Deep roots in successful CSP® technology
The concept of Nexus is based on SMS group's proven Compact Strip Production (CSP®) technology. With the first plant in 1989 at Nucor Crawfordsville in the United States and 30 reference plants built worldwide to date, CSP® is the industry’s leading thin slab casting and rolling technology. Due to the compact layout and a linkage of casting and rolling, SMS group's CSP® technology ensures highest product quality at high cost efficiency with a broad product spectrum.
The layout of a typical CSP® plant includes one or more vertical casters, a tunnel furnace for temperature homogenization and a compact finishing mill with up to seven stands. After the laminar cooling line, the strips are coiled at the downcoilers. With this setup, a CSP® line is capable to produce 1.5 million tons hot rolled coil per year. The capacity can simply be doubled by installing a second casting strand.
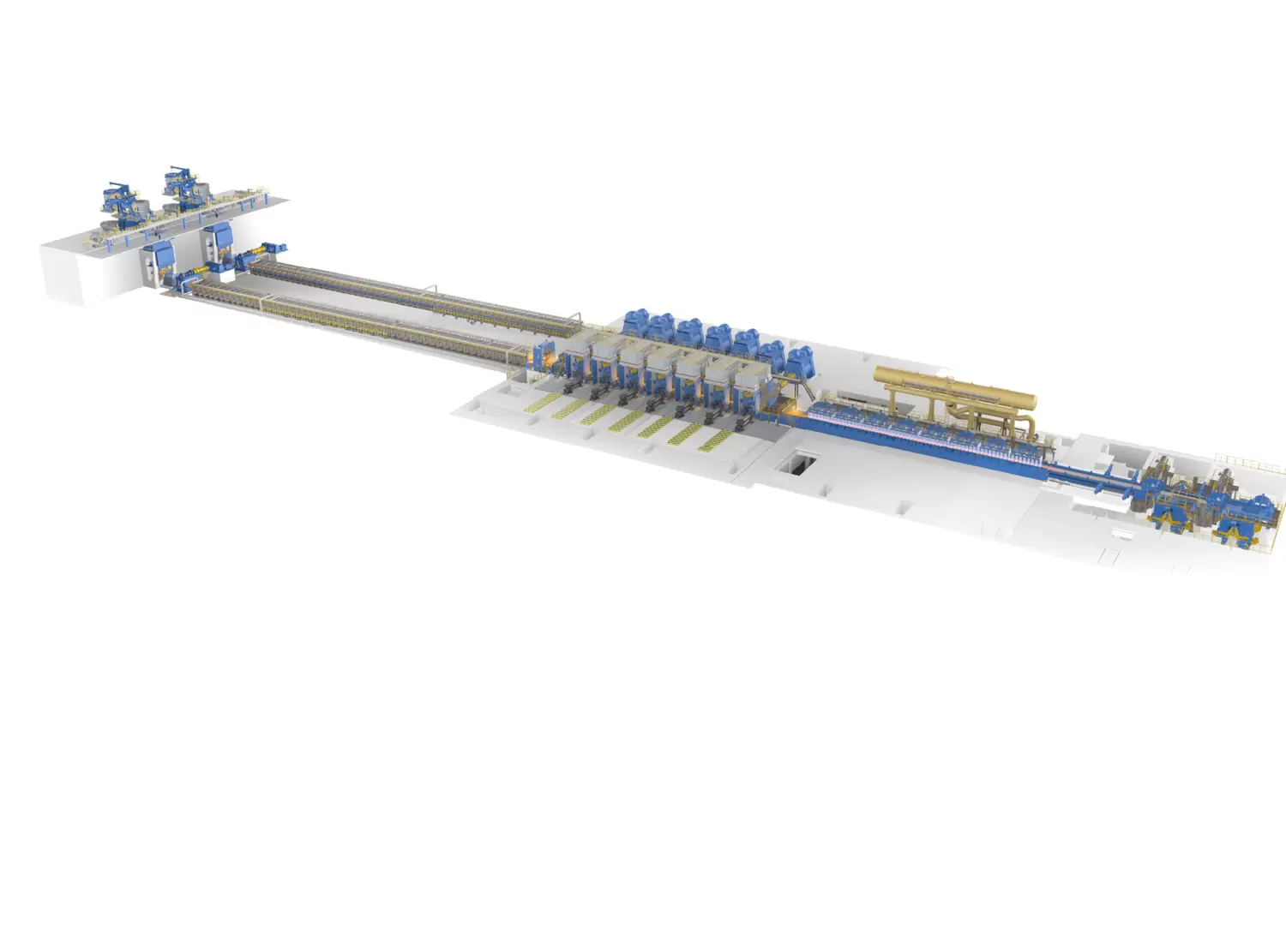
CSP® Nexus layout
For an increase in productivity and for an even wider product mix in terms of steel grades and strip dimensions, the well-known CSP® layout is complemented with a newly developed high throughput casting machine and an additional two-stand roughing mill. The result is the basic CSP® Nexus layout.
The bow-type casting machine boosts the yearly capacity of the Nexus plant to up to 2.7 million tons per year with one strand and more than 4 million tons with two strands – which is comparable with a conventional hot strip mill.
The roughing mill of the Nexus plant is capable to reduce the slab thickness to an optimum incoming thickness into the finishing mill. It allows the caster to always cast at optimum casting thickness in terms of productivity and temperature.
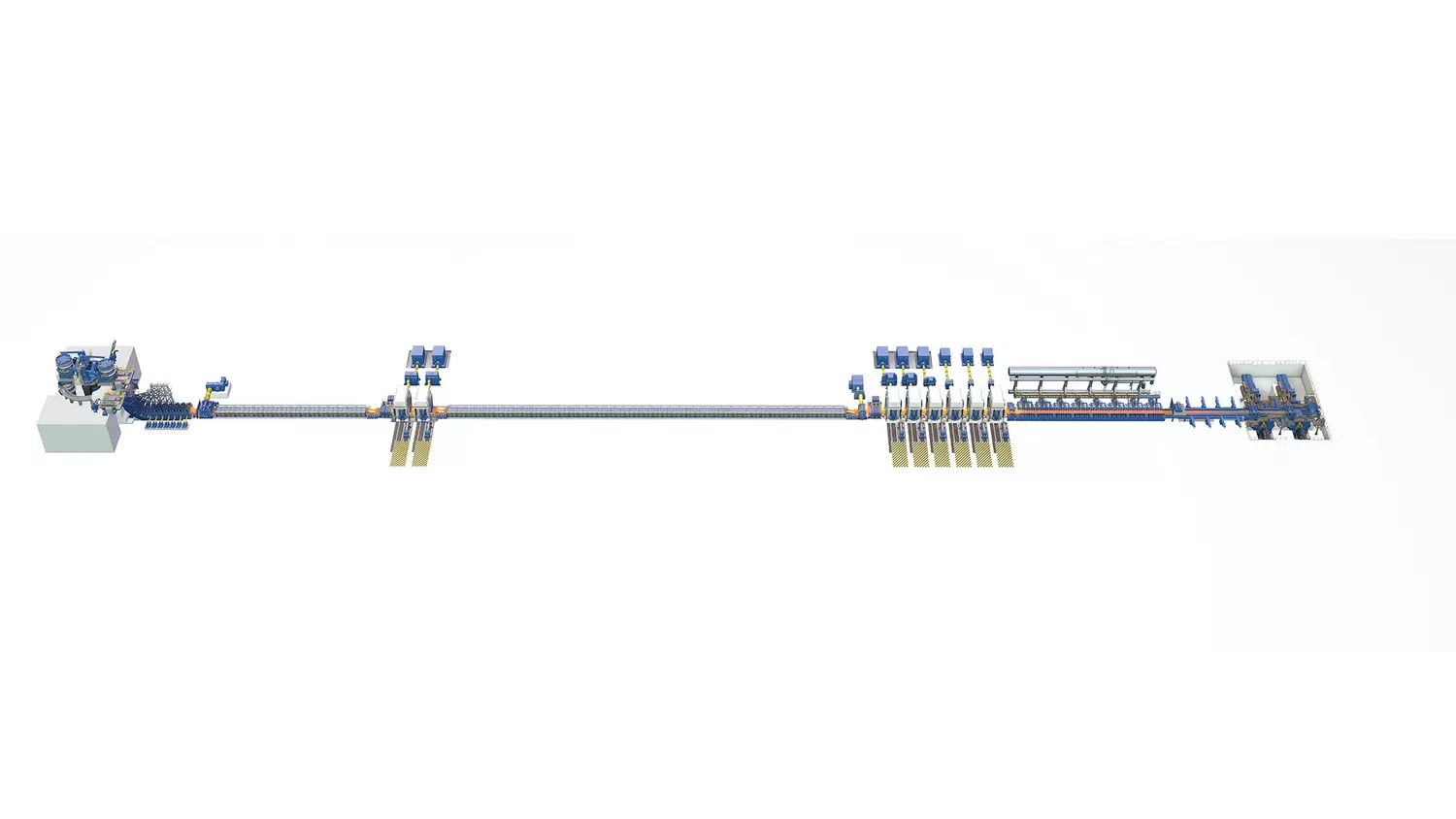
Highest flexibility due to a modular design
The layout of a CSP® Nexus plant is modular. It can be expanded with a variety of options to have maximum flexibility and fully meet the customers’ demands. For example, a second casting strand or lateral slab feeding to increase the production capacity, a high speed shear to enable endless production for ultra-thin strips, induction heating when the focus is on thin, high strength steel grades or an interchangeable casting machine head with a parallel mold allows the production of highly crack-sensitive steels.
Green steel production
Beside the demands of efficiency, flexibility and promptness for a profitable steel production, the global steel industry has to reduce emissions and meet sustainability requirements in future. With the compact layout and the combination of casting and direct rolling, the basic idea of CSP® and CSP® Nexus is the efficient use of energy and valuable resources.
To meet the green steel requirements, the CSP® Nexus plant can be designed hydrogen-ready or even fully electrified. As a result, CSP® and CSP® Nexus are capable to produce steel on a climate neutral level and will be an essential part of the green steel strategy.
First CSP® Nexus reference in 2021
The first CSP® Nexus reference plant is currently being built for SDI in Sinton, Texas in the United States. Starting 2021, SDI will produce 2.7 million tons per year.
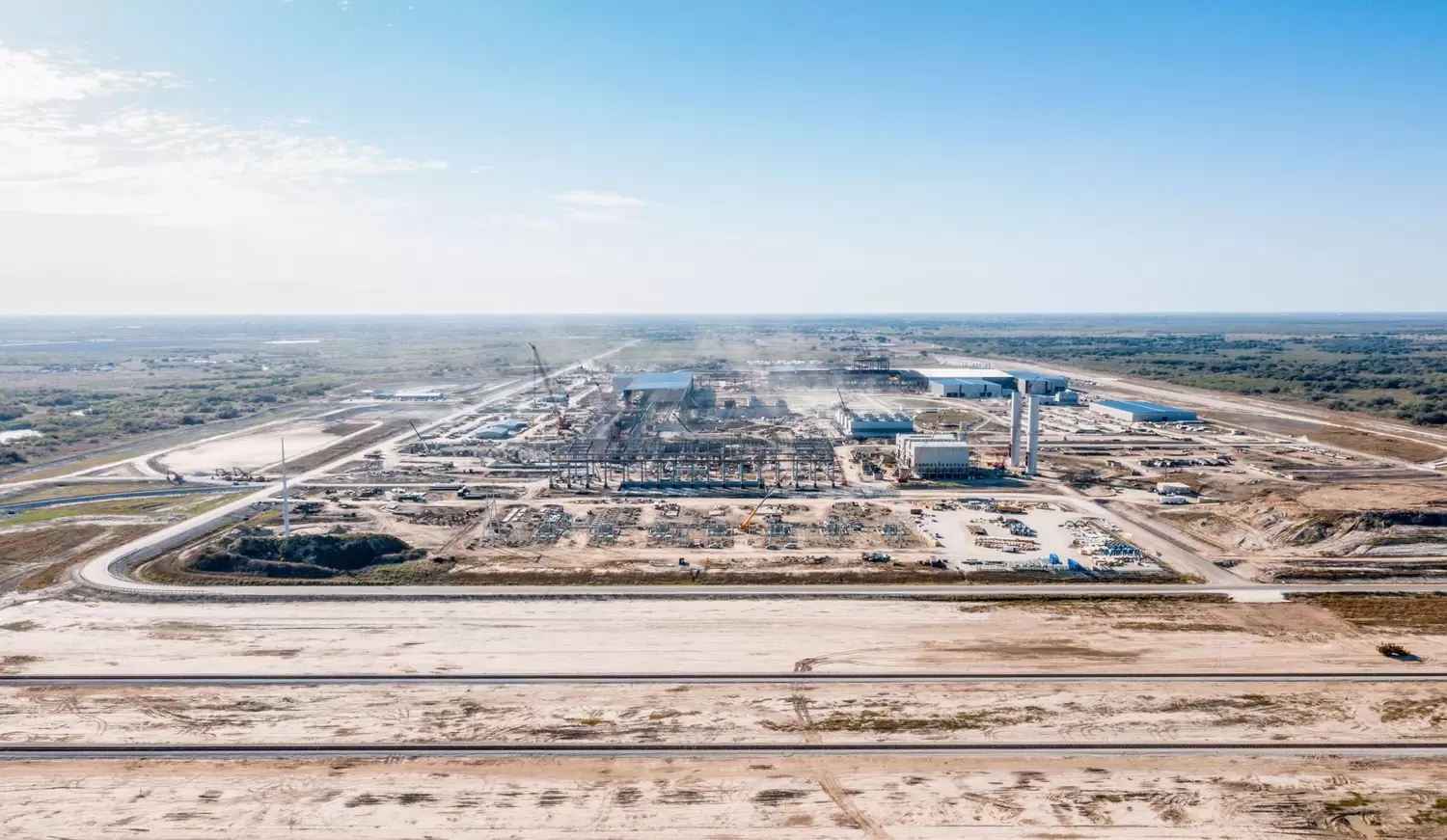