How do you eliminate the need for operators to always be present in a production plant? Are they really required on-site to prevent unplanned line stoppages? Or is it possible to operate a single plant, or even an entire plant complex, fully remotely? What about a scenario in which a plant was to be staffed by a minimal on-site crew in collaboration with an expert team located, let’s say, on the other side of the world? What would it take to implement a genuinely holistic approach comprising everything from the sensor level to the latest developments in digitalization? To which degree should a plant be automated? What kind of AI-based assistance functionalities will shape the path to autonomous operation? That is what X-Pact® Lights-Out is all about: It is our concept for highly dynamic, resource-saving, autonomous plant operation.
X-Pact® Lights-Out concept
With X-Pact® Lights-Out, our vision of autonomous plant operation has become a reality. To improve the efficiency of everyday production, the main objective is to achieve the highest level of process stability possible by reducing the necessary staff to a minimum. The X-Pact® Lights-Out concept represents a paradigm shift in production plant operation. Currently, the need for operators to be physically present on-site to monitor the performance of their equipment is mostly considered essential. In the future, however, the X-Pact® Lights-Out concept could make it possible to operate individual machines or all units of a plant complex from centralized on-site or even off-site operator stations.
For large companies with various locations in different parts of the world, this could provide several benefits. Their operational expertise could be concentrated, operator training could be centralized, and the exchange of information among members of the core operations team could be intensified. It would also be possible to establish centralized training centers using digital twins and global operating centers that are always available regardless of the time zone.
We help our customers realize their vision of a Lights-Out factory, allowing them to focus even more on their core business and strategic tasks. They will benefit in multiple ways, for example, from:
- High-performance autonomous production
- Remote operation of entire production complexes
- A highly qualified team of experts
- Maximum transparency of plant operations
The Lights-Out factory is also the future of industrial production regarding sustainability. Using the latest predictive analytics not only increases plant performance and efficiency but also helps to further reduce CO2 emissions by avoiding waste, improving the plant’s availability, and lowering overall energy consumption.
The ubiquitous shortage of skilled workers has the potential to even further accelerate the Lights-Out approach.
ONE pulpit: Fully networked plant with remote pulpits
A single control pulpit per line and a single, integrated, and centralized operator station for the entire plant complex. For CSP® plants, for example, several control desks could be combined to form a single operator station, enabling a single person to monitor and control several different subprocesses simultaneously.
Deep automation and maximum use of predictive maintenance make it possible to reduce the number of staff required on site. To this end, the various units of a plant complex are completely networked and connected to remote control pulpits. Real-time views of the plant, along with augmented reality (AR) and 3D visualizations, are displayed on large screens, along with key performance indicators (KPIs) related to plant status, product quality, energy management, and production planning. This enables centralized data management for all stages of production.
ONE team: Specialized remote control crew
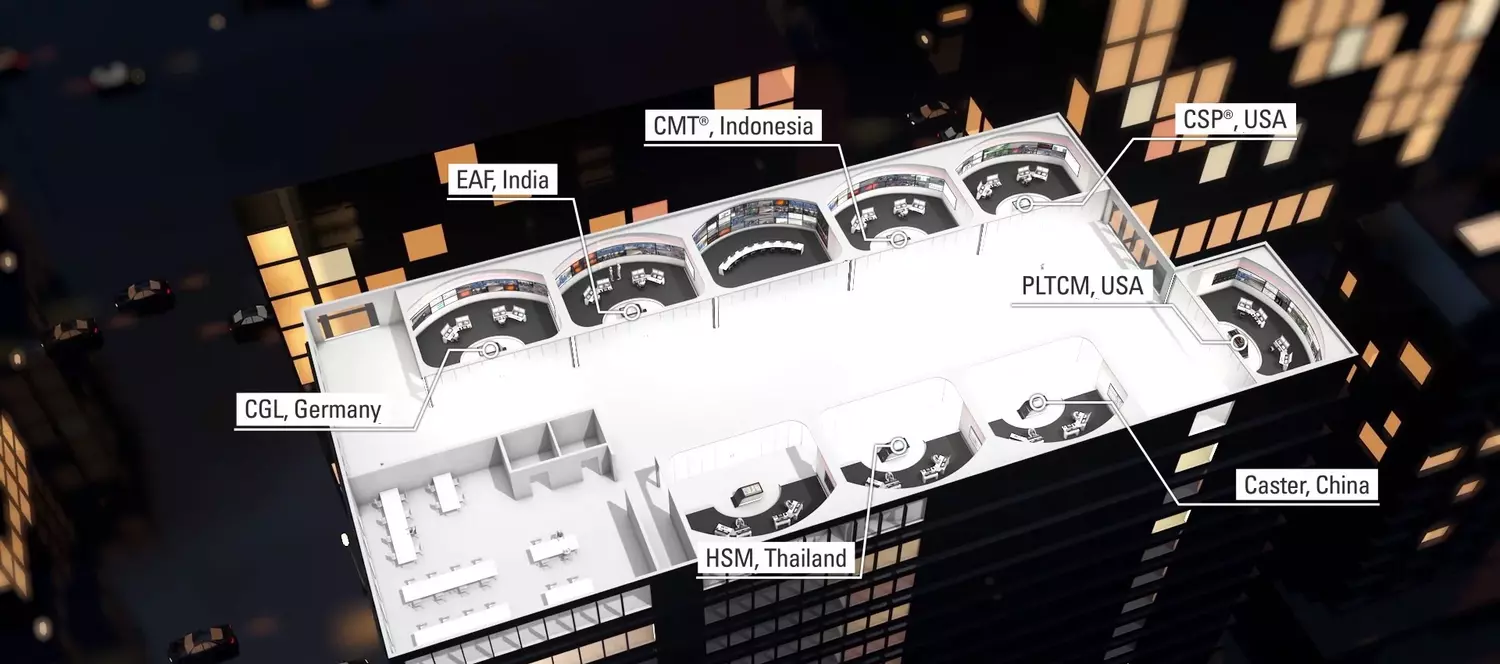
In a Lights-Out factory, all automation systems remain physically installed at the production facilities but are controlled centrally by a remote, highly specialized team of experts. This physical distance requires highly dynamic plant automation systems with the highest demands in IT communication capabilities for plant visualization (HMI) and also live camera views from and to the site. The remote teams and their local counterparts cooperate through the control pulpits and smart communication methods to achieve efficient operation and effective plant maintenance.
ONE view: Maximum transparency and supervision
An entire steelmaking complex, from the melt shop to the finishing lines, can be integrated into one centralized operator station – not only when building a new plant complex but also as a retrofit to existing facilities.
The X-Pact® Vision Integrated Operating Center (IOC) plays a pivotal role in this process. It consolidates all the operational expertise related to production processes in a single location, enabling a concentrated flow of information that facilitates plant and logistics management. This significantly reduces the need for human resources. All the data needed for production analysis, performance evaluation, and shift meetings is readily available at any time.
Several of our customers are currently running tests for the remote operation of their production facilities. After improving the process monitoring and supervision efficiency at their plants, some of them are already testing true remote operation. Increased process stability through AI and machine learning is crucial to successfully navigating the path to a Lights-Out factory.
ONE partner: Integrated, single-source approach
SMS group is ideally positioned to support our customers on their way toward more sustainable and profitable operations. Our integrated solutions combine 150 years of experience in metallurgy and plant engineering with a deep understanding of digitalization. Our motto for this integrated approach: Our Drive – Your Performance.
Tune in to this interview and learn more about X-Pact® Lights-Out.