SMS group continues improving its hot rolling process models, prediction accuracy and technological controls performance efficiency. A new cross-functional model – meta model – takes an integrated temperature/microstructural approach. This takes process control to an entirely new level.
Hot rolling involves various consecutive process steps, each of which effect the mechanical properties of the product, for example - yield strength, tensile strength and low-temperature behavior. In addition, the result of the rolling process is influenced by the chemical composition of the steel and the temperature guidance during rolling. Established process control methods are able to minimize deviations from the target process parameters helping to avoid expensive claims, however rolling tests are often necessary, time-consuming and costly.
Assuring consistent quality
For the various process stages, SMS group has developed models and technological controls that enable optimum actuator adjustment and prevent the hot strip quality from being negatively affected by process variations. For many years these advances have been employed successfully in modern hot rolling mills.
Today as a result, the precision of actuator setting and control accuracy have reached very high levels. Nevertheless, the market requirements continue to be increasingly demanding, for example the rolling of ultra-high-strength steels, calls for further sophisticated optimization options. The aim is to make the process predictability and controllability even more precise – even for these increasingly challenging steels.
These types of steel grade shares have been continuously increasing in our customers’ product portfolio. Many steel producers have been adapting their production equipment to meet this trend. This goes hand in hand with the requirement allowing more flexible production planning, and more efficient utilization and linking of available process data and measured values. Consequently, the models that form the basis of process control are becoming increasingly complex.
First level: Physical models
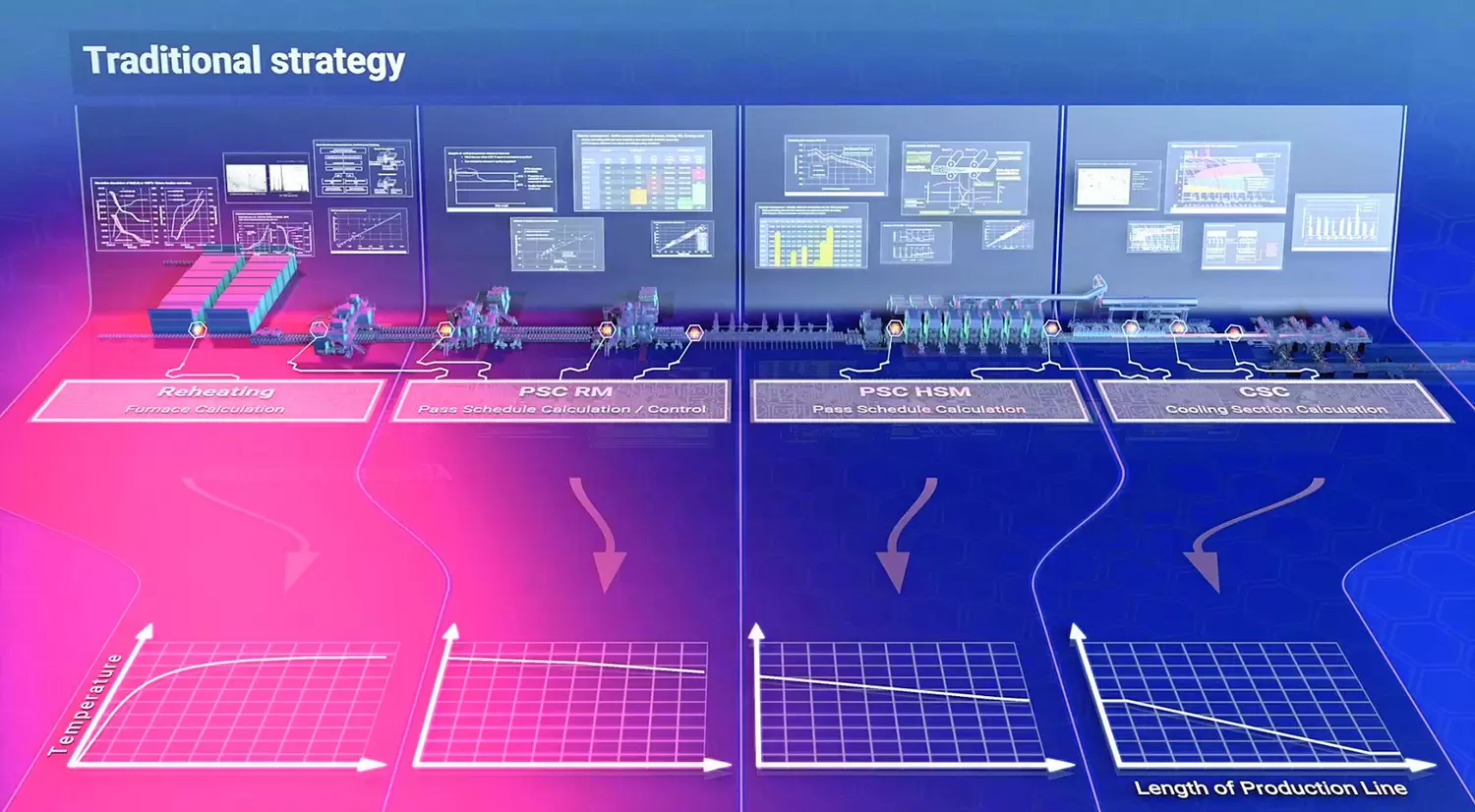
In hot rolling mills, process control is based on physical models, such as:
- X-Pact® Dynamic Furnace Control (DFC) used in CSP® plants for homogeneous slab reheating, calculation of temperature control parameters and assurance of uniform temperature distribution
- X-Pact® Pass Schedule Calculation (PSC®) for prediction of rolling forces, speeds, temperatures and gages
- X-Pact® Profile, Contour and Flatness Control (PCFC®) for profile and flatness calculation and calculation of the set-points for CVC® work roll shifting and bending, taking into consideration information from the roll state model that calculates thermal roll crown and roll wear
- X-Pact® Cooling Section Control (CSC) for calculating the water requirement taking into consideration the selected cooling strategy.
The aims of these models are to predict process parameters and set the targets for the corresponding actuators, based on physical laws and measurements. Initially, they act independently from one another, assuring the achievement of the process objectives within their respective area.
Second level: Meta models for process optimization
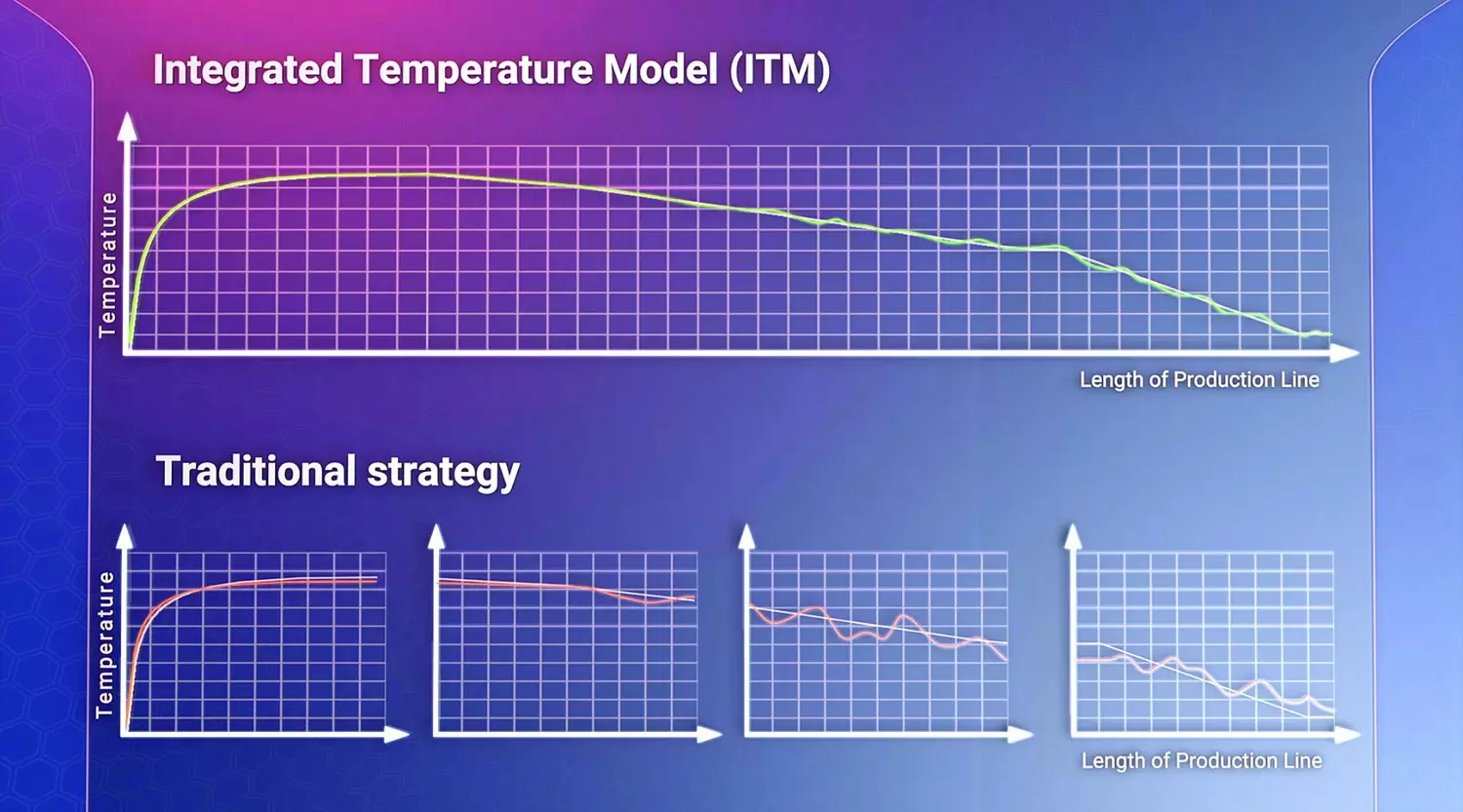
At the next level, the individual models’ knowledge about the process conditions are linked with one another and enhanced by the incorporation of material-scientific data. The interaction of temperature control in the rolling mill with the achievement of the desired mechanical properties in the produced hot strip is one example showing that SMS group has reached the next level of integration with its X-Pact® Integrated Temperature Model.
Each physical model obtains the data it needs to optimize the overall process from other relevant models, while taking into consideration correlations between the models calculation results and controls. For example, achieving the target temperature of the strip at the end of rolling is directly linked with the temperature guidance in the finishing mill. The resulting speed-time curve is intermittently updated and provides the input value for the cooling model. This enables the cooling model to anticipate variations in speed, allowing for the timely adjustment to the cooling values. This approach guarantees maximum temperature homogeneity along the complete strip length resulting in optimum mechanical properties.
Third level: The self-learning, self-optimizing meta model
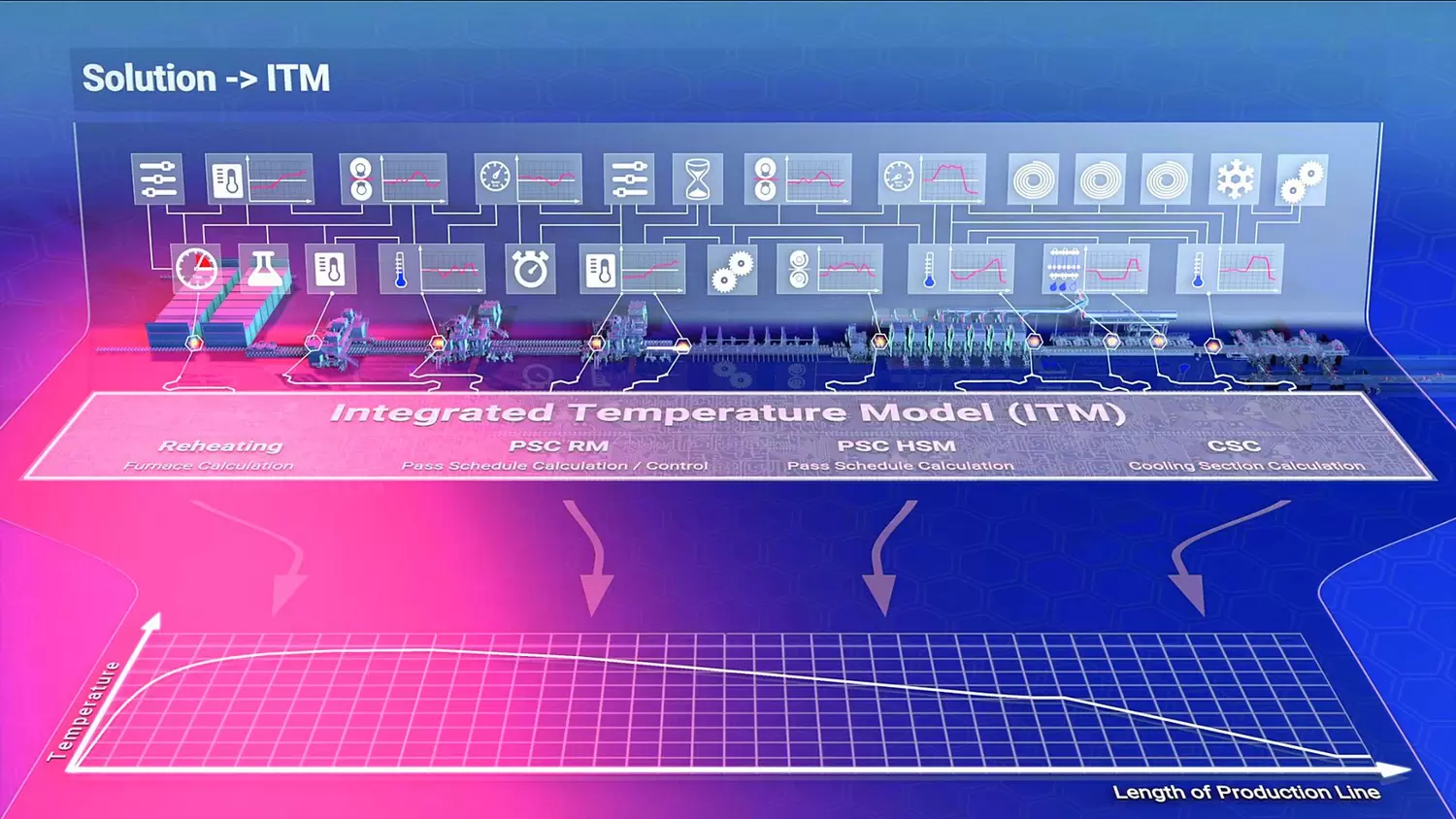
Currently, SMS group is focusing its activities to further develop its X-Pact® Integrated Temperature Model (ITM) on establishing a learning, self-optimizing meta model. In future, the ITM will be able to make recommendations for the appropriate responses to process variations, with the primary goal to further boost the product quality and yield. Additional objectives of the current development - to be achieved by establishing correlations with the X-Pact® Material Property Model (MPM) - include maximizing the production capacity, decreasing energy and water consumption and reducing alloying costs.
Read the full article with more information about the X-Pact® Integrated Temperature Modell in our next edition of the SMS group Newsletter. Register for SMS group #connect to receive the infomation when edition 02/2020 of our SMS group Newsletter is available.