In the conventional tapping of steel, the operator must always observe the converter position, the tapping stream and the position of the ladle under the converter. Slag flowing into the ladle is detected by slag early detection systems, and slag retention systems are activated automatically or by the operator. The tapping times depend on the tilting mode controlled by the operator. Faults occurring during operation negatively affect safety, production, quality and plant stability.
The use of X-Pact® Auto Tapping significantly improves the tapping process. The tilting angle is optimized based on the ferrostatic pressure at the taphole. The minimization of the resulting tapping time is controlled by means of a camera arranged at the converter mouth providing a view of the bath surface.
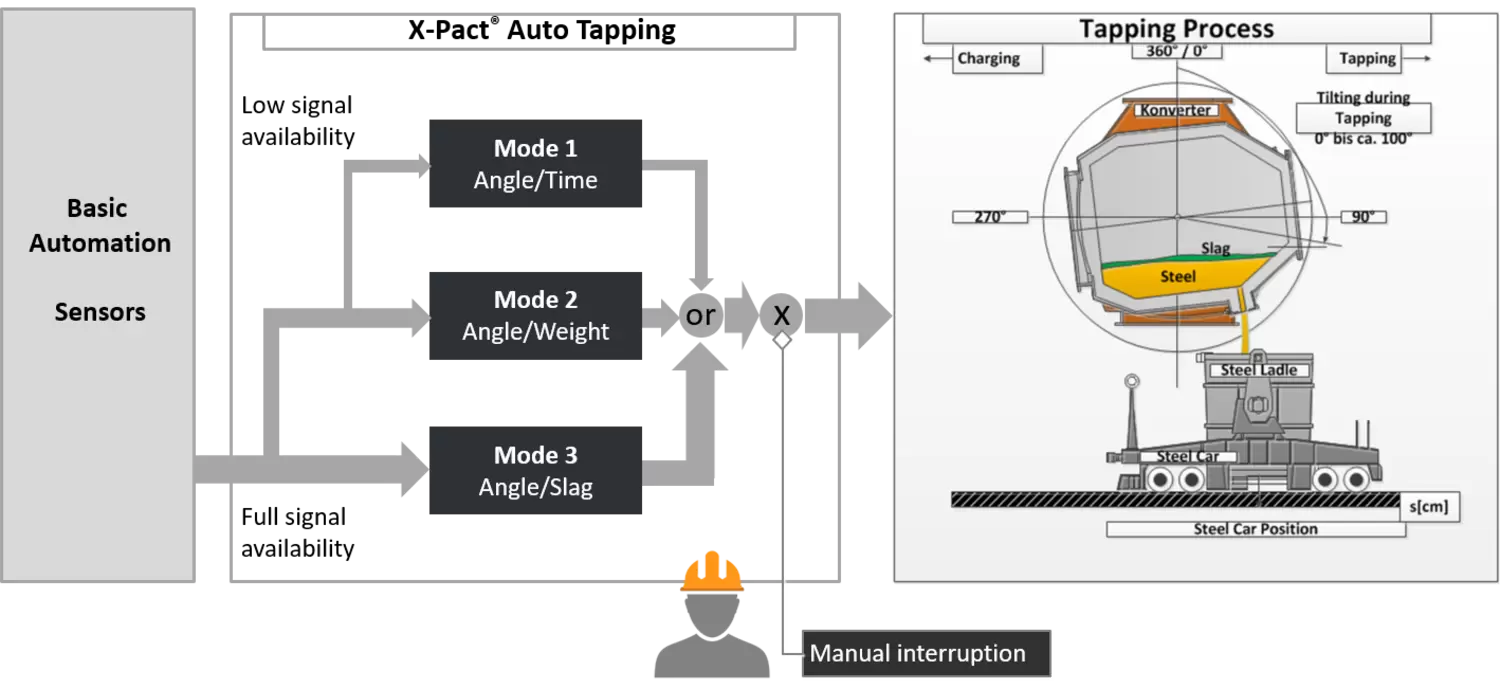
The automatic function has a robust performance. The high reproducibility of the tapping process leads to a shorter and operator-independent tapping time and to a reduced slag overflow into the steel ladle. The result is an increase in productivity.
Many of our customers' plants are equipped with the X-Pact® Auto Tapping module. This integrated solution from the X-Pact® portfolio for converter meltshops can be used either as an integral part of a complete automation solution or as an independent add-on that is integrated into existing equipment.