投资于我们的未来
Lightness.NRW - 开发材料和工艺,以便在可大规模生产的超轻设计中利用可回收、环保和最高强度的铝合金,为未来的交通服务。
摘要
由于各种原因,汽车行业在短期和中期内都面临着设计和制造轻型汽车的巨大压力。
因此,铝生产商不遗余力地开发新的高强度铝合金,并将目光投向未来,希望用这种合金赢得大宗订单,作为钢材的竞争对手。然而,就高强度铝合金而言,在汽车设计中必须考虑的一个缺点是缺乏成本效益高的制造技术,这种技术不仅要适应这种高强度合金,而且要适合大规模生产。这给社会带来的巨大效益的技术并不能只用于顶级车型的研发上,相反,我们需要的是可用于所有车型的轻量化系统。
由此产生的项目联合体是有目的的,即所有必要的开发阶段,包括一项新的、可申请专利的生产技术,都由全球知名企业参与:从开发高强度、工艺适应性强的铝合金,到设计部件和建造所需的生产设施,都是如此--例如,在这种情况下,福特嘉年华就是首次在科隆开发和生产的。
北威州(如阿滕多恩地区)的供应商也能从这种新型高强度铝合金大规模生产轻量化技术的发展中获益,设计并提供使用这种合金的其他产品。
成果
作为 Lightness.NRW 项目的一部分,开发了一种热压成型(HDF)工艺,可将高强度和最大强度铝合金(板材或管状半成品)成型为具有高度复杂几何形状的超轻结构部件。通过实验室和示范组件以及组件研究,展示了HDF技术在大规模车辆生产中用于轻量化结构的潜力。为了利用与超轻量结构相关的全部技术潜力,还开发了基于实验结果的过程模拟和静态及动态应用的组件模拟。
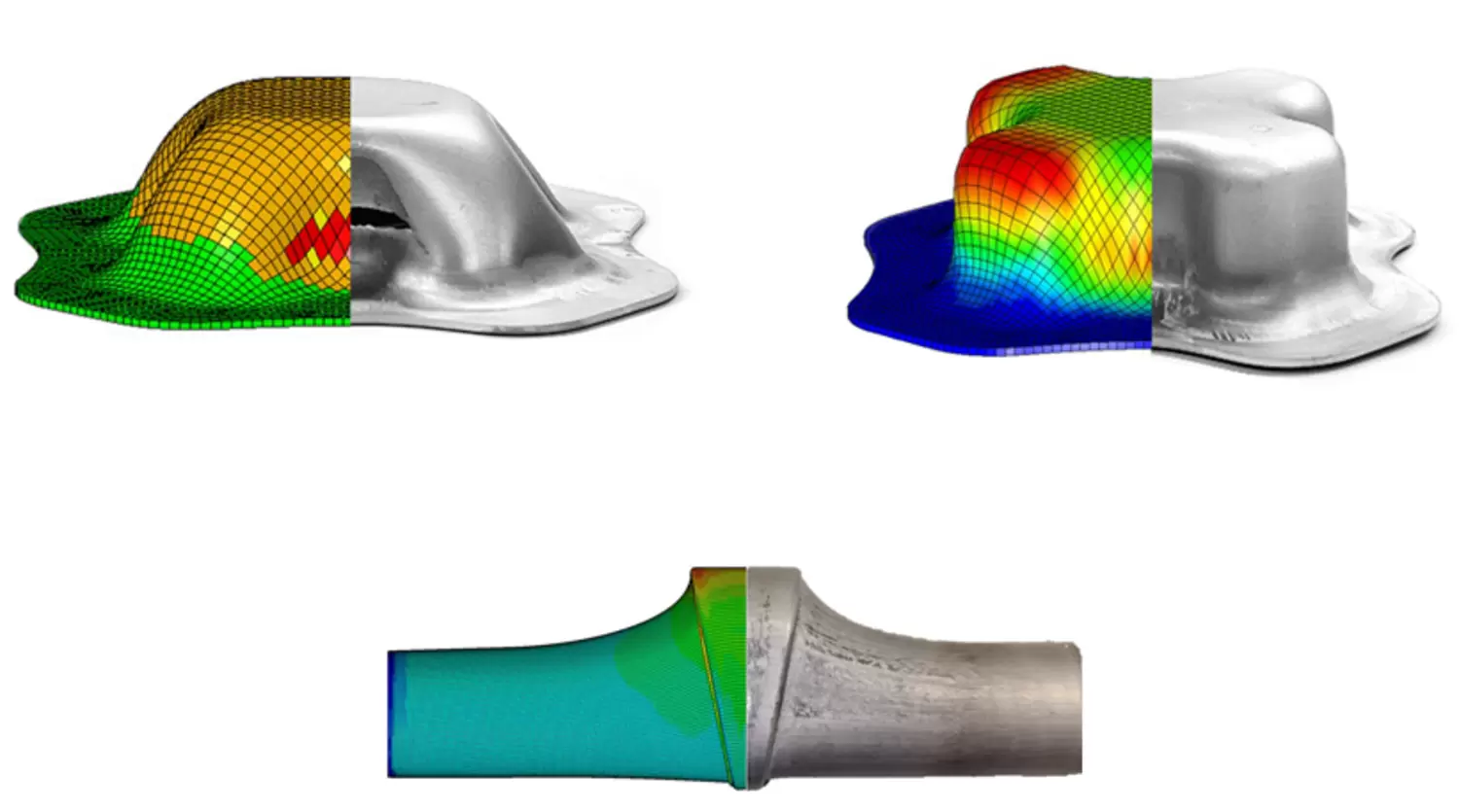
-
项目联合体一起解答复杂问题
-
项目联合体一起解答复杂问题
只有为覆盖价值链各个方面而设立的综合项目联合体,才能回答在整个工艺链中出现的复杂问题。联合体伙伴的能力和专业知识涵盖了从合金、工艺和设备的开发,到建立描述成型过程和组件行为的模拟方法学,再到实际示范元件的开发和生产及其最终的实验表征。基于开发和选择适用于HDF技术的高强度铝合金,通过成功制造两个技术示范元件——连接件和管节点,展示并实验验证了这种创新成型技术在生产复杂铝结构部件方面的性能。
这一过程得到了基于有限元的工艺和组件模拟的支持,以实现工具和组件几何形状的逐步优化。基于计算的机械特性(静态和动态),开发了一种材料卡片,使得铝轻量化结构有针对性的设计和尺寸确定成为可能。
基于此,开发并验证了一种强大的CAE模拟方法学,以及一种材料卡片和材料数据库,这些也可以在项目之外使用。利用实验测试的结果以及从示范元件制造过程中获得的关于最大变形程度的研究,还可以制定设计指南,从而探讨在汽车领域的潜在应用。
-
HDF技术的潜力
-
HDF技术的潜力
对技术示范组件进行了大量的静态和动态测试,这些测试为评估HDF技术的潜力提供了可靠的数据基础。通过模拟和实验,还研究了后处理对组件性能的影响,以确保优化热处理以达到所需的机械组件性能。
为将HDF技术集成到大规模生产环境中而设计的工厂概念,标志着项目从实验室规模到批量生产的重要一步的成功完成。为此,利用制造的管节点为例,虚拟实现了包括所有设备、准备和供应单元以及相关处理系统在内的工艺设施,考虑了车辆大规模批量生产中的周期时间。基于这一整体设施的虚拟展示,可以评估制造成本和环境平衡,并在汽车行业终端用户的协助下确定其在大规模批量生产中的一般适用性。
通过这种方式,为在大规模生产应用中建立HDF技术奠定了基础。最终评估的组件特性表明,HDF技术代表了一种节能和资源高效的轻量化结构的巨大机会。在未来几年中,这项技术可以为确保高强度铝合金制成的复杂(结构)组件在批量生产中广泛应用做出重大贡献,从而实现超轻量金属结构,这些复杂部件在传统工艺中通常不能经济有效地制造,甚至根本无法制造。
联系方式
-
Koos van Putten
-
Koos van Putten
Research & Development
+49 2161 350 2434SMS group GmbH
Am SMS Campus 1
41069 Mönchengladbach
Germany