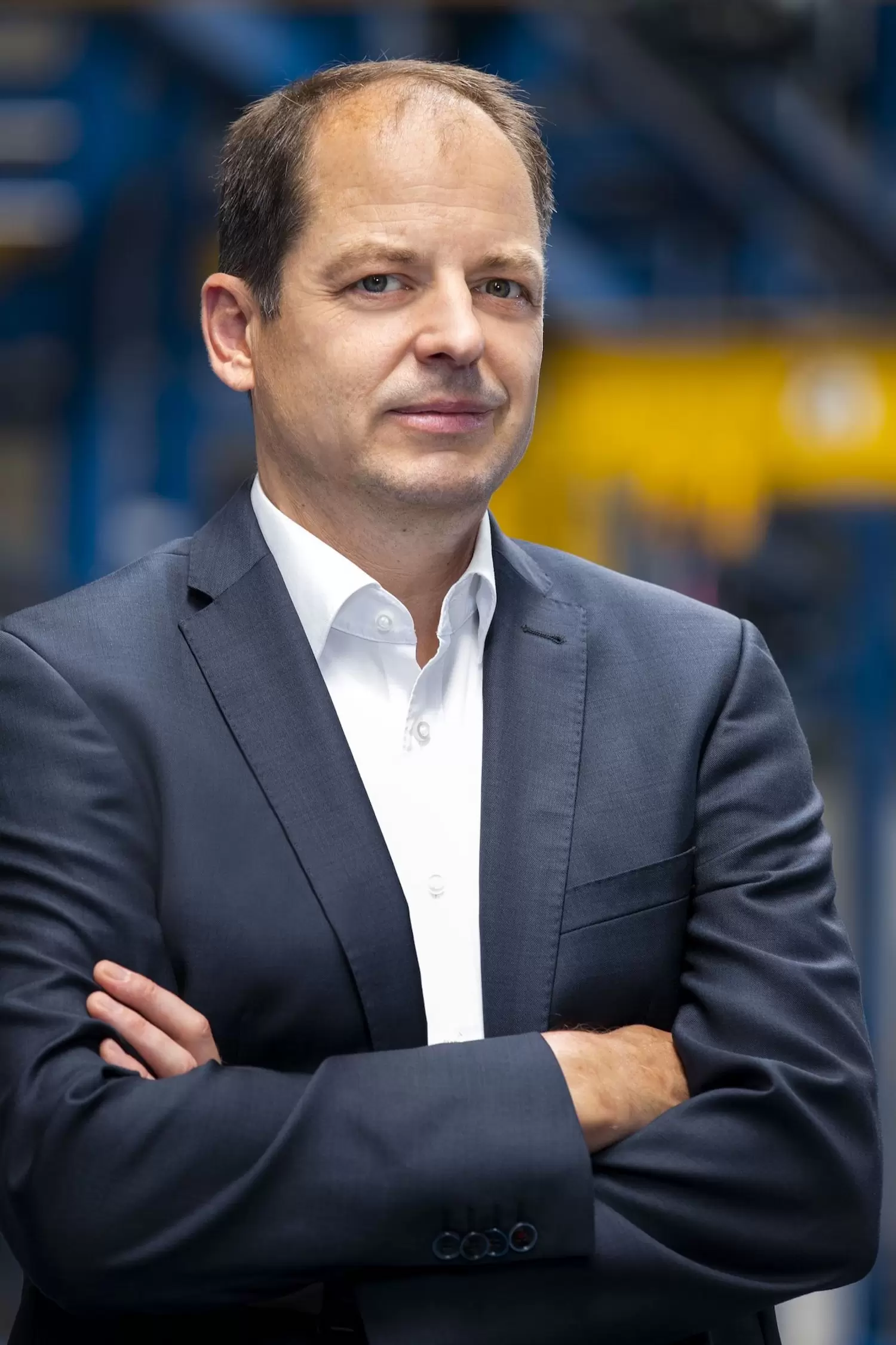
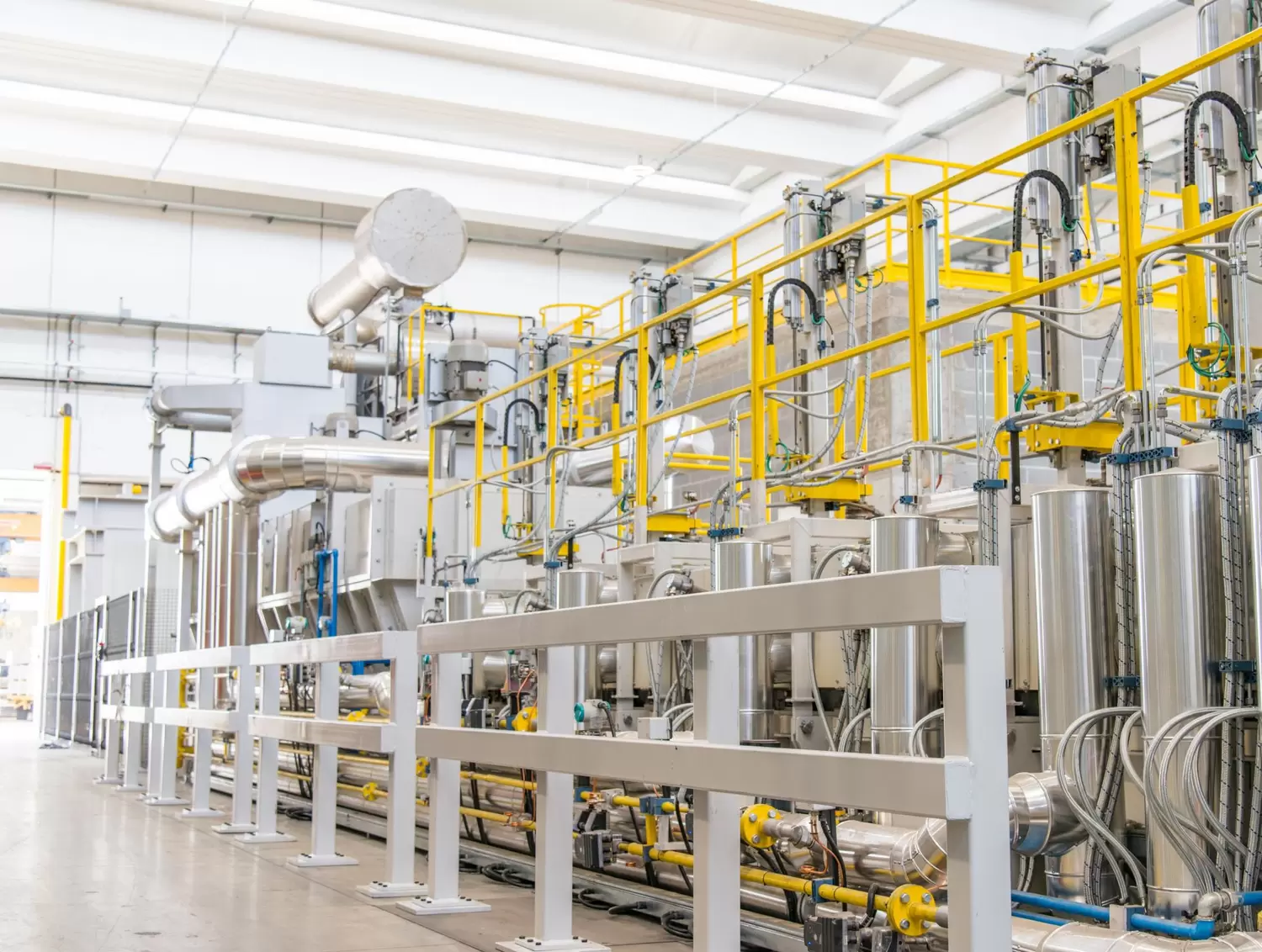
The Covid-19 pandemic has probably thrown business plans overboard for the SMS group as well, as for other companies too. What traces has the pandemic left behind it at SMS?
Thomas Winterfeldt: So far we have come through the pandemic comparatively well. The first half of 2020 went off relatively unscathed for SMS group as it did for the forging technology sector; order intakes continued largely according to plan until then, but from the summer onward it became perceptible that projects came to a halt and order intakes declined. However, we were able to pick up a lot in our servicing activities, which are becoming more and more important for our group and for Forging Technology. Meanwhile, around onethird of our contracts relate to servicing, in other words the classical after-sales business with replacement parts, repair and modernization contracts. We seek to establish longterm agreements with our customers and we also see on the customer side increasing readiness to outsource these activities to us as technology partners, in order to be able to concentrate completely and fully on their core business – namely running optimized processes and manufacturing qualitatively highgrade products.
For many long years China was the most important market for SMS group. Did business in China also help you last year during the Covid pandemic?
Thomas Winterfeldt: Market activities in China remained to a large extent unaffected by the pandemic. There, we have seen and are still seeing lively project activity and are very successful in China with our forging technology business. In China we mainly serve customers producing for technologically demanding applications in the automotive and aviation industries, and who turn to SMS as an experienced and competent project partner.
Hansjörg Hoppe: An example of that is the contract awarded to us in December by Shandong Weiqiao Light Metal for a 28-MN direct / indirect extrusion and tube press. This is a very special unit with many technological features. From the third quarter of 2022 the press will be producing profiles and thin-walled tubes of aluminium – mainly for demanding automotive products. The contract was agreed and signed by our local staff without anyone having to travel out from Germany, but with video-conference support.
Thomas Winterfeldt: Thanks to our well-established presence in the various market regions, despite the travel restrictions we have been able to reactivate several construction sites quickly, link up with our experts remotely, and complete a number of projects. For example we brought to the acceptance stage a closed-die forging press with a new drive in the USA and in China an open-die forging press, and in India we are continuing with the commissioning of a wheel-rolling mill.
Hansjörg Hoppe: India’s market too is developing very well for aluminium projects. We are represented there by a company of our own, which is responsible for the engineering and for project implementation. Meanwhile, we have been able to sell five aluminium extrusion presses made in India.
In the aluminium industry there is nowadays much talk about low-carbon aluminium. More and more primary aluminium producers offer low-carbon aluminium under creative brand names. To what extent does such a trend also reach you?
Thomas Winterfeldt: The issue of carbon footprint is becoming more and more important in the project inquiries that we receive. In the steel industry, that aspect has become highly topical under the slogan ‘green slabs’. But in the aluminium sector too, besides the performance- related technological plant features everything has revolved around reducing energy consumption and CO2 emissions. Here let me again refer to Hertwich Engineering, which sets the benchmark with its energy-efficient melting furnaces for aluminium scrap.
Hansjörg Hoppe: In the extrusion sector, already years ago we achieved a great leap forward toward still more energy-efficient production with our HybrEx press and its electric servomotors.
With conventional presses too, you can point to numerous implemented measures that reduce energy consumption and idle times. Is the specific energy advantage of the HybrEx still really significant?
Hansjörg Hoppe: We continually carry out energy measurements on HybrEx presses during everyday operation, and can therefore confirm very definitely that the energy advantage of a HybrEx is considerable. Of course, energy consumption depends on the products and the alloys that are processed by such a machine. However, as a rough average the energy consumption with a HybrEx is less than 80 kWh per tonne of profiles. With our conventional extrusion presses we fluctuate within a window of about 110 to 115 kWh per tonne. And even that, compared with the energy consumption of these machines twenty years ago, is a clear advantage.
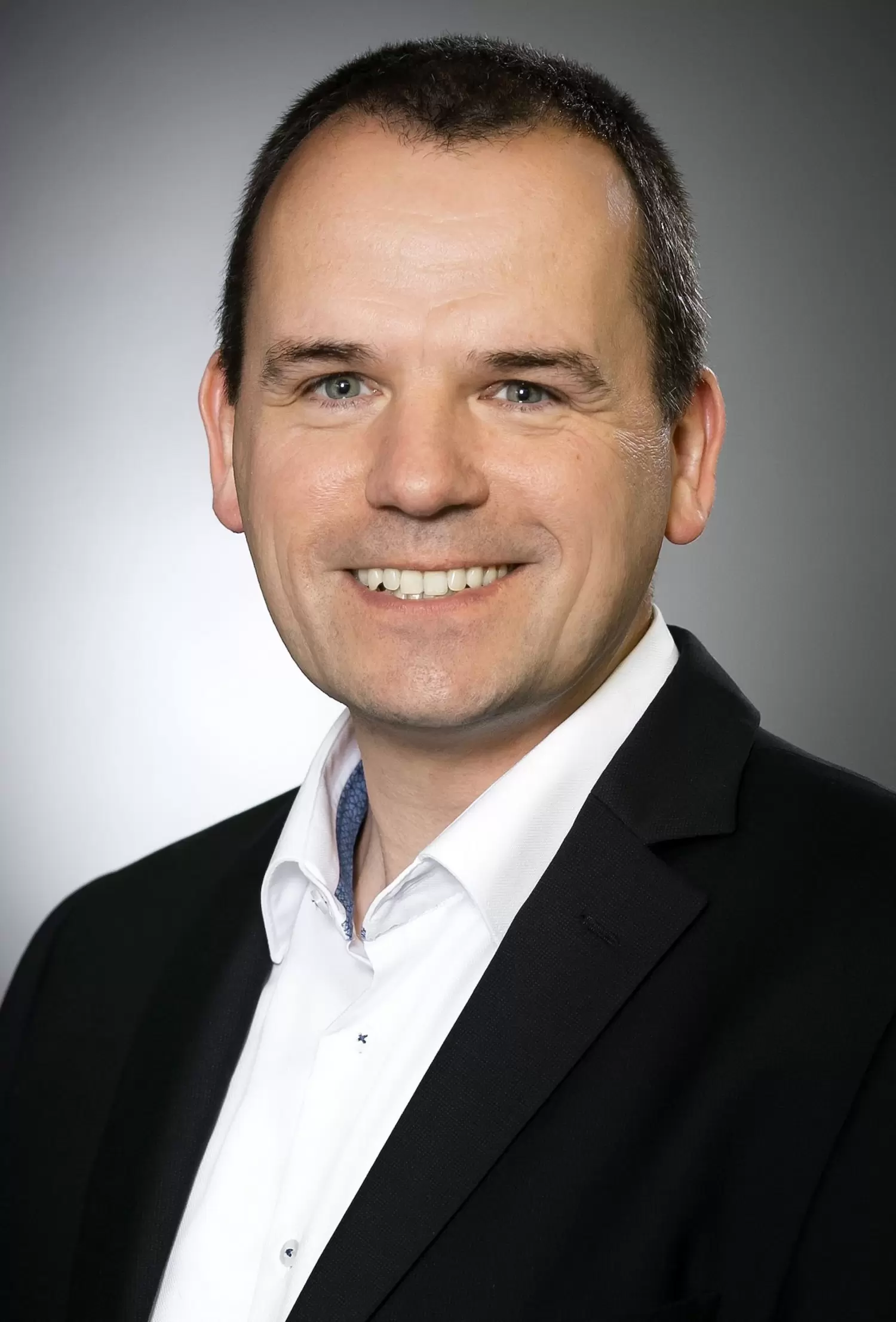
How many HybrEx machines have you now sold and up to what size are these presses availalble?
Hansjörg Hoppe: We have sold a dozen HybrEx presses – all over the world. For example a 40-MN press for 10-inch billets was delivered to Japan for UACJ and a 35-MN HybrEx for 9-inch billets to England, both of them achieving their final acceptance last year. We offer the HybrEx up to a size of 45 MN. The limiting factor is the size of the motors for moving the running beam and container.
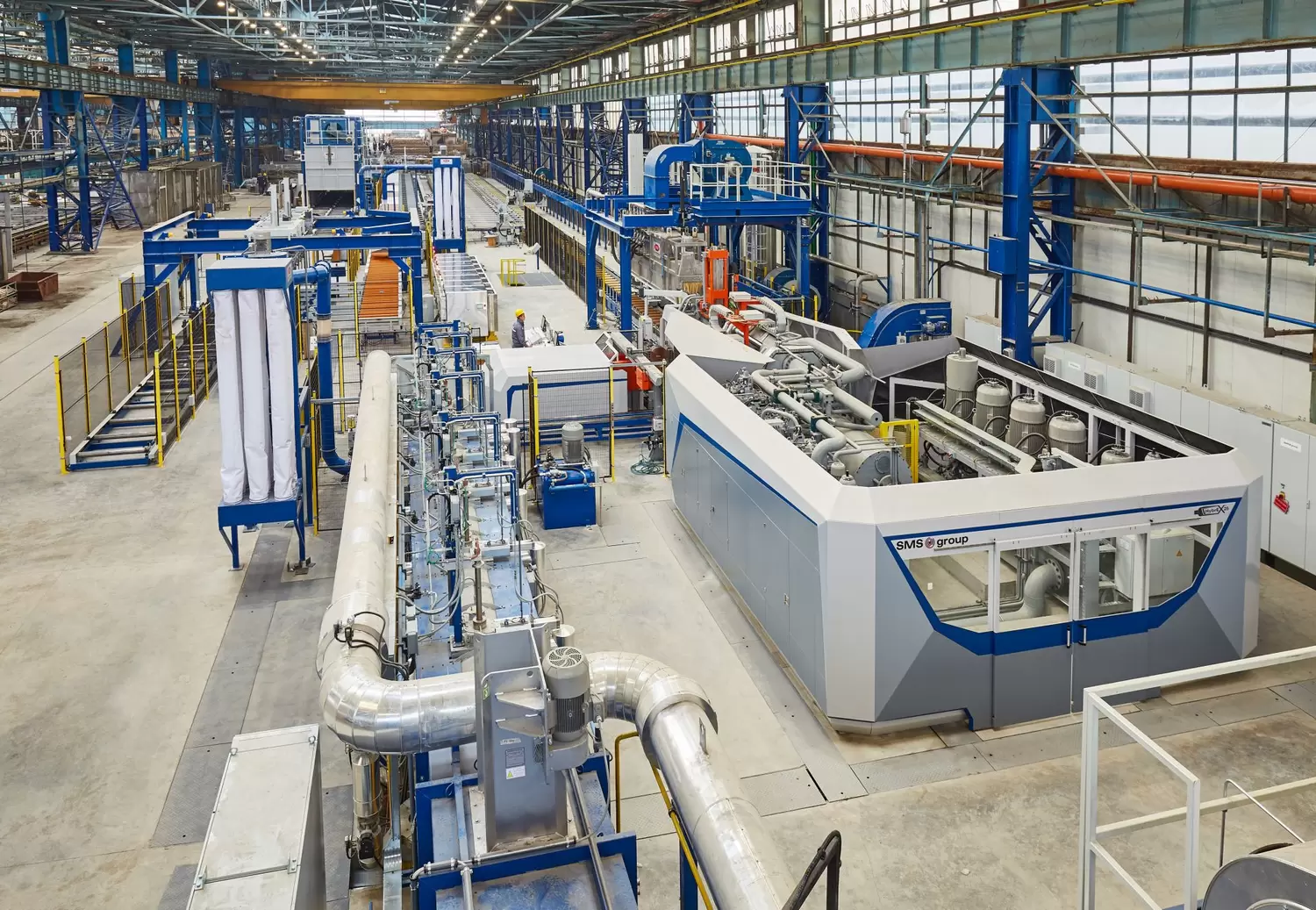
How important is digitalization for your sector?
Thomas Winterfeldt: Taking account of digital technologies in our machinery and plant is decisively important for a proactive analysis of the plant status, for product quality, for production planning and for energy management. It is all about transforming data into information and information into added value for the customer. In this we are assisted by our company SMS digital, which develops tailor-made, utility-orientated software systems. In times to come intuition and years of experience will no longer be sufficient for the optimum operation of a plant. Today we offer the most up-to-date digitalization tools, which are perfectly designed for extrusion and through their sensor systems and the evaluation of large data volumes in real time, enable deep insights into the processes and the state and behavior of the entire plant components. In that way the plant operator benefits from transparency and supportive analyses which have not been available before. Even the smallest deviations are recognized at an early stage, or faults can be avoided by learning systems (digitalization) or documented before they take place. This is also hugely important for the back-tracing of defective products. In the case of aviation products this has already been a ‘must’ for a long time and in the automotive industry it will also be the case in the not too distant future. In the Big River Steel plant built by SMS in the USA, no coil leaves the plant without all its production parameters having been documented and the AI-supported system of the coil released for marketing.
Would you say a little more about your software tools?
Hansjörg Hoppe: Take our Picos visualization system – with this, the press operator can monitor and control the entire process flow. The tool visualizes the production specifying the required process parameters. It shows the actual values, includes an alarm function and delivers diagnoses when a fault occurs in the production flow.
Thomas Winterfeldt: The Midis+ technology package enables the management of all product relevant data and increases the overall equipment effectiveness, so that we cover the whole of the process chain from the delivery of the billet to the packaging of the finished product. Thanks to the recording of numerous parameters and by clear visualization, the plant operator easily detects potentials for improving the performance of his extrusion press. With SMS Metrics machine data are gathered, stored and evaluated in real time. Thanks to transparency, plant operators are able to expand their process know-how. Evaluations can be easily prepared on a dashboard browser and be retrieved worldwide.
Hansjörg Hoppe: We have already been using the Cadex software for a long time. It enables the extrusion process to be optimized by means of thermal simulation. For that, the heat balance for each billet is calculated so that the material can be deformed at the optimum billet and taper temperature.
Thomas Winterfeldt: We offer each of our customers a basic digital package. This is supplemented by Smart Alarm – a web-based application for operators, shift managers, maintenance staff or even plant managers. Smart Alarm ensures better oversight and better control in the event of alarms triggered in the plants. Via long-term storage of historic alarm, data alarm trends can be calculated that will permit to detect potential downtimes. The web-based application was developed by SMS digital. All these tools help the customer to improve his plants and processes and offer advantages in servicing business because we can also give long-term guarantees about the availability of the equipment.
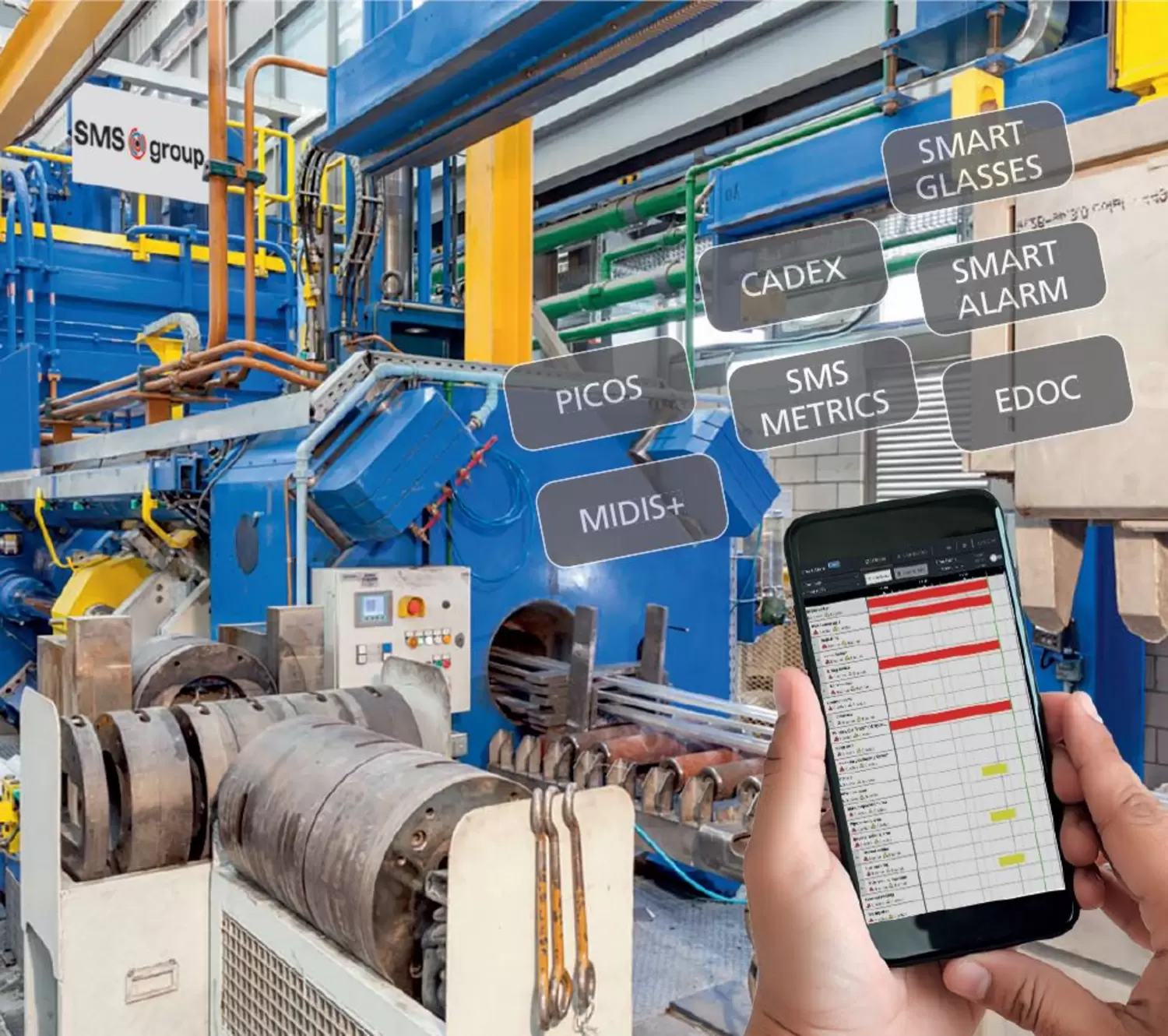
Earlier you mentioned the building up of new business fields in the context of additive manufacturing. This also includes the production of metal powder by a powder atomization unit. To what extent has that field developed?
Thomas Winterfeldt: With our own powder atomization plant we have gained knowledge with which we can already produce various highly alloyed metal powders. We have been able to place a unit of that type with our customer Outokumpu under an ‘Equipment as a Service’ contract model. With plant technology for atomizing aluminium powder we have developed an attractive concept and are in talks with potential customers for conjoint implementation, so as to be able in the future to offer units for the production of high-grade aluminium powder. In our view this is a most promising future field because AM offers new possibilities for the function- optimized design of components whose potential is already becoming evident. Already in some of our plants we have created a number of 3Dprinted components with functionoptimized designs. As an example a hydraulic control block for open-die forging presses can be mentioned, which is more compact, flow-optimized and much lighter than the previous control blocks, which were very complex and expensive to produce. We have designed a spray head which is used for the cooling and lubrication of dies in forging machines. That was produced completely by the additive method and was distinguished in 2019 with the German Design Award. So, just as we are system suppliers in forging technology and extrusion lines who can provide the entire process and all the equipment components for a line, we also want to master the entire process chain in the sector of additive manufacturing technologies.
This interview is courtesy of Giesel Verlag GmbH. The full version of the article was published in the International Aluminium Journal No. 3/2021.
The same applies to Hydromec, the new group company. Hydromec is in the immediate vicinity of Omav, with workshops that supplement it. Hydromec is an efficient company in the fields of closed-die and open-die forging as well as ring rolling, and was in thepast a serious competitor for SMS group, at least in the European market. With Hydromec we will follow the same successful path as with Omav in recent years. Now we have the possibility to serve the global market together and are in the market as system suppliers, beginning with the recycling and melting furnaces made by Hertwich Engineering, also an SMS group company, through extrusion and forging machines, and all the way to run-outs and heat treatment plants.