For pipelines, the right corrosion protection is most important when it comes to durability and resistance of the pipes used. With PERFECT spray®, SMS group is able to apply an almost pore-free thermal layer.
Expansion and safeguarding of energy infrastructure becomes increasingly more important. The worldwide pipeline network includes more than three million kilometers and it is growing every year by about 25,000 kilometers. Pipelines are the lifelines supplying the world with essential raw materials and are indispensable for transporting oil, gas and drinking water over long distances. The pipelines are partly exposed to severe conditions. No matter whether piped on above-ground pipe routes, in the ground or under water – the right corrosion protection is the alpha and omega when it comes to durability and resistance of the pipes used. This is where wire arc spraying comes into play – a process characterized by high application rates and low energy consumption.
Wire arc spraying systems of the latest generation
SMS group brings together two promising technologies: wire arc spraying and an all-digital current/voltage source developed in-house. This resulted in the thermal arc spray system PERFECT spray® − for the treatment of metallic and non-metallic surfaces.
With the wire arc spraying system for thermal spraying according to DIN EN ISO 14917, SMS group opens up whole new markets in the corrosion, wear protection and servicing sectors: due to control-specific and design-related disadvantages of wire arc systems available on the market, end users had to accept significant restrictions regarding layer quality and process efficiency till now. Through new approaches in electric arc control, an open linear design and the development of SMS group’s own gun concept with pressure-loss-optimized, turbulence-reduced and high-expanding nozzle system significant improvements in process efficiency and layer quality can be achieved.
The new wire arc system is modular in design and includes ceramic inner flow contours adapted to the corresponding coating application which have been engineered to gas-dynamic factors and can be adapted to the desired gas flow rate or mass flow. There is the possibility to direct the gas flow to the wire ends in a clear supersonic range (gas flow velocity larger Mach 1) or retard the gas to subsonic speed – depending on material or application case.
It is possible to process almost all metallic materials which are deliverable in wire form. By the option of separately controlled wire feeds different cathode- and anode-side materials can be processed, to produce alloys and pseudo-alloys in the process (for example a combination of steel and nickel or aluminum and copper).
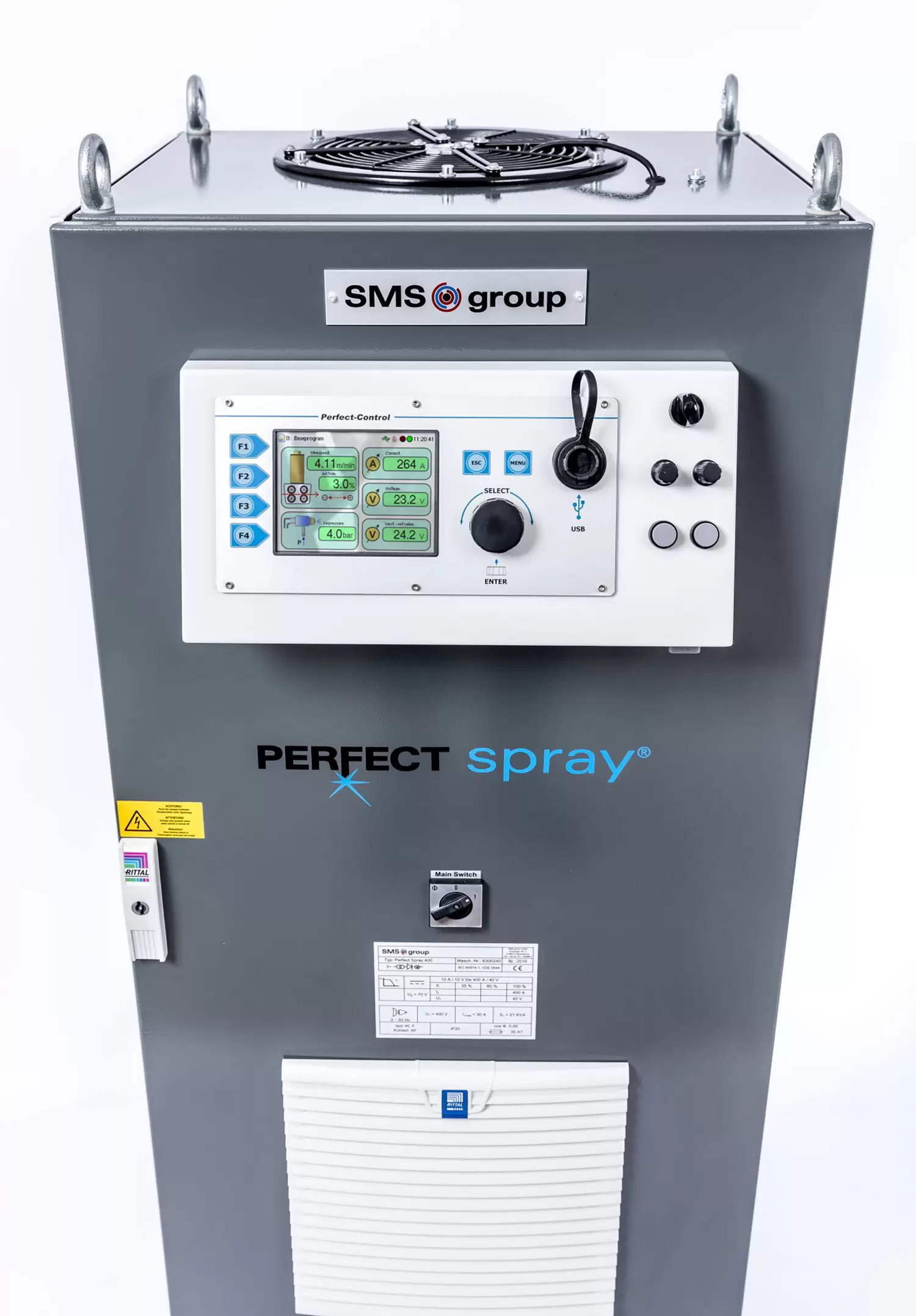
Homogenous spraying process, excellent coating quality
This is what PERFECT spray® offers:
- A precise and ultrafast process control
- Full parameter control of power supply for processing different wire materials and diameters
- An innovative nozzle concept for generating high-speed gas flow
- A wear-resistant and process-safe wire contacting concept
- A maintenance-friendly gun and highly functional, durable materials for all system components
The highlight of PERFECT spray® is the active process control by fully parameterizable current voltage source in connection with active adaptation of the characteristic field depending on the respective wire-shaped metallic filler material.
Cost-, energy and material-efficient technology
Current issues and problems of a politically motivated turnaround in energy policy bring coating methods such as wire arc spraying into the focus of technologies which can guarantee long-time corrosion protection in a cost-, energy- and material-efficient manner. Material systems suitable for this task are alloys on the basis of aluminum-zinc which can be processed as pre-alloyed AlZn wire or by using different wires (anodic: zinc; cathodic: aluminum). The SMS group coating system PERFECT spray® enables almost pore-free coating. Because of the possibility of controlling wire feed velocities of cathode and anode separately materials of different melting temperatures can be conveyed homogeneously, which makes it possible that a constant arc resistance (minimal length variation) is adjusted. The layers are additionally post-treated with a special sealant on Sol-Gel basis and guarantee with recent standards and depending on layer thickness corrosion protection for more than 20 years – even under heavy seawater weathering.
With a future-oriented PERFECT spray® the spraying unit is not only perfect for application in an industrial environment, but also qualifies it for science and research to open up new resource-saving applications and markets.