The three ladle furnaces will process heats of 150 tons each, serving as buffering stations for the liquid steel to harmonize the production flow and enabling high-precision control of the chemical composition, temperature and castability of the steel. With the high-speed seven-strand continuous caster designed by SMS Concast, TOSYALI opted for an innovative solution: the billet caster will be designed as a combi-caster for 150-millimeter square billets and a future extension to also include the production of blooms and beam blanks. The new meltshop is scheduled to be commissioned in early September 2022.
Electrics and automation control and optimize the processes
SMS group’s scope of supply comprises the complete Level 1 and Level 2 systems with state-of-the-art technological solutions for controlling and optimizing the processes of the ladle furnaces and the continuous caster. The Level 2 systems ensure a consistently high quality and high plant availability, and support the product certification process.
Thanks to our long-standing and trustful business relationship with SMS, both teams are working together very efficiently in the realization of this project.
“Thanks to our long-standing and trustful business relationship with SMS, both teams are working together very efficiently in the realization of this project. Despite the difficult circumstances due to the pandemic we are optimistic that we will achieve our common goal of a fast and seamless project execution,” says H.I. Parlak, Project Manager of the Sariseki project at Tosyali Demir Çelik Sanayi A. Ş.
The supply of the three ladle furnaces includes SynReg, SMS group's technological package for electrode regulation. Complementing the refining tracking and control modules of the Level 2 system, it ensures maximum process efficiency and product quality while minimizing consumption of electric energy and ferroalloys. All ladle furnaces will, in addition, be equipped with a four-strand wire feeder for precise and cost-efficient adjustment of the steel’s chemical composition, an automatic temperature measuring and sampling system for accurate and consistent measurement of the liquid steel parameters, and an emergency stirring lance.
Technological and digital solutions for continuous casting
The continuous casting machine will have a 10.25-meter radius and produce 150-millimeter square sections at casting speeds of up to 5.5 meters per minute. The product portfolio will include steel grades such as rebar, low-alloyed wire rod, welding wire, high-carbon steels, cold heading steels and spring steels.
The SMS Concast technological and digital solutions will support a stable casting process: In combination with the state-of-the art CONFLOW stopper mechanism, the tundish - which will have a special geometry to accommodate the seven strands in the corresponding distances to allow for the future expansion to include blooms and beam blanks - will ensure a reliable and safe casting process. INVEX mold tubes, designed and manufactured by SMS Concast, will be applied in high-speed and SBQ billet casting. Mold and final electromagnetic stirrers (CONSTIR) will improve the inner quality of the cast products. The innovative CONDRIVE direct oscillation drive, based on advanced torque motor technology, enables online adjustment of the frequency and stroke and supports high-precision oscillation control. The CONREAD optical product recognition system from SMS Concast tracks the marked billets seamlessly down to the dispatch.
The Level 2 system of the casting machine tracks and records all quality-relevant parameters, and provides a detailed cast report for every billet/bloom. The process modules include computerized casting tracking with slice-by-slice identification for quality prediction, temperature tracking, cut length optimization, and equipment life time recording.
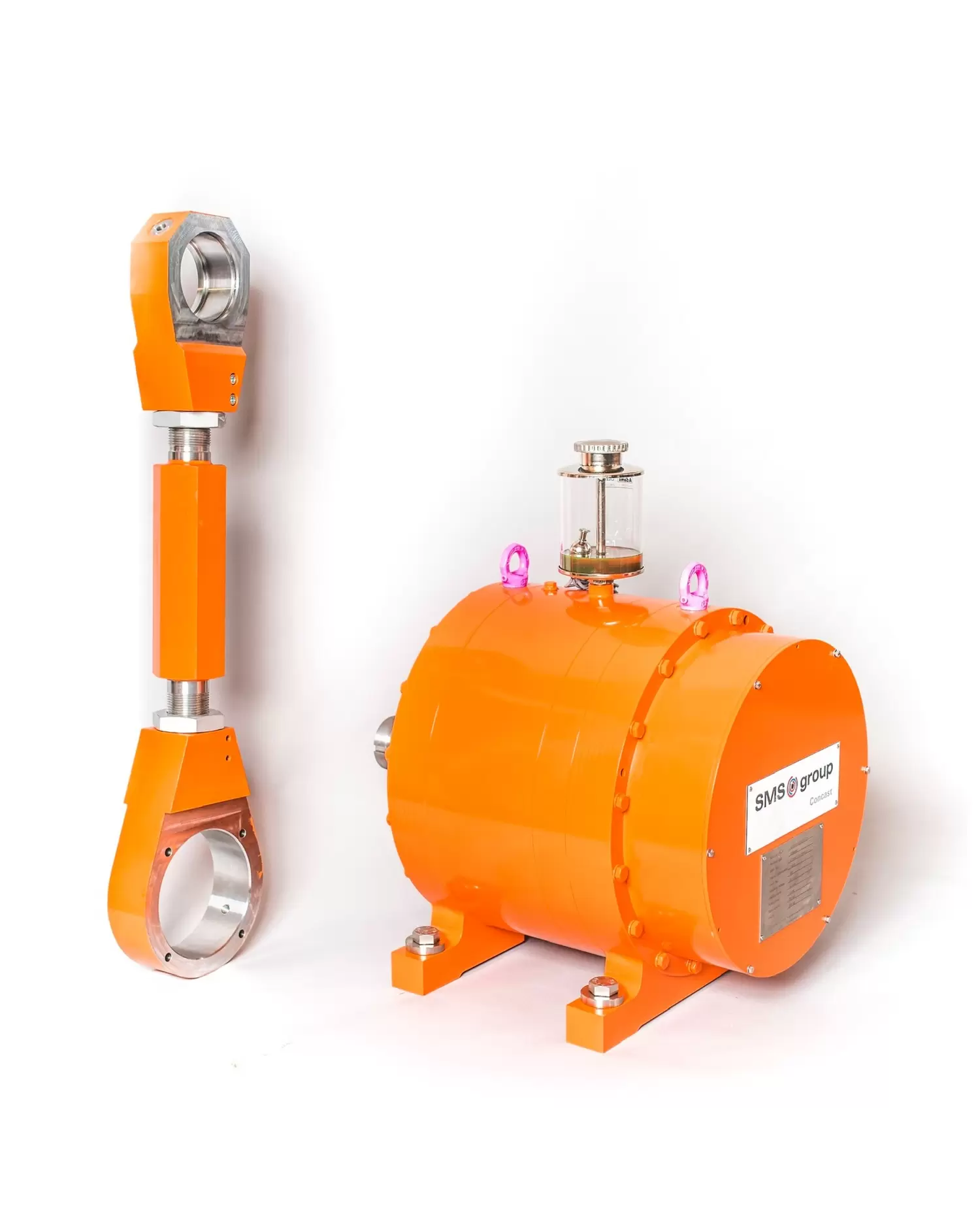