Mannesmann Stainless Tubes (MST), a company of Salzgitter AG, has awarded us the acceptance certificate for our largest-ever cold pilger mill (KPW). The KPW 370 L (Lanchester mass balancing system) is a further addition to MST's production portfolio for seamless stainless steel tubes manufactured in Remscheid, Germany.
All over the world, MST operates numerous cold pilger mills of various sizes as well as several roll grinders from SMS group and ranks as one of the leading manufacturers of seamless stainless steel and nickel-based tubes for an array of applications in, for example, the oil and gas industry, medical technology, and the chemical and automotive sectors.
"With the new cold pilger mill from SMS group, we are expanding our product portfolio to include larger pipes with outside diameters of up to 290 millimeters", says Stefan Evertz, Production Manager Precision Line / Cold Pilgering at Mannesmann Stainless Tubes Deutschland GmbH.
Customized cold pilger mill technology
The KPW 370 L operates at 65 strokes per minute and has a drive power of up to 1.55 megawatts. The 44-ton mill stand moves forward and backward 65 times a minute. As the input stock mainly comprises materials that are difficult to form, the mill stand was equipped with a specially developed hydraulic force limitation system, in order to avoid the resulting overloads.
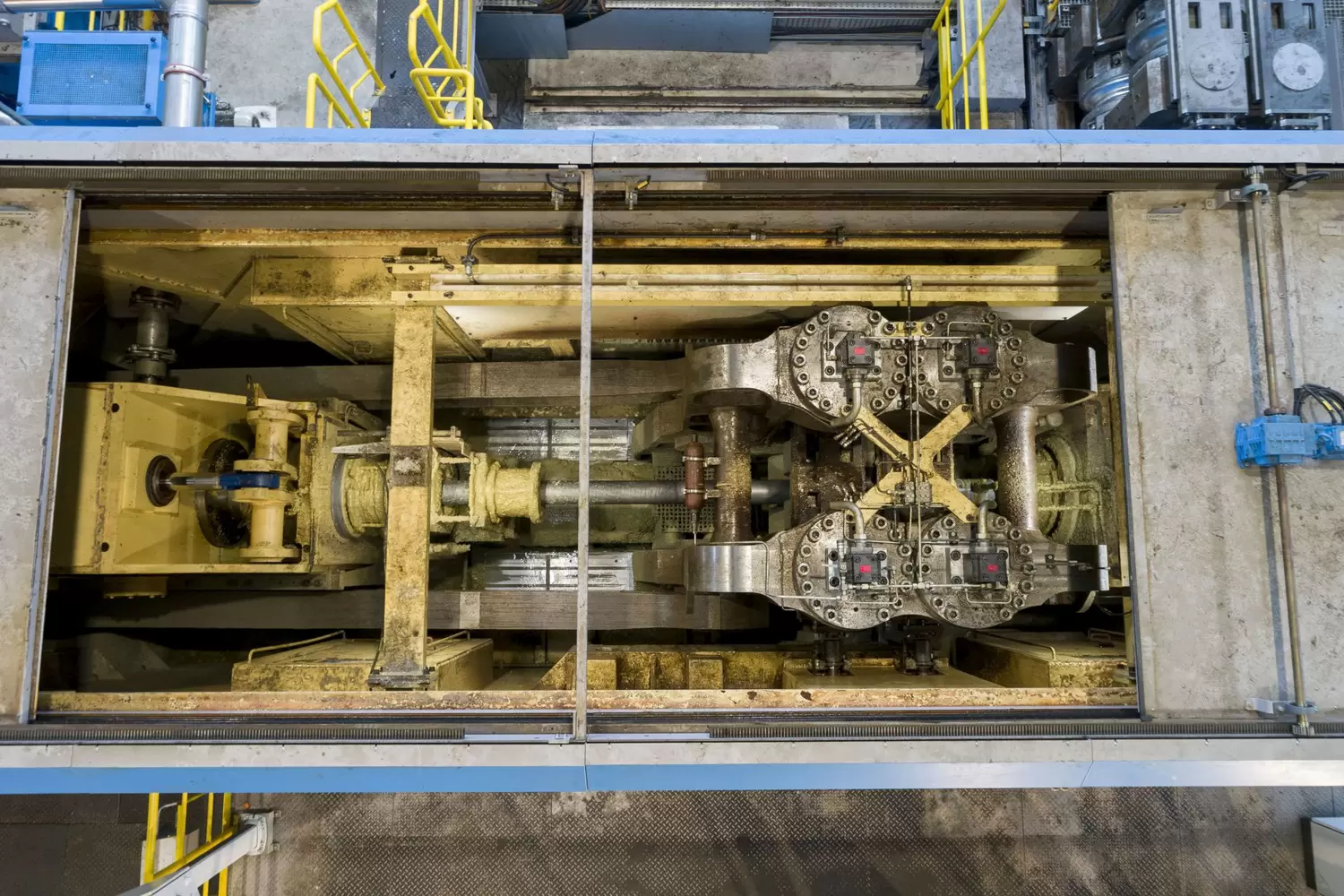
Compared with drawing and hydroforming, MST achieves closer tolerances by using the cold pilger process, which boasts higher process reliability and cross-section reductions of up to 80 percent at the same time. In order to meet the high quality requirements in terms of microstructure, strength, outside diameter, and wall thickness tolerances, SMS group has designed and built a special calibration system for the ring rolls with diameters of up to 950 millimeters. For this purpose, SMS group's production team developed a new manufacturing process.
When designing the plant, special attention was paid to the rapid conversion of the rolling mill to enable production of different sizes. As a result, a size change can be completed in less than three hours. To achieve this high flexibility, the plant was equipped with a motorized roll gap adjustment system and a changing car – for the partially automated, lateral replacement of the chock assemblies. The special design of the mill stand also allows MST to use rolling tools from a cold pilger mill supplied by SMS group that MST has been operating since 1956.
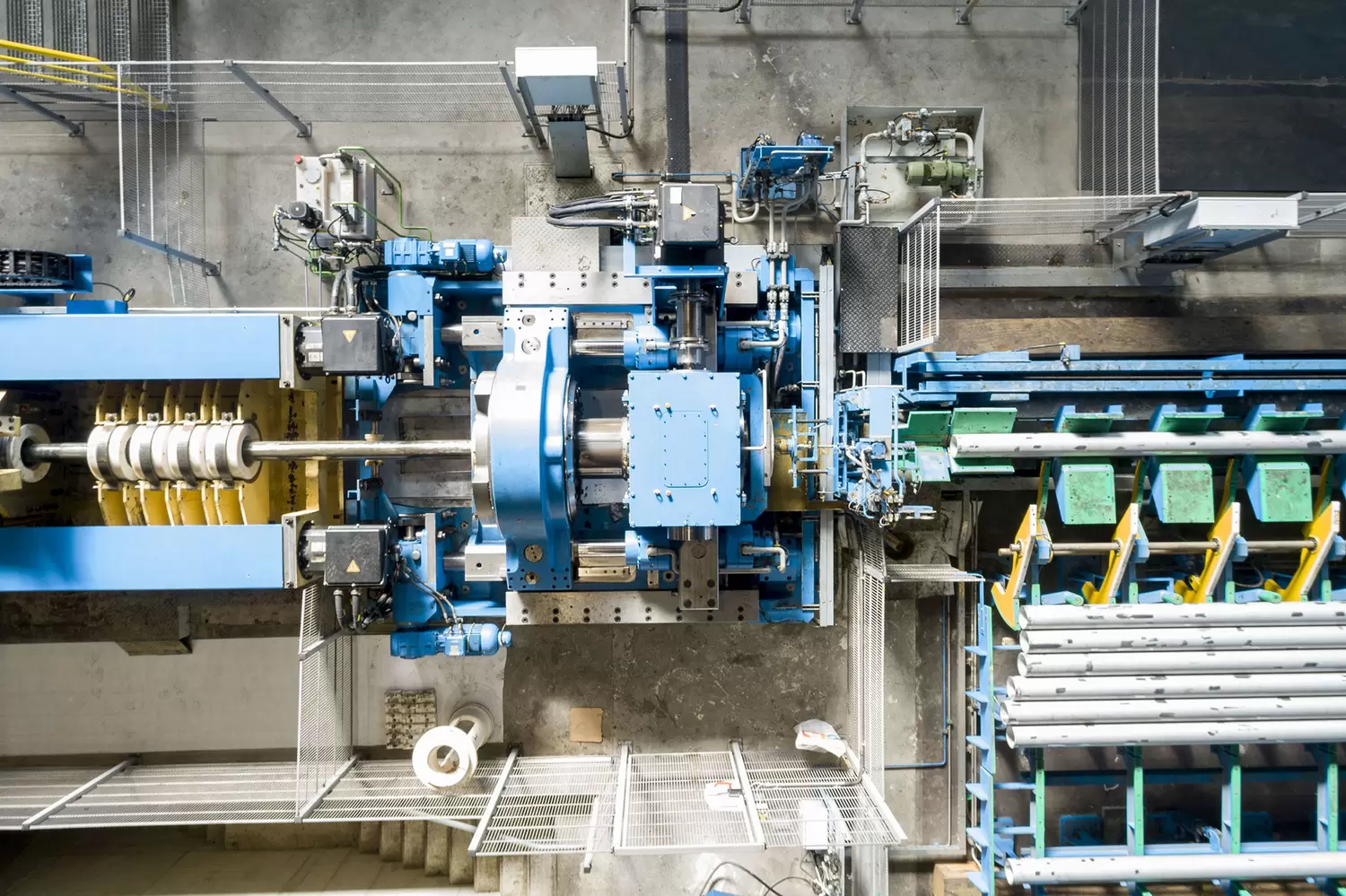
The cold pilger mill is fitted with various systems for collecting production and process data. In addition, a Genius CM® (condition monitoring) system, also supplied by SMS, is installed on the crank drive. This enables irregularities during operation and damage to the equipment to be detected early on, in order to plan timely and long-term maintenance and repair measures and thus avoid consequential damage. This means plant failures can be reduced to a minimum and downtimes for maintenance can be kept short.
Remscheid is the town where the Mannesmann brothers rolled the world's first seamless steel tube in 1886. Today, the new cold pilger mill built at this historic location represents yet another milestone in the partnership between the two companies, SMS group and MST, which has flourished since the early 20th century.