The smart steelworks optimizes its production processes from the raw material down to the final product in an auto-adaptive way employing physical and databased models as part of the integrated supply chain
Industrie 4.0, digitalization, internet of Things and cloud computing are topics dominating current discussions and strategies in industry. SMS group has developed strategies to promote digitalization in the steel industry on the basis of selected projects. This article also presents future-oriented concepts and solutions currently under development. Plant engineering companies and their customers have to deal with very similar challenges:
- Securing steel’s market position as a competitive material with versatile properties and the ability to fulfill future demands.
- Safeguarding competitiveness by lean processes and cost structures while using resources sparingly.
- Constant achievement of top product quality and high yield.
- Maximizing plant performance combined with minimized maintenance and low capital lock-up.
- Flexible production planning with varying and sometimes small batch sizes, at the same time guaranteeing timeliness of delivery.
All this has to be accomplished under ever-changing conditions, such as varying costs of raw materials, energy and human resources, and observing changing rules, such as new environmental regulations or modified legal standards. What does “Industrie 4.0 – digitalization” mean in this context? Digitalization is not an end in itself. The question is rather: “Where can digitalization help us achieve the above mentioned goals better – in a more sustainable and valueadding way?” Plant operators often first think of what is referred to as the “smart steel factory”, which would be able to produce steel intelligently and largely autonomously. The smart factory is characterized by the networking of activities performed by man and machine in dynamic production processes which will optimize themselves in real time taking into account the complete value chain.
What does Industrie 4.0 mean?
Industrie 4.0 means an ongoing process capturing the entire network of value creation. It comprises the vertical (internal) and the horizontal value creation chain (from the supplier through to the customer) and will eventually lead to a fundamental transformation of both. Everyone taking part in the value creation network will be feel the change.
The Industrie 4.0 process defines itself by...
- the current trend towards digitalization and the open, real-time exchange of data and the accessibility of data by all involved (humans and machines) in the manufacturing processes of the value creation network. This includes techniques like the Internet of Things (IoT) or the Internet of People (IoP)
- the creation of digital twins of real plants as well as of processes and products by converging actual and nominal data of the mechanical equipment, functions and processes via sensors, automation systems and software
- the employment of networked sensors and mobile computing capacities in embedded systems, which are cloud networked with existing IT systems. This allows relevant information to be processed in an individualized way and in real time and be made available to humans and machines at any place and time
- the expansion and upgrading of automation and production control systems by introducing data analytics (Big Data analysis, artificial intelligence) which enhance functionalities like self-optimization, self-configuration, selfdiagnosis, pattern recognition and intelligent support systems for the staff in the works
- the capacity of Cyber Physical Systems (CPS) able to make autonomous decisions and collaborate on a par with the staff. In this context, maximum attention will have to be paid to the safety and protection of the needs of employees, processes and machines
Digitalization is not new
When SMS group started to take an in-depth look into this topic, it soon became clear that “Industrie 4.0” was already present in the companies in certain areas, without calling it that way. This has also been confirmed by many of our customers and can be illustrated by the following examples: Already since 2000, SMS group has been engaged in the development of “virtual techniques” (virtual reality and augmented reality) as well as related basis technologies such as interactive real-time visualization and multi-modal interaction.
The digital workshop
In this context, SMS group has recognized that the topic of “multi-disciplinary collaboration” is an extremely important working field. We have further developed it into what is called the “digital workshop”. The digital workshop serves as a working and communication platform for multidisciplinary collaboration when tackling tasks that involve various various different disciplines. By making use of the native data and data exchange formats (IGES, JT, WRL) available in the 3D CAD systems used in the engineering departments, it links simulation data with actuations of plant components and movements of products. Today, virtual technologies are used as a tool to back planning and designing. Proven fields of application are, for example, interactive product presentations used in sales departments, integration tests as part of the project implementation process or virtual technologies used by service departments for training purposes. Making the customer part of a virtual, multi-discipline working environment shared by several users facilitates effective coordination and agreement processes that will minimize corrections at a later stage, saving project time and costs.
Plug & work - hardware-in-the-loop-simulation
The growth of computing capacities and advances in simulation techniques for multi-body systems (MBS) make it possible today to simulate the kinematic and dynamic behavior of complex machines and plants in real time and to operate them in a hardware-in-the-loop configuration with real controls. This allows functional tests of the control system and the programmed control functions to be performed prior to commissioning on site (virtual commissioning). Being a functional verification of the automation solution, this procedure takes place as part of the integration test of automation systems. All components are combined into one digital product. The simulation test incorporates the hardware assets of the automation system (operating stations, PLC, process computers, etc.) and the customer-specific operating concept. Interfaces are tested and pre-optimized automation parameters validated.
Complex control functions are visualized with the support of CAD models and may serve as tools in customer training. This approach guarantees short commissioning times with steep ramp-ups, resulting in stable production and high product quality from the very beginning. Today the use of digital engineering techniques is widespread in practice. Virtual commissioning is even applied to complex plant scenarios.
Hence, for the plant operators and for SMS group, digitalization is not an entirely new territory. However, there has been a shift of emphasis. Today SMS group understands Industrie 4.0 as a holistic process aiming at the creation of new value. We will become networked and cooperate with our customers and suppliers much more closely to achieve enhanced solutions in a concerted, joint effort.
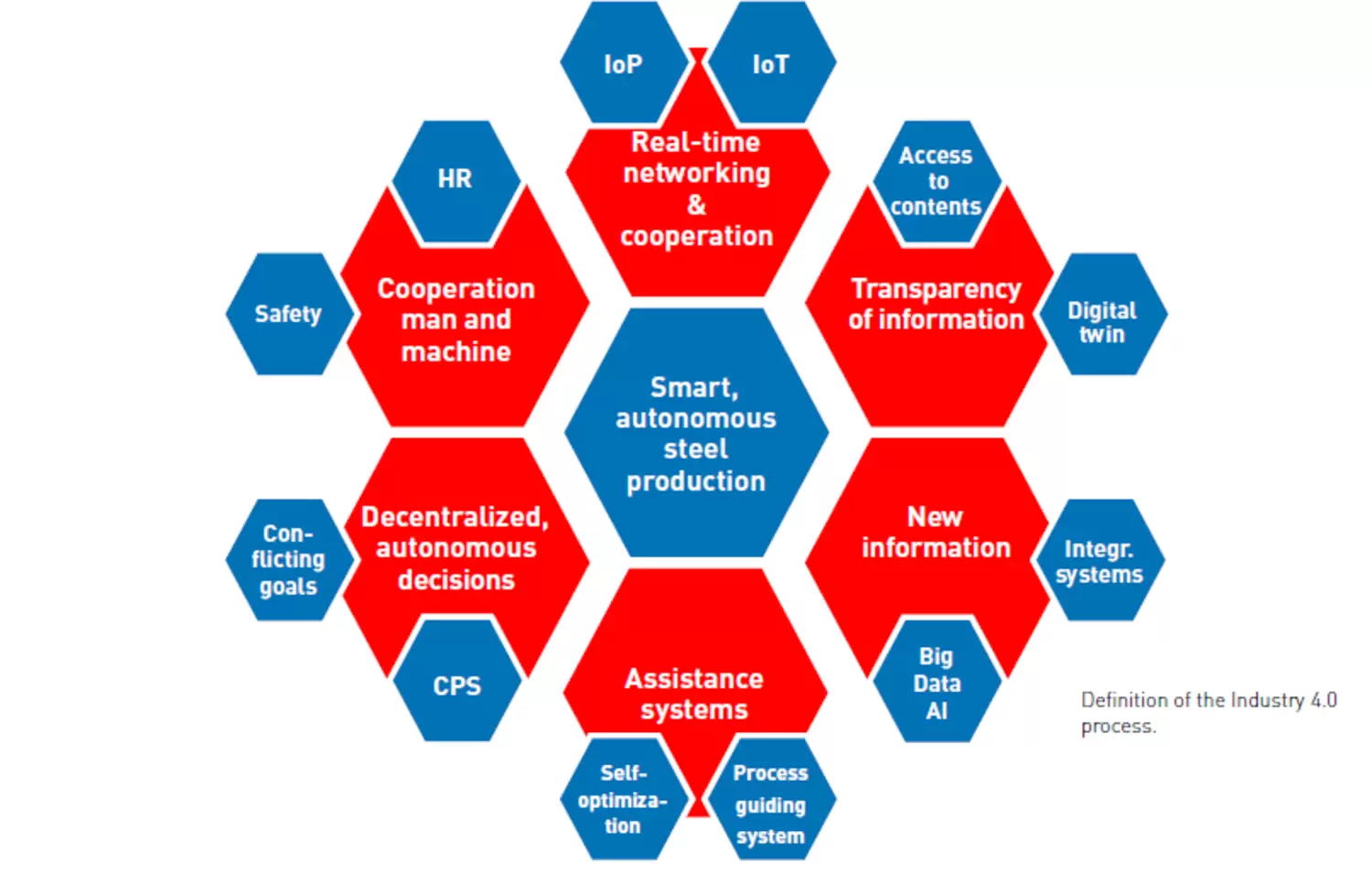
Pressing questions and expectations of the customers
SMS group has been taking an open approach to digitalization. Initially, within an Ideation Lab environment, numerous interviews were conducted with in-house experts and with customers and suppliers. The topic of digitalization gives rise to questions and multiple concerns. The most important questions refer to aspects like:
- How will digitalization affect business models?
- How is digitalization going to improve process efficiency?
- How can I make sure that know-how and process information will not be disclosed when we open up to the Internet of Things and how can we protect our operations against vulnerable attacks?
- How can I live digital processes and digital transparency without the feeling that I am surveiling everything and everybody? What legal implications go along with digitalization?
- How can I avoid loosing my independence? What would it be like for plant suppliers and their customers when they enter into a lifecycle partnership?
- How will all this fit into my current automation and IT structure? What standards will be applied?
- What kind of new requirements will the employees bepresented with? Where do I get competent answers to all these questions?
Examples
Digitalization also gives rise to expectations. This is illustrated below by examples representing various functional areas of a company. The basic instrument of Supply Chain Management, for example, is the consistent mapping of the production and material flows and the complete order handling process, including the customer order, the manufacturing order and the suppliers. The employees rely on digital simulation and optimization tools operating in real time to be able to plan production more effectively and at shorter notice and predict production processes or energy consumption more reliably. They expect flexible, cooperative logistics solutions implemented together with their raw material, consumables and spare parts suppliers. By handling the spare parts management for their customers as a service, SMS group has already been active in this field. Here, cost reduction potential is tapped from economies of scale resulting from the combination of several spare part portfolios.
Sales departments request digital tools that facilitate pricing and provide for transparency in delivery date setting as well as solutions enabling “digital shadowing” of products and processes, serving as documentation for the customer. Providers of IT and automation solutions as well as the IT departments of the manufacturing companies are presented with the challenge of having to capture all data and information arising from the production activities (plants, processes, products) in a consistent form, at all process stages and – if applicable – at all locations and to process and store the data and information in real time in what is referred to as a “Unique Source of Truth”.
At the same time, the correct information has to be processed in a way suitable for all involved (humans and machines), while being accessible at any place and time and guaranteeing a maximum of data security. This is an extremely challenging task given the existing heterogeneous structure of plant and automation solutions, the immense number of “production islands” that have evolved in the companies during the last two to four decades and the still common practice of handling processes and procedures in paper form. This will require quite some basic work to be accomplished in many areas. In production, great emphasis will be placed on the use of artificial intelligence in Big Data Analytics, as this will further improve the efficiency of process monitoring and controlling via self-learning algorithms. Purely physical modeling approaches in place today may soon be expanded or even replaced by data-driven models.
Predictive maintenance and service
Also the trend towards solutions enabling predictive maintenance and service of production-critical core components will pick up speed. Both plant operators and plant manufacturers will concentrate on retrofitting their plants with the necessary sensor equipment. Also the possibility of remotely tracking and tracing products and equipment components – and employees for safety reasons – will gain in importance. In quality management, functionalities like the assignment of functional and geometrical product information to the products, reliable tracking within the entire works in real time and the possibility of seamlessly relating quality-relevant information to each product along the entire production chain have been increasingly moving into the focus of attention. They facilitate the move to largely automated quality assessment processes and automated product grading against customer specifications, including a direct feedback to the production planning department. Quality-critical decisions have to be taken at an early stage in the process in order to ensure that the processing depth in the event of potential deviations is as low as possible or to be able to take remedial action against process deviations at an early stage.
What is the SMS group approach?
SMS group has been taking the approach of Design Thinking, a typical methodology used by digital start-ups. In the initial phase, the focus is on identifying customer requirements, the so-called Pain Points, in interviews or by mere observation. This is followed by an agile phase of Rapid Prototyping: initial solution concepts are implemented in the form of prototypes by specialists and validated and optimized together with the customer. In this way, a so-called Minimum Viable Product (MVP), a solution basically ready to be launched, is created in a matter of weeks. Then, the product will be further developed and sophisticated applying the proven procedure of testing, validating and improving. The guiding principle of all these activities is “sustainability”. The objective is not to digitalize anything and everything, but follow up on what will provide added value.
For SMS group as a plant engineering company one thing will change though: in the future, cost-based business models will have to be complemented or replaced by business models based on value. In other words, the plantbased business will remain, but will be much more closely linked with innovative, digital services. This requires above all trustful and reliable handling of the information and data which we share with our customers and vice versa. Therefore, the implementation of digital systems solutions will lead to a much closer relationship between plant manufacturers and plant operators, and the business processes on both sides will have to become a lot more transparent.
Another major task, which SMS group sees in connection with digitalization, is to make the management of Big Data more efficient, following the examples of the giant digital Internet players. The challenge is to systematically and continuously evaluate all data arising from production plants and production control systems and use the thus obtained knowledge as a basis for augmented decision-making, achieving, for example, functional improvements. Functional optimizations leverage reserves, quickly leading to a measurable benefit for the customer. Also decisions with respect to attractive investments and activities geared towards the development of, for example, assistance systems or expansions of existing automation systems can be derived from a high-quality database. The data and data techniques form the basis on which new business models for digital services, also outside one’s own sector of industry, are developed.
Examples of implemented digital solutions
As a plant engineering company, SMS group expects that advancing digitalization will first take shape in production, maintenance and quality processes. SMS group has already developed various marketable solutions that are in practical use in various production plants
Embedded systems
In the future, embedded systems will become a standard feature of our plants and components. Embedded systems document and analyze the behavior of components during operation and will autonomously initiate appropriate action, if necessary. An example is the system installed in a smart spindle in a hot rolling mill operated by a customer in China. The electronic component, including a CPU, has about the size of a business card. It is fix mounted within the spindle. An energy harvesting system, exploiting the rotation of the spindle as energy source, guarantees energy supply for at least two years.
The system monitors the spindle’s vibrations and torques. In addition to generating and evaluating the data autonomously, the embedded system also initiates necessary measures, such as service or maintenance activities. Establishing a link to the existing IT and automation structure is possible, but not necessary. Therefore the solution can be easily retrofit to existing plants. Systems data can be accessed by external computer systems at any time to perform further analyses. An additional feature of the system is that both current measuring values and information from data evaluations can be displayed on mobile devices.
Intelligent ladle management in the steelworks
The primary objective of model-based ladle management is to calculate the temperature contents of all ladles in the steelworks in order to determine the optimal temperature window for the casting operation, while taking into consideration the planned process operations and the current state of the ladles. Besides modeling the temperature fields of the ladle bodies, the refractory lining and the steel melt, the system is also expected to provide constant tracking of all the ladles in the steelworks by means of RFID, beacon or IR image recognition techniques. Measured data from temperature sensors, thermal image cameras and information about lining types and residual wall thicknesses available in the ladle lining and repair shops are implemented in the system in order to back the modeling processes. Commissioning of such a ladle management system is currently under way at one of our customers in Germany.
Virtually supported plant control - augmented operation
An example of Augmented Operation is the solution developed by the SMS group company Amova. The objective of this solution is to optimize logistics control in a high-bay coil store. A digital twin of the high-bay store is used to control, monitor and optimize the process. The twin generates a 3D map of the complete high-bay warehouse including the transport systems and finishing facilities as well as the associated dynamic activities. Product and processrelevant information from the automation systems is inteintegrated into the visualization in real time and retrievable as required. The warehouse operator can observe all warehouse activities both in reality and in the virtual set-up. The digital twin additionally allows the operator to view information such as the current temperature level of each coil. Release signals and transport operations are initiated in the digital twin via drag & drop functions and directly relayed to the autonomous cranes and forklift trucks, however, in a system-optimized sequence. Via its forecasting functionality, the system can also project all processes and operations into the future, ensuring maximal transparency in logistics planning.
SMS group platform services
Digital service platforms are the foundations of intelligent, digital service competence. Via such platforms, companies can exchange information in digital form reliably and securely. One of the first e-functions offered by SMS group is an eService solution which allows its users to quickly and reliably identify spare parts and have access to documents such as data sheets, service guidelines and operating manuals. The electronic spare parts catalogue presented in 2016 at the Tube & Wire trade show has already been rolled out at one of our mini-mill customers in the USA. Via an intuitive operating application designed to be used directly at the plant, the correct spare part or spare parts package can be identified and the procurement process initiated with just a few clicks , either via the ordering procedure in place at the customer’s or directly on the SMS group platform.
Bottom line
Various selected examples of digital solutions have been presented above. SMS group has been dealing with digitalization not only under technological aspects, as it has consequences on the integral processes of a company, with fundamental effects on existing processes and business models. To SMS group it is more an evolution than a revolution. Change is expected to take place in the areas of production, maintenance and quality assurance first. The key factors enabling this change are embedded systems, digital service platforms, the successful implementation of realtime data networks within the works and the ability to make best use of the performance capabilities of Big Data Analytics and Cloud Computing in order to promote the employment of self-optimizing, autonomous process control systems. According to SMS group, digitalization will provide entirely new opportunities for both steel producers and plant manufacturers. This will lead to more intensive cooperation between the plant suppliers and their customers, and to the implementation of digital solutions that are commercially rewarding for both sides.