电炉(EAF)直接使用废钢作为主要原料,因此与传统的长流程相比,可大幅减少碳足迹,最高可减少 90%。只要使用绿色电力,这种方法是生产近零排放钢材的最快途径。尽管如此,电炉炼钢在产品质量和效率方面仍有很大的优化潜力。
废钢管理和产品质量
在电炉中使用回收废钢时,铜、锡和铅等杂质元素无法在熔炼过程中消除,从而会降低延展性并导致脆性,影响最终产品的质量。要从废钢中生产出高质量的钢材,先进的分拣、混合和预处理技术是必不可少的,这样才能满足严格的质量标准,从而生产出优质钢材。
X-Pact®金属优化器通过优化废钢和金属材料的使用来提高效率,确保有效的混合、更高的质量和更好的资源利用。它针对目标钢种选择成本最低的炉料组合,实时验证和更新杂质元素的估算。这一迭代过程可实现稳定、高质量的产出,同时降低能耗。
对于废钢成分的反向分析,X-Pact® 取样器为优化炉料组合和提高成材率提供了可靠的数据。这一先进的机器人应用实现了钢水取样的自动化,包括样取样运输和取样枪变形补偿,并完全集成到主自动化系统中。
成材率和能效最大化
实现成材率最大化和能源效率最优化是确保电炉炼钢成本效益和环境可持续性的关键。多年前,我们的自动渣门技术-Condoor®--为无人操作概念的诞生铺平了道路。作为一种炉渣阀门控制系统,Condoor® 可管理电炉中的渣量和气氛。通过精确控制这些参数,可减少材料损耗、提高总成材率、优化能耗并减少电极用量。Condoor®还可在现有设备上进行改造,是升级改造项目的完美解决方案。它的设计使其能够与各种类型的固体和液体炉料兼容,这一点已通过多个项目得到证实。
提高成材率的一个关键因素是控制电炉内炉渣的化学成分,这就需要在用炉渣覆盖电弧和将炉渣中的氧化铁回收到钢水中之间取得平衡,而这正是 Condoor 的强项,尤其是与西马克开发的工艺控制套件结合使用时。
鉴于电炉钢生产对电力的巨大需求,每个电炉都有优化能源利用和降低能耗的巨大潜力。因此,像Viridis能源和可持续性套件这样的先进的数字化能源管理系统是必不可少的。Viridis套件由紧密集成的不同应用程序组成,每个应用程序都能解决特定的挑战。这样,数字化解决方案就能实时改善能源和资源流。此外,客户还可受益于整合能源合同数据和交易的功能。除其他功能外,Viridis套件还可通过异常检测提高能源效率,并跟踪、报告和验证排放情况。
为了进一步实现数字化优化,EAFXpert 利用数据分析和机器学习来监控和优化炉子性能,提供实时洞察力和预测性维护,从而最大限度地减少停机时间,最大限度地提高生产率。
X-Pact®SynReg 的工作是确保向电极提供所需的熔炼功率,无论什么炉料。X-Pact®SynReg 具有极高的可配置性,并集成了大量历史数据库,可提供一致的最佳性能:快速电极控制、首次接触逻辑和电弧预测是系统中嵌入的部分功能,可提高能效、减少电极损耗和降低运营成本。
X-Pact®AURA 是在弱电网生产现场实现大功率熔炼的另一种解决方案。它以IGBT绝缘栅双极晶体管)技术为基础,采用模块化设计和先进的电力电子技术,可确保高效率、功率密度、电流稳定性、动态响应和可靠性,并将对电网的影响降至最低。摒弃了重型变压器和电抗器等单体设备,AURA引入了模块化概念,即通过安装在专用房间内的多个并联机柜达到所需的功率。
X-Pact®AURA 利用快速开关电子元件为直流电炉供电,通过对液浴进行强力垂直搅拌,避免炉内分层,从而增强了传热效果并降低了能源需求。
塑造未来:不断创新
尽管取得了所有这些进展,但电炉仍有很大的创新潜力,特别是在将碳足迹减少到前所未有的水平方面。最有前途的创新之一是氢气烧嘴,它使用氢气代替化石燃料,产生水蒸气而不是二氧化碳。这样,我们不仅减少了熔炼过程的碳足迹,还提高了效率。作为欧盟资助项目的一部分,氢气烧嘴的实验室测试取得了成功,目前正在意大利的工业电炉中进行测试,不久将在西班牙进行测试,随后将在整个钢铁行业更广泛地采用这一创新技术。
另一个突破性解决方案是 Allcharge,这是一种多功能加料系统,旨在优化各种金属材料(包括废钢和 DRI)的使用。Allcharge 可确保以最高效、最有效的投入组合实现稳定的质量和产量。通过优化装料,Allcharge 有助于降低能耗和减少浪费,从而进一步促进可持续性发展目标的实现。与其他解决方案相比,西马克Allcharge无需对废钢进行预热,从而限制了二恶英、挥发性有机化合物和一氧化碳的排放。此外,通过侧壁装料实现的平浴操作可减少氮氧化物的排放和对电网的影响。
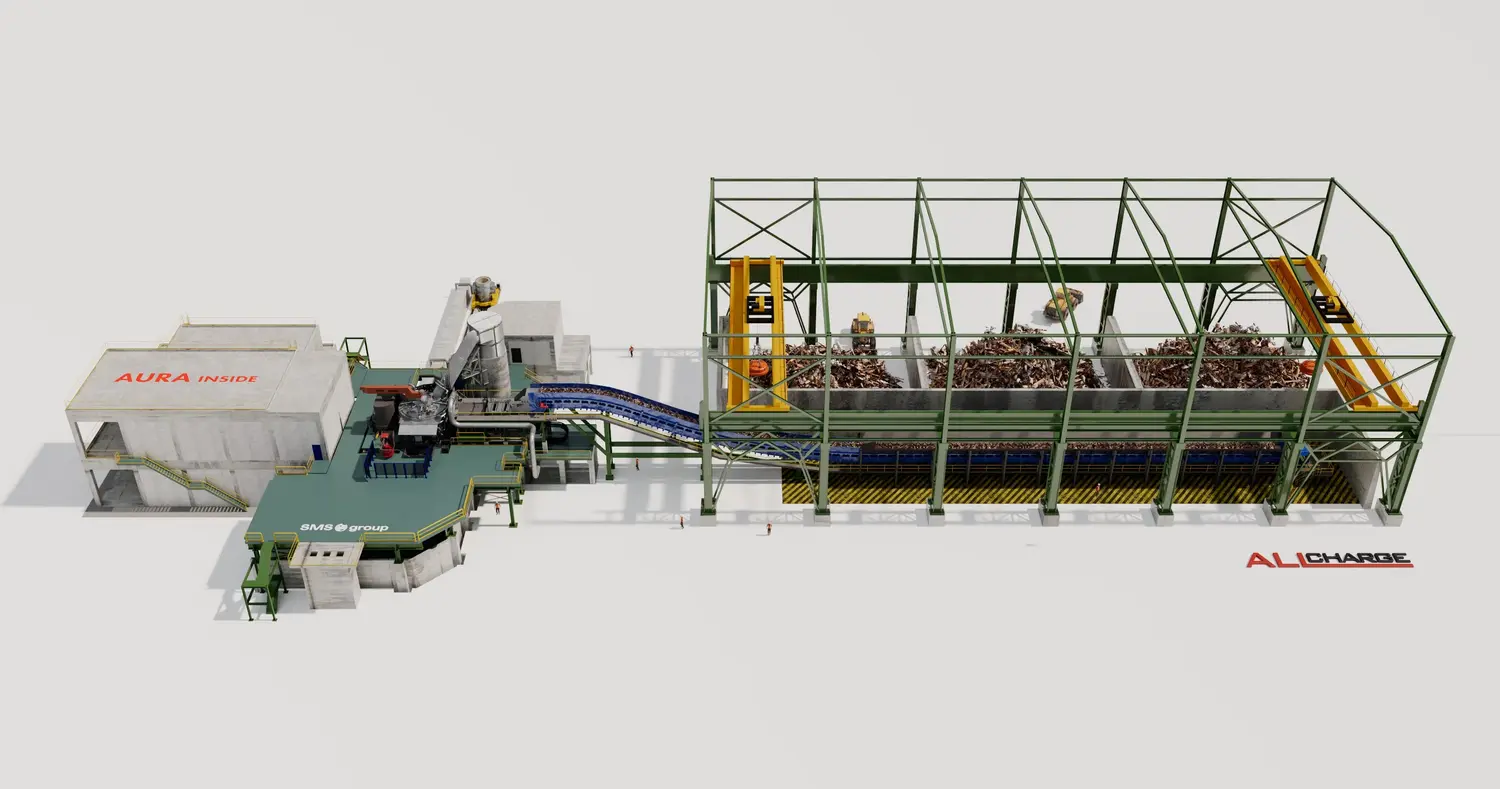