MIDIS+
Manage set-points and parameter for a fully automated production
The integrated production planning system MIDIS+ (Management Information Diagnostic Indication System) is designed to manage set-points and parameters for fully automated production across all areas of forging plants. This system seamlessly synchronizes machines within a production line, such as furnaces, shears, and presses, and is compatible with non-SMS equipment and various transport vehicles, providing a holistic management solution.
By utilizing SMS technology tools, MIDIS+ generates optimized production and transport instructions, significantly enhancing operational efficiency. As a state-of-the-art web application, it offers modularity and flexibility, allowing it to adapt to specific production requirements. The system includes workplace-specific Human-Machine Interfaces (HMIs) for enhanced usability and employs a unified database, increasing awareness of plant efficiency and production scenarios. This makes MIDIS+ an ideal solution for manufacturers aiming to optimize processes and maintain a competitive advantage.
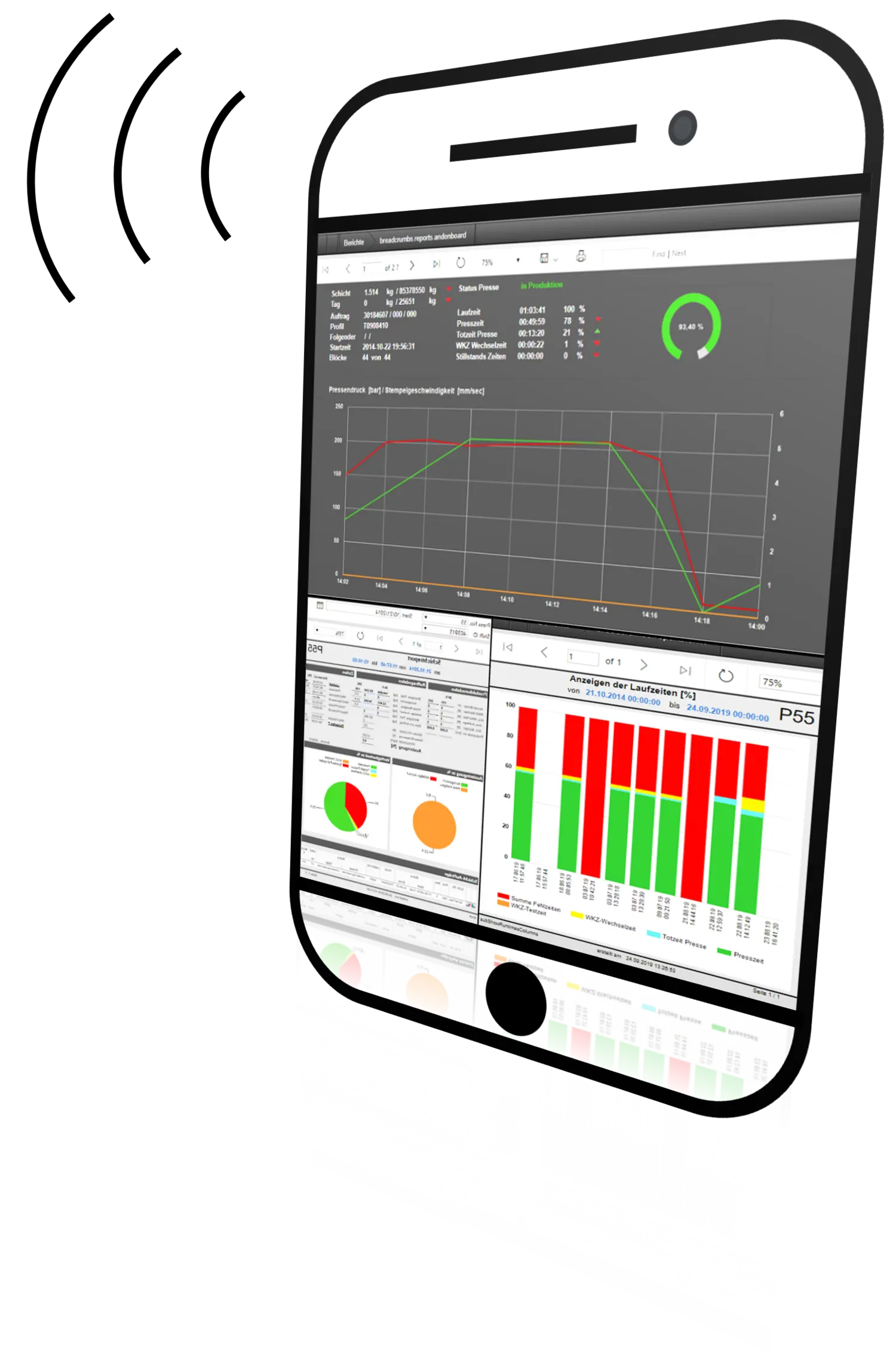
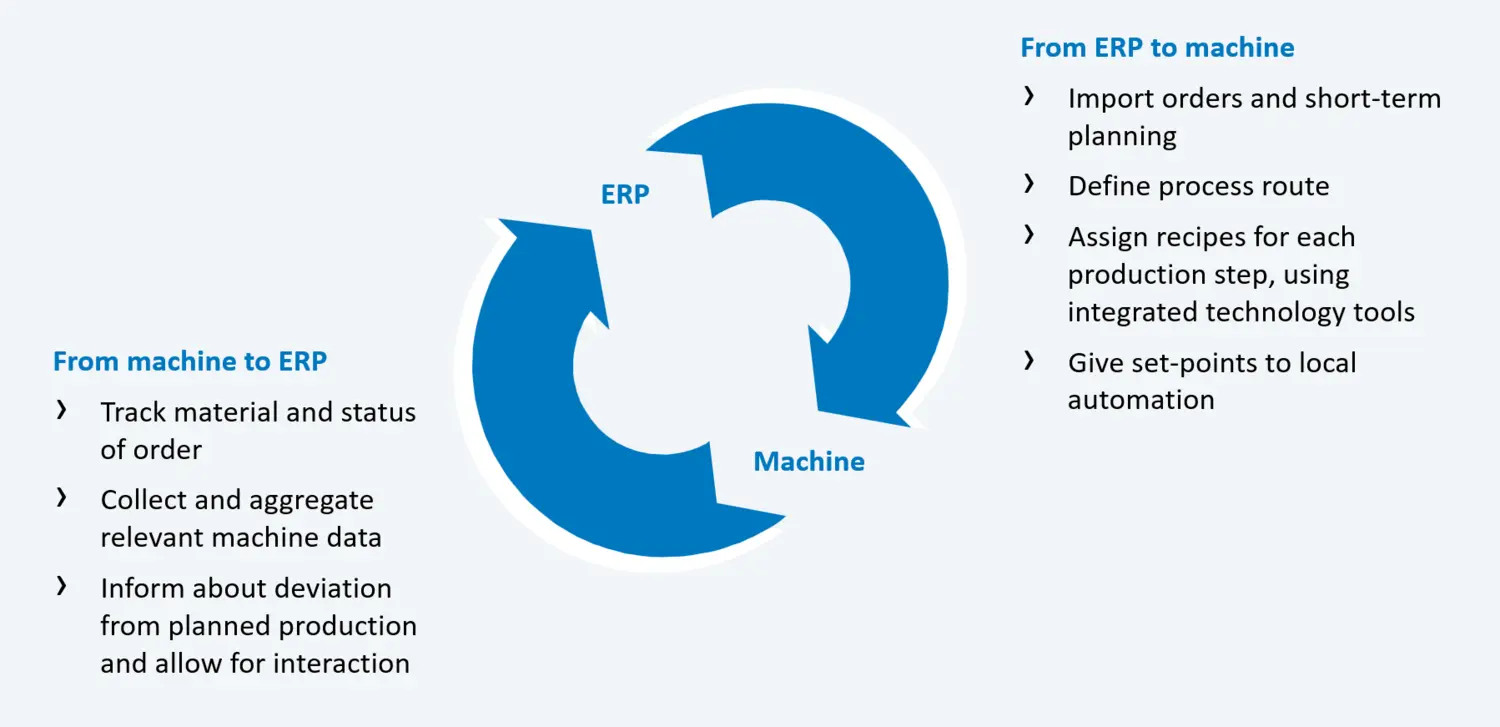
Management of Interruptions, Tools and Materials
Create data basis for further evaluation
Interruptions
Our system is designed to focus on tracking and analyzing interruption times to enhance productivity. It automatically receives the start and stop times of interruptions from the PLC, allowing for precise monitoring. Users can manually associate the reason for interruptions from a predefined list, ensuring that both interruption times and reasons are recorded in a digital and unambiguous format.
Tool Management and Order History
This feature emphasizes tracking and analyzing tool usage to extend tool lifespan. It automatically stores tool change times for subsequent evaluation. Users can select tools for each production run from a predefined list, which includes information from the die furnace. The system also automatically tracks associated production metrics such as the number of billets, weight, and length.
Materials and Alloys
Our focus is on standardizing production through the use of harmonized alloys based on machine parameters. The system stores production-relevant parameters for each alloy, such as cooling and saw parameters, ensuring consistent quality and efficiency in production processes.
Let's get in touch!
Use our contact form for questions, inquiries or personal contact.
Shift planning
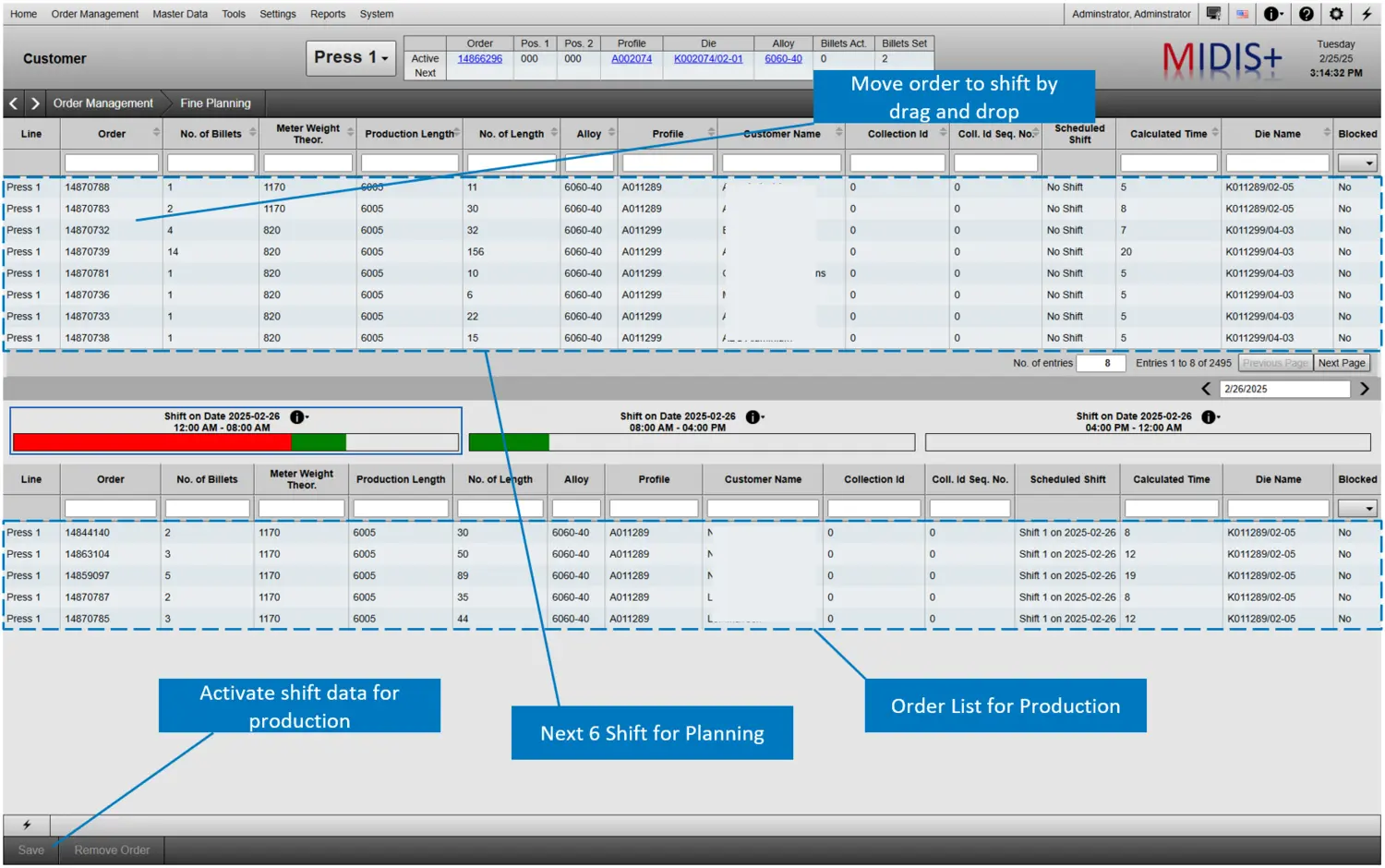
-
Online billet length optimization at the extrusion press
Example 1
In the online billet optimization, the scrap rate is minimized by choosing the optimal billet taking into account all order and process-related boundary conditions. The measured values like achieved extrusion length and press discard length is used to update the calculation continuously, reacting on die wear and other influencing factors.
-
Furnace Loading at Open Die and Radial Forging
Example 2
Loading the furnace with different sized blocks and requirements to temperature and heating times is generally a challenge. Also, tracking the actual parameters is difficult and very important for quality assurance. MIDIS+ provides special modules which visualize the furnace loading and allow the assignment of transport orders. The actual furnace temperatures and heating times are tracked, associated to the product and compared with the target values. One the one hand, this can be used for quality control.
The information is integrated in the overall transportation control system, tracking and contolling when which material is transported where.
Benefits
- Higher production due to standardized processes and high degree of automation
- Better transparency by using standard reports for production, quality, energy and maintenance
- Improved efficiency by collecting tool usage and production data
- Higher delivery reliability and better planning through evaluations of the production from the order to the material dispatch