Plant overview
The plant complex of Big River Steel is located in Osceola, Arkansas, USA on the banks of the Mississippi River, well positioned to the fastest growing steel consuming region in the United States. Consequently, BRS identified profitable market segments such as HSLA, API Linepipe, OCTG grades for energy sector, extra deep drawing steels (EDDS) and AHSS steels for automotive sectors. Further CRML (cold rolled motor lamination) and NGO SP (non-grain oriented semi-processed) electrical grades are part of its product mix. In the future, BRS also intends to prepare itself for the production of CGO (conventional grain oriented silicon steel) and H-GO (high permeability grain oriented silicon steel).
In the first phase, the plant complex of BRS consists of a steelmaking plant, a single-strand CSP® plant with a capacity of 1.5 million t/ year, a PLTCM, a combined continuous annealing and hot dip galvanizing line, batch annealing furnaces and an offline skin pass mill.
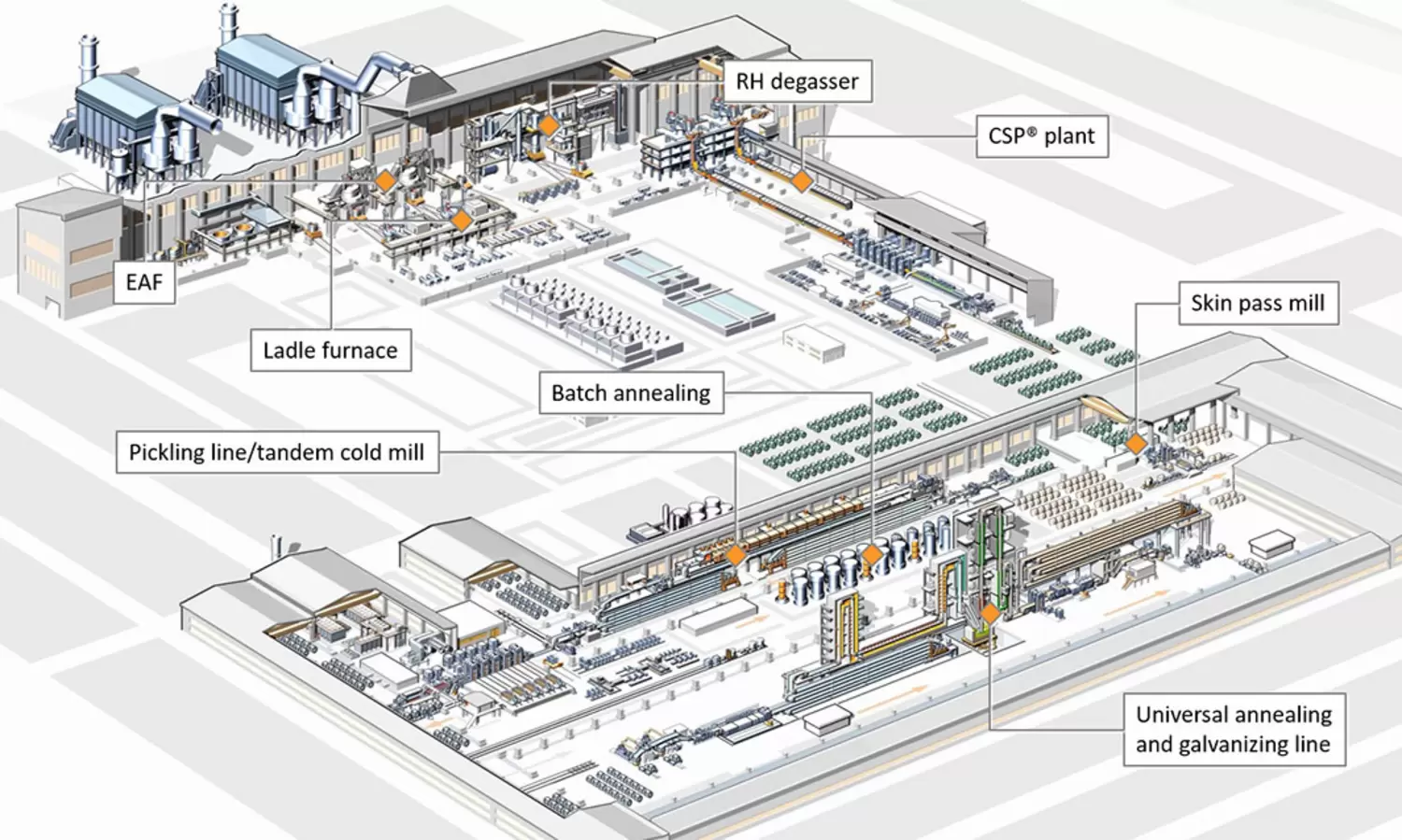
Steel making and rolling
The steel making plant consists of a direct current electrical arc furnace with a tapping weight of 150 t. Charge material includes commercial scrap grades and depending on the steel grade produced, pig iron, DRI or HBI. For metallurgical refining and alloying a ladle furnace is used designed as twin station with joint electrodes to reduce idle time due to ladle handling.
For vacuum treatment a Ruhrstahl-Heraeus (RH) degasser is installed with TOP lance for forced decarburization and chemical heating. The RH degasser has a capacity of 145 t per ladle. The process is characterized by short treatment time and flexible ladle handling. This gives BRS the opportunity of economical mass production of high quality steel grades with ultra-low carbon and low gas content. The coupling of EAF and RH degasser is the first one in North America.
The CSP® plant is designed to produce strips with a width of up to 1930 mm (76”) and a final thickness between 1.4 mm and 25.4 mm. In the first phase, the CSP® plant consist of a vertical solid bending (VSB) type CSP® caster, the CSP® furnace and the 6-stand CSP® mill with laminar cooling and downcoiler.
Read the full technical paper
- If you have already registered for SMS group Connect, please go directly to your personal dashboard: www.sms-group.com/login.
- You have not registered yet? Go to www.sms-group.com/registration and get your free SMS group Connect account.
Downstream equipment
The pickling line tandem cold mill (PLTCM) is designed to process up to 900,000 tons of steel strip per year with strip widths ranging from 914 to 1,880 mm and an entry thickness in the range of 1.4 to 5.0 mm. It is equipped with an X-Roll® laser welder, a scale breaker, a turbulence pickling section and a five stand tandem cold mill. The latter reduces the steel strip to final gauges of 0.27 to 1.4 mm. To produce pickled and oiled strip the pickling line is equipped in the exit of the pickling section with the DUMA-BANDZINK oiling machine.
The continuous annealing and hot dip galvanizing line gives great flexibility in strip processing enabling the production of coated and uncoated strips for a wide range of steel grades. This is done highly energy efficient and environmental friendly due to the intelligent I-furnace technology integrating process models and innovative online measurement technologies.
In addition, BRS uses 25 batch annealing furnaces with innovative process intelligent ensuring excellent cold strip treatment and throughput optimized operation with an annual capacity of 413.000 t. The subsequent offline Skin Pass Mill with a rolling force of 18,000 kN enable skin passing of super hard complex phase automotive grades and is capable of providing up to 13 % elongation for motor lamination grades.
CSP® technology
CSP® CASTER
The CSP® caster is a vertical solid bending (VSB) type. Slab thickness is 85 mm which can be flexibly reduced down to 55 mm by liquid core reduction (LCR). The caster is equipped with mold temperature mapping (MTM), X-Pact® solid process model, breakout detection and electromagnetic brake (EMBR) for reduced turbulence thereby improving steel internal as well as surface quality.
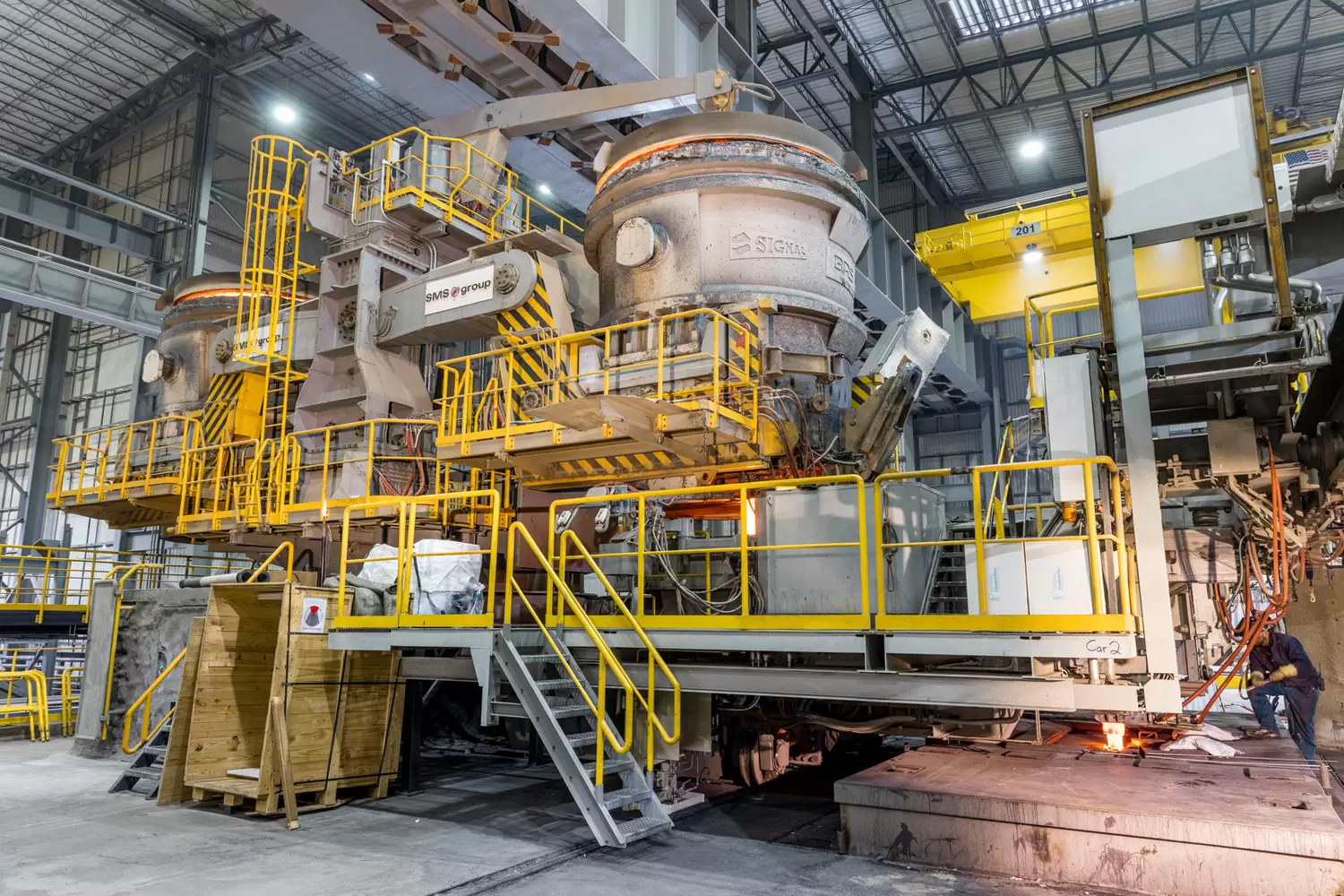
CSP® furnace
The CSP® furnace was designed to minimize energy consumption and to nevertheless achieve ideal heating-through of the thin slabs. The entire roller hearth furnace is equipped with environmentally compatible ultra-low NOx burners. At a measured average NOx emission of 85 mg/Nm³. The furnace of Big River Steel sets a standard with regard to environmental compatibility. This emission level is far below the statutory limit value.
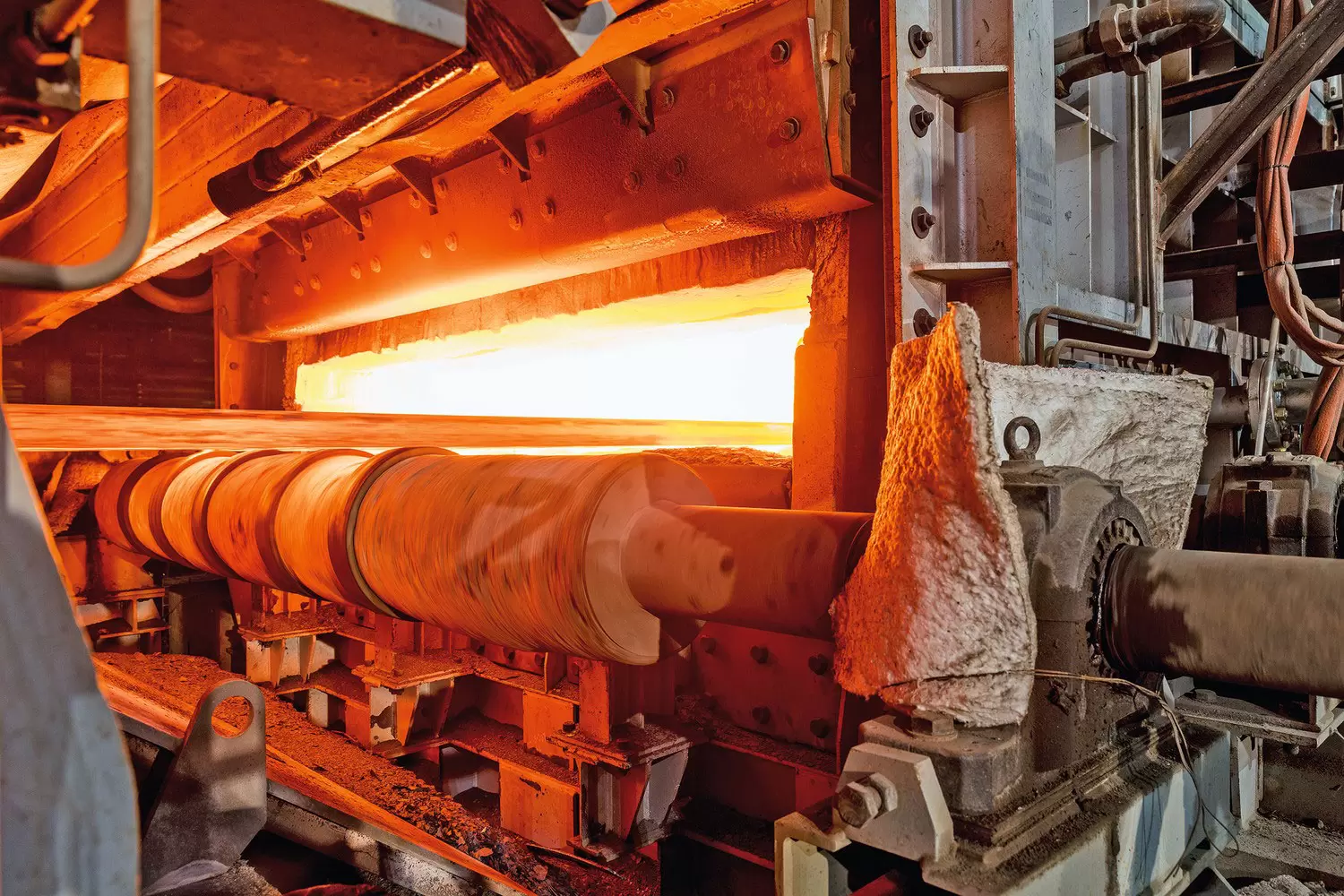
Slab transport through the furnace is carried out by water-cooled rollers with a special insulation. These rollers reduce the energy loss by more than 30 % in comparison with conventional rollers. This significant increase in energy efficiency reduces the gas consumption and hence allows saving of operating costs. The overall reduction of energy consumption in the furnace is more than 20 %. Energy consumption of the furnace when fed with slabs with a cross-section of 65 mm x 1800 mm and a casting speed of 5.0 m/minute is as low as 35.2 kWh/t over 100 m of furnace length.
The control of the furnace uses the powerful X-Pact® Dynamic Furnace Control Model (DFC). This model ensures the heating of the slab to the desired temperature at a high degree of uniformity over length, width and thickness.
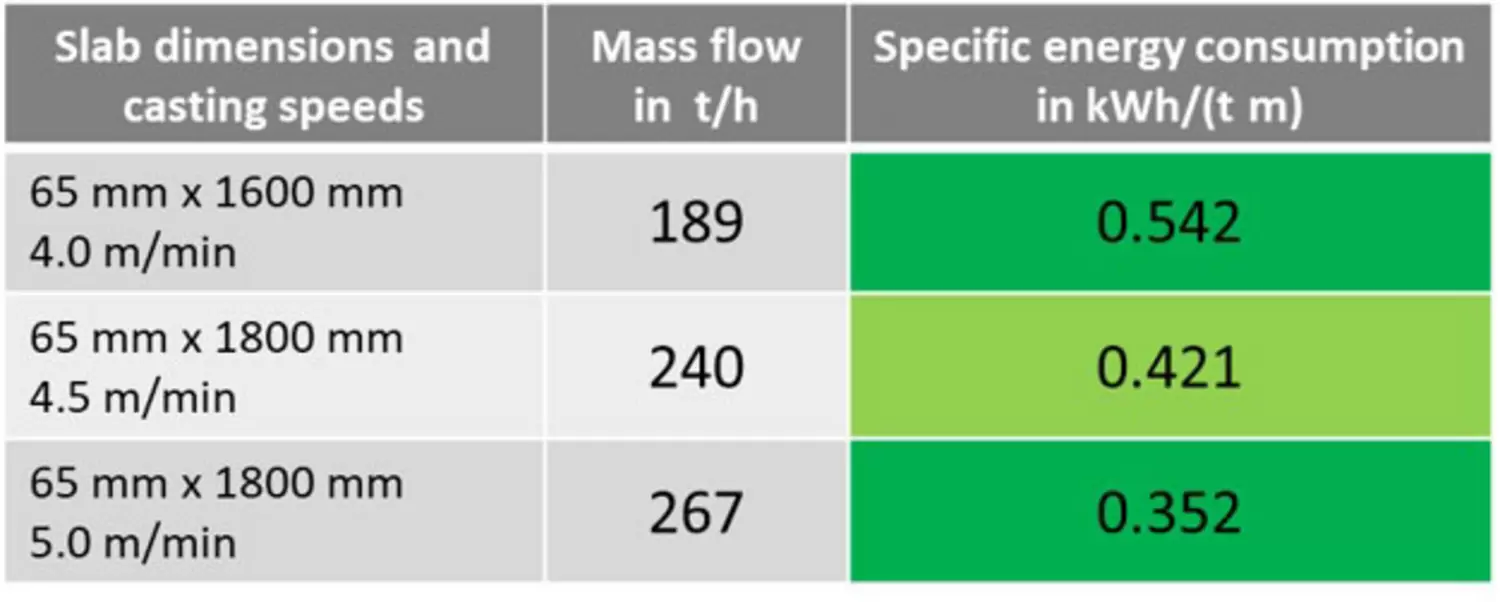
CSP® mill
The 6-stand CSP® rolling mill is fitted with all technologies and components for the cost-effective production of high-quality hot strip with excellent product tolerances. These include the advanced guiding system to improve strip stirring, the latest descaling technology, hydraulic gauge adjustment, CVC plus® technology, as well as an advanced Level 2 system with material property model to ensure product quality and to reduce the development time for new products.
The laminar cooling is equipped with 12 groups. 3 groups are designed as super reinforced zones, 8 as micro zones and 1 as trimming zone. All groups are equipped with latest version of the edge masking, able to follow the strip edge. It improves the mechanical properties near the strip edge, the temperature profile across the width and thus the flatness of the hot rolled strip in cold condition.
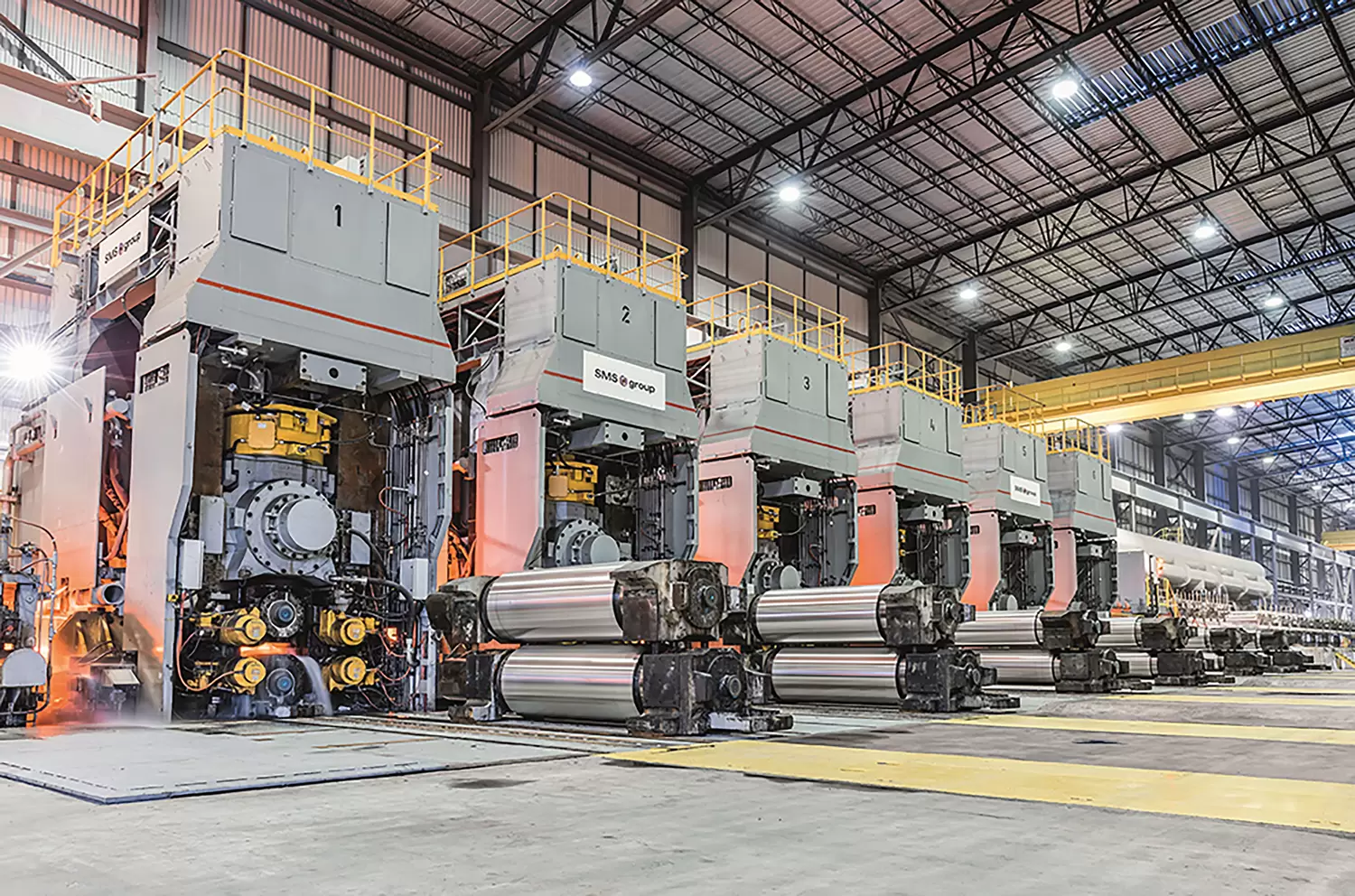
Operational results
RAMP-UP OF PRODUCTION
The CSP® plant produced its first strip on 11 December 2016. In January 2017, in the first full month of production, a total of 58,000 metric tons (63,000 American short tons) left the plant - this quantity was the world record for all CSP® plants. In early November 2017, Big River Steel surpassed the mark of one million tons produced on the CSP® plant with one strand. Two years after the first coil BRS has already produced 2.67 million tons and exceeded the rated capacity of 1.5 million tons per year during 2018.
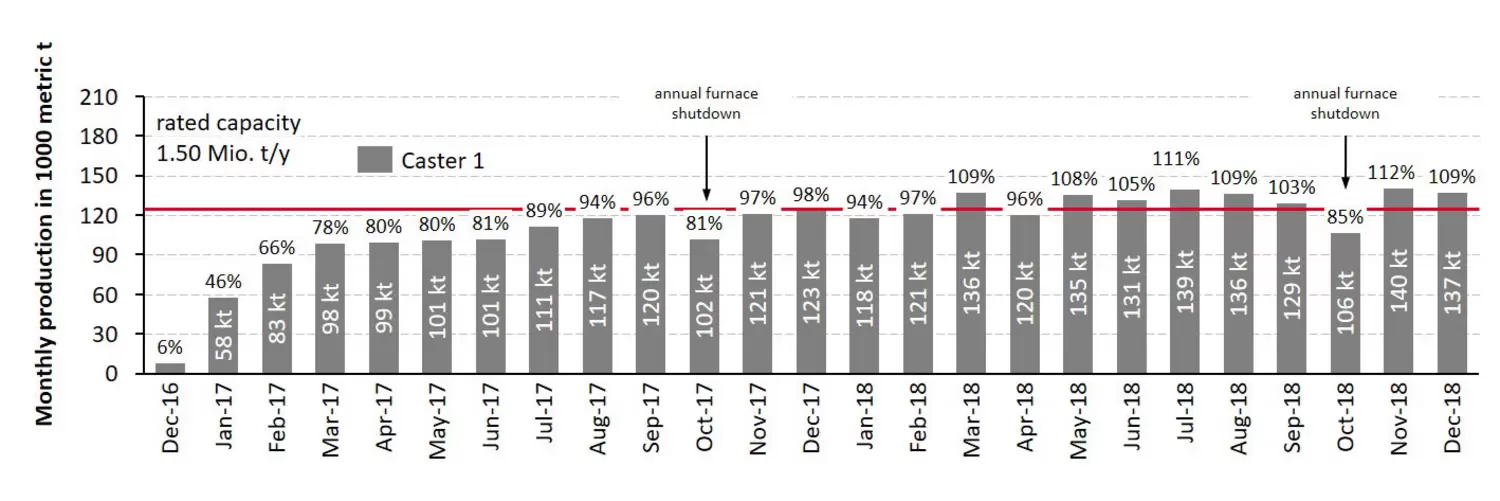
Flexible production
Many customers expect from Big River Steel as a newcomer in the market very high flexibility with regard to product quality, product dimensions, lot sizes and delivery time. On account of the best plant dimensioning in every process step and the digitalization of the whole plant, all these expectations can be met at a mean lot size of only 7 coils. Almost 50 percent of the strips produced have a width of more than 1500 mm.
The CSP® plant is of decisive importance for the flexibility of Big River Steel. Within one sequence, considerable changes of the strip width can be effected. Strip thickness variations of more than 10 mm are realized from strip to strip.
Moreover, in the case depicted here, four different steel grades are cast within the sequence. This flexibility is a decisive factor of success for Big River Steel. On one hand it is a benefit yielded by the CSP® technology due to temperature homogeneity and CVC plus® technology and on the other hand it is economically feasible due to advanced functionality to reduce the length and the number of transition slab or strips like the flexible analysis approach implemented in the Level 3 system X-Pact® MES 4.0. It reduces the number of transfer slab by more than 50 percent and saves BRS millions of dollars already during the first two years.
Within an implementation period of 8 weeks, the PQA® system was able to do its job and is now fully utilized in the day to day dispatching. The fundamental benefit of the PQA® system is that only products without defects leave the plant, which is very important for the development of a long-standing customer-supplier relationship.
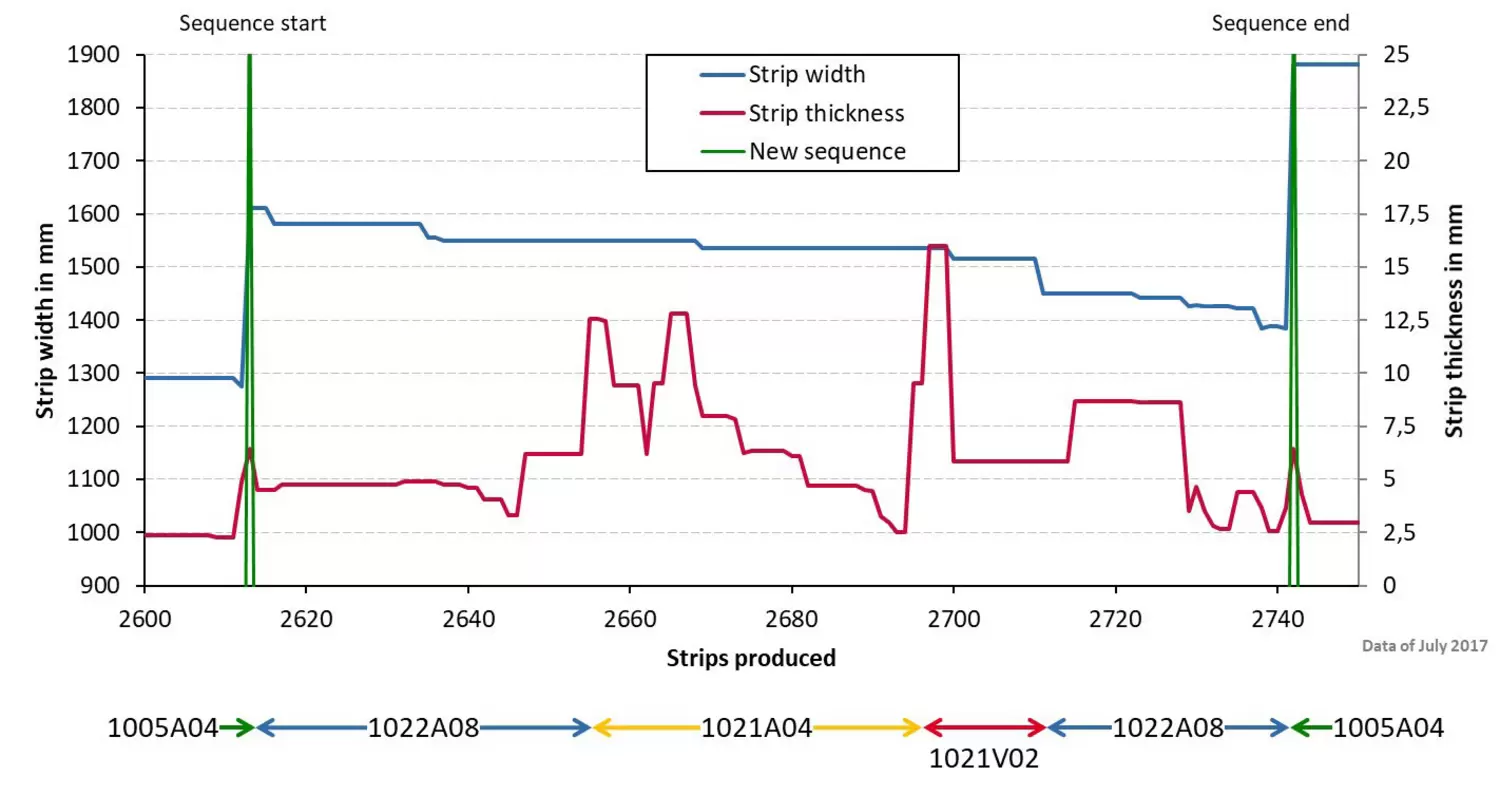
Steel grades: API line pipe
Just few months after the first coil attempts were made to gradually develop OCTG grades, API line pipe grades from X52 to X80, AHSS HSLA steels and extra deep drawing grades for automotive sectors. The RH degasser was commissioned in July 2017. With the first heat run through RH degasser on July 28, 2017 development started for API line pipe grades sour and non-sour applications, electrical steels and extra deep drawing (EDD) grades.
The trails of X52 and J55 for tubular applications were conducted at the request of key ERW/HFW pipe manufacturers and are now commercially produced successfully. The first trial for the production of API X70 grade hot rolled skelp in 12.5 mm thickness was set up in August 2017 for both sour and non-sour gas applications.
Considering the high levels of internal cleanliness witnessed at BRS and thicker slab dimensions that can be used, chemistry of first API X70 trial heat was designed. Two heats were made one through EAF-LMF-CC route and the other through EAF-LMF-RH-CC route and the heats were cast in to 80mm thick slabs and thermo-mechanically processed to 12.5 mm thick hot rolled coils.

The picture shows full size transverse Charpy impact values of X70 samples. Drop weight Tear Tests (DWTT) were conducted at temperature down to minus 45 °C and all the samples revealed excellent shear down to that temperature. The requested mechanical properties of API X70 could be successfully obtained in the 12.5 mm thick hot rolled strips.
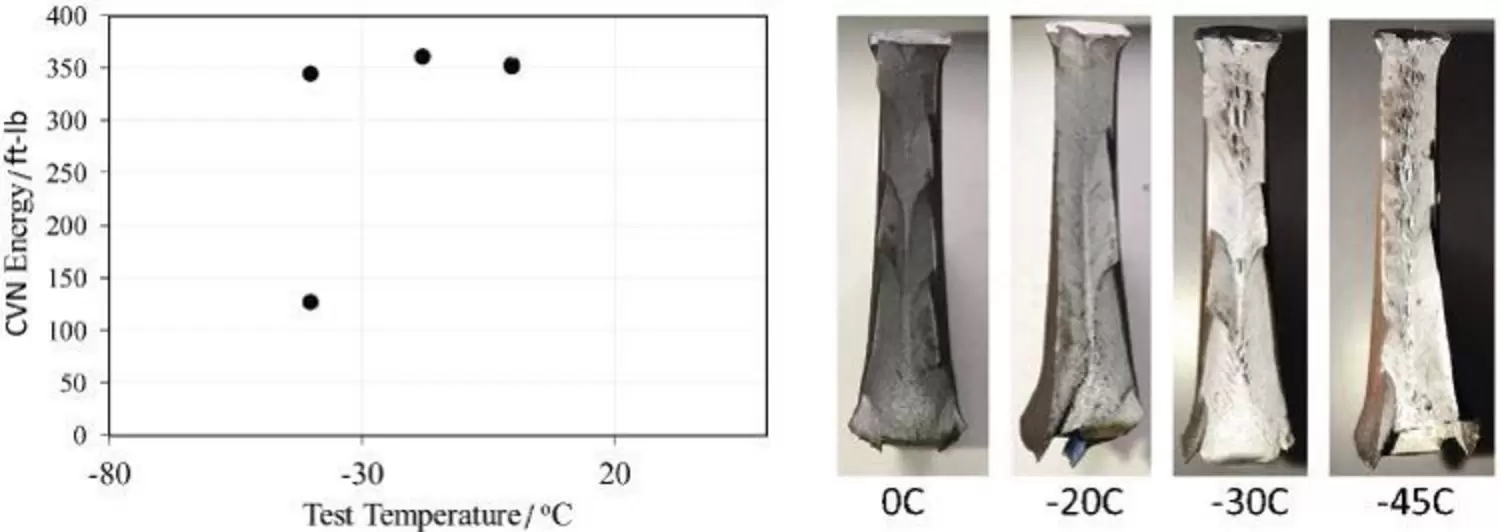
Samples were tested for HIC resistance as per NACE 0284-16 specification in solution A. The tests indicating outstanding HIC resistance of the X70 grade steel produced. Macrographs of specimens before and after HIC tests showed no hydrogen blister formation on the surfaces.
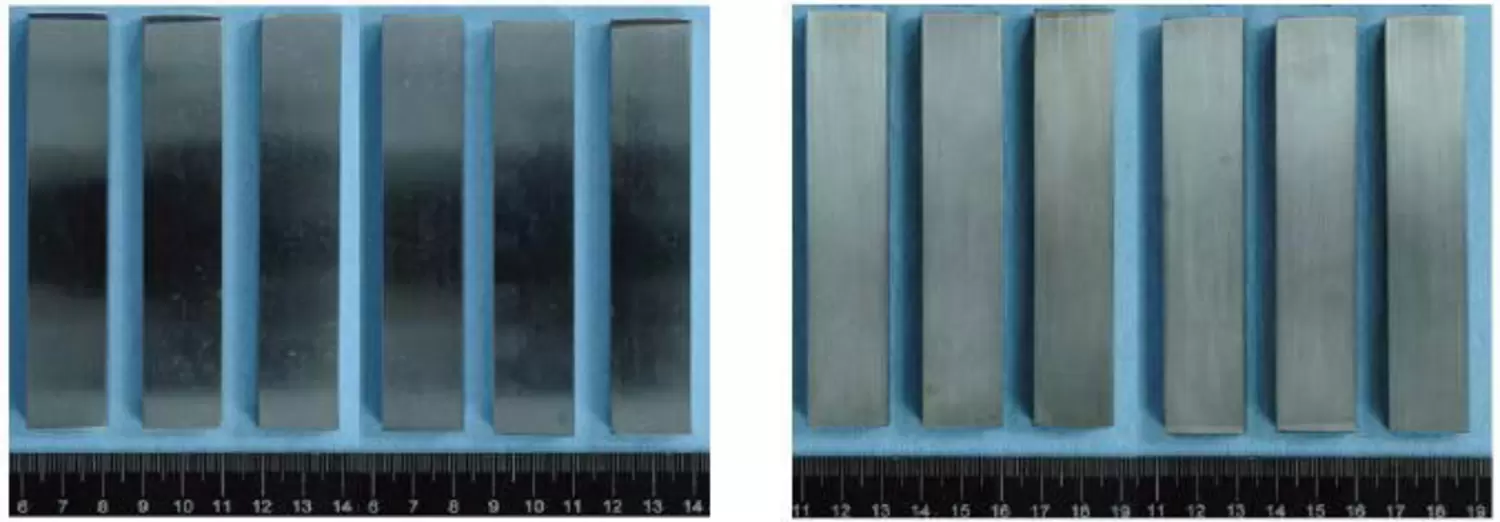
Steel grades: Advanced high-strength steel grades (AHSS)
Regarding AHSS, the first trials for the production of the family of dual-phase steels were held in December 2017 and low carbon chemistry was adopted for the production of DP590 to avoid peritectic behavior of the steel. The steel was hot rolled to 3.3 mm and was finish processed to 1 mm thick galvanized coil.
Steel grades: Electrical grades
One of the prime production targets for BRS will be electrical grades of steels considering the growth of electric cars in US market and beyond. The combination of EAF-LMF-RH–CC production sequence perfectly suits BRS for the production of electrical grades of steels. BRS skin pass mill is capable of delivering a temper pass reduction of up to 10 % and the Hi-Flo Batch annealing furnaces with 100 % Hydrogen atmosphere are capable of annealing at high temperatures required of motor lamination and semi-finished NGO electrical steels.
In January 2018, Big River Steel first attempted one trial heat of 0.4Si electrical steel with less than 50 ppm carbon. The heat was processed through EAF-LMF-RH-LMF-CC. The steel was cast in to 65 mm thick slabs and hot rolled to 3.30 mm, 2.74 mm and 2.44 mm thin hot bands. Hot band coils were processed through pickle line, cold rolled followed by batch annealing at targeted temperatures. The annealed coils were skin passed and then successful further processed at customer side. Also trails with Si content of 1.3 % and 1.6 % for motor laminations are done during 2018.