In the world of advanced manufacturing, the emergence of isothermal forging plants marks a significant milestone. This leading-edge technology is designed to manufacture workpieces with near-net-shape precision, all with in a controlled, constant high-temperature environment. The advantage of this process lies in its execution under vacuum conditions, with both the tools and workpieces maintained at constant forging temperature.
The aerospace and energy sectors among others, require components capable of withstanding high mechanical and thermal stresses. To meet these requirements, innovative materials must be used to produce the large components involved. This emphasizes the importance of cost-effective solutions that bring substantial savings and make isothermal forging plants a smart investment decision.
Up to now, isothermal forging lines were developed by the aerospace industry suppliers themselves. They used their own knowledge to meet the certification requirements of aircraft turbines and aerospace industry material qualities. These suppliers procured the individual units, such as the isothermal forging press, vacuum chamber and heating unit, as well as the isothermal tools themselves to develop all the interfaces.
Elevating industry standards through integration
We combined our experience in forging press equipment with our proven vacuum technology used in secondary and tertiary metallurgy, a standard feature of these isothermal forging plants. The integration of the tool tower (die stack and state-of-the-art heating technology along with our process expertise has produced an optimal system capable of processing a diverse range of future materials.
Concept
Features
1. Hydraulic closed-die forging press
2. Loading and unloading chambers with integrated furnaces for heating the workpieces
3. Unique charging chamber with integrated manipulator
4. HIF chamber with combined heating furnaces for the upper and lower dies
5. Tool chambers for exchanging the upper and lower dies
6. Vacuum slide gates
7. Charging chamber with integrated handling cars for upper and lower dies
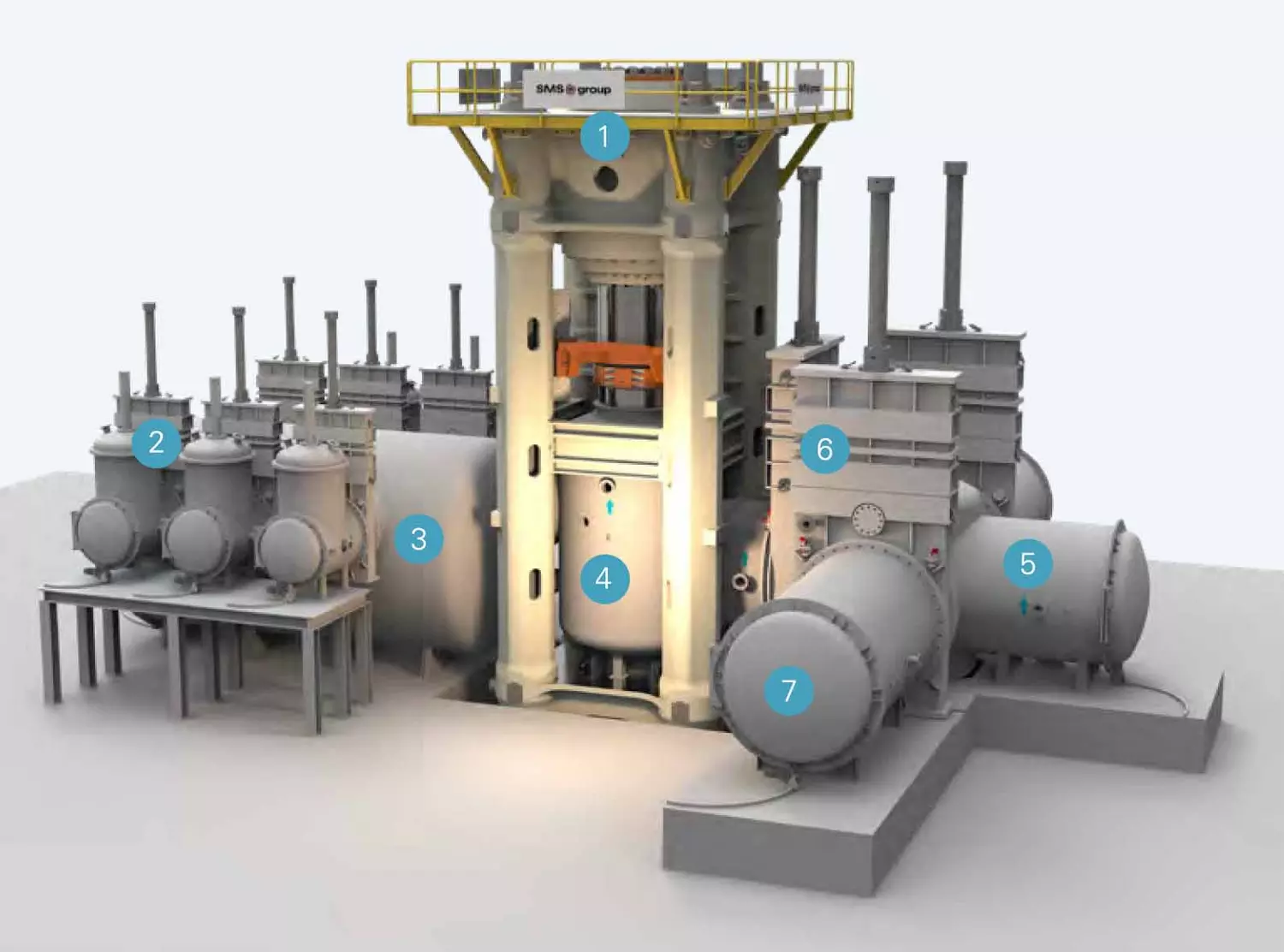
The hot isothermal forging (HIF) line is seamlessly integrated without any interfaces. Our innovative approach is based on the round, multi-vacuum chamber design. In the HIF line chamber, a stable synchronization of temperatures between the workpiece and the dies is maintained throughout the entire forging process. Achieving this balance is possible thanks to the use of vacuum heating furnace technology, which heats both the upper and lower dies and the workpiece.
One notable innovation is the utilization of ceramic blocks for thermal insulation of the tools. These ceramic blocks are highly effective, particularly under the tremendous forging forces. Moreover, the insulation plays a crucial role in protecting the press components from excessive heat. The hydraulic system in the forging press is characterized by tightly controlled strain rates, which enable precise speed and force control. This system is designed with an energy saving concept in mind and boasts a dynamic behavior system for the hydraulic unit, thereby optimizing the overall performance.
Heating furnaces are equipped with multi-zone heating elements, allowing for precise temperature control and uniform heating. To guarantee optimal quality of the final product, a monitoring system is implemented for both the workpiece and the dies. The vacuum unit with integrated mechanical vacuum pumps and filter units achieves the required vacuum level for the HIF process.
The power management system includes the power supply for the furnaces as well as ancillary supply and operating facilities, ensuring seamless operation throughout the forging process.
To oversee and manage the entire HIF line, a control and monitoring system, integrated into a broader digitalization framework, is used. Additionally, the system is supported by our “Management Information Diagnostic Indication System” digital platform, thus enhancing the overall efficiency and reliability of the forging process.
Benefits
- Precise forging
- Strict temperature control within a narrow range
- Prevention of redox reactions
- Elimination of potential negative material properties such as macrostructure and micro-crack formation
- Optimization of the metallurgical parameters
- Large turbine discs easier to produce
- Fully automated
- Safe and rapid certification of processes, resulting in lower costs for the aerospace industry