Anyone in the winter out and about on the world’s ski slopes is familiar with the situation: if you are freezing you wear the wrong clothing. It is so to speak our protective coating. In a similar way, the thermal coating process affects the components. Using various thermal spraying methods, protective coatings are applied to the surfaces to protect them against external influences. In this way, components may become resistant for example against corrosion or wear, which not only may make them last longer, but additionally extend their field of application.
In thermal spraying, coating materials such as wires, powders or bars are fed to a spray gun or to a burner. The materials are heated and then accelerated into the direction of the component. In this way, the joined or fused particles achieve high speeds of up to 800 meters per second hitting the surface of the component. After the heat is transferred to the base material the particles solidify on the component’s surface where they form a layer. The spray coating, however, not only spreads on the surface but virtually joins to it. Depending on the desired coating thickness, this process is repeated.
The term thermal spraying comprises several different processes which in their application are not in direct competition. On the contrary, they complement one another due to their specific characteristics with regard to processes and coatings generated.
New fields of application with proper protective coatings
When protective coatings are applied high-duty components may be qualified for the utilization in mechanical and plant engineering, but also in aerospace or automotive technologies. In addition to that, lighter base materials may be used for applications for which they were not suited up to now due to their surface properties.
For coatings using thermal spraying nearly all base materials are suitable. In addition to metals, ceramics, plastics, fiber composites or even natural materials such as stone and wood can also be coated. The latter, for example, represents a popular building material, combining high compressive strength with simultaneous elasticity. And often high resistance can be extended with a sprayed coating and additionally protects wood against parasites such as insects and against fungi infestation. Thanks to a functionalized surface, the building material can be used for a broader field of application. Furthermore, esthetic aspects may also play a role: for trendy furniture for example copper-coated wood is used.
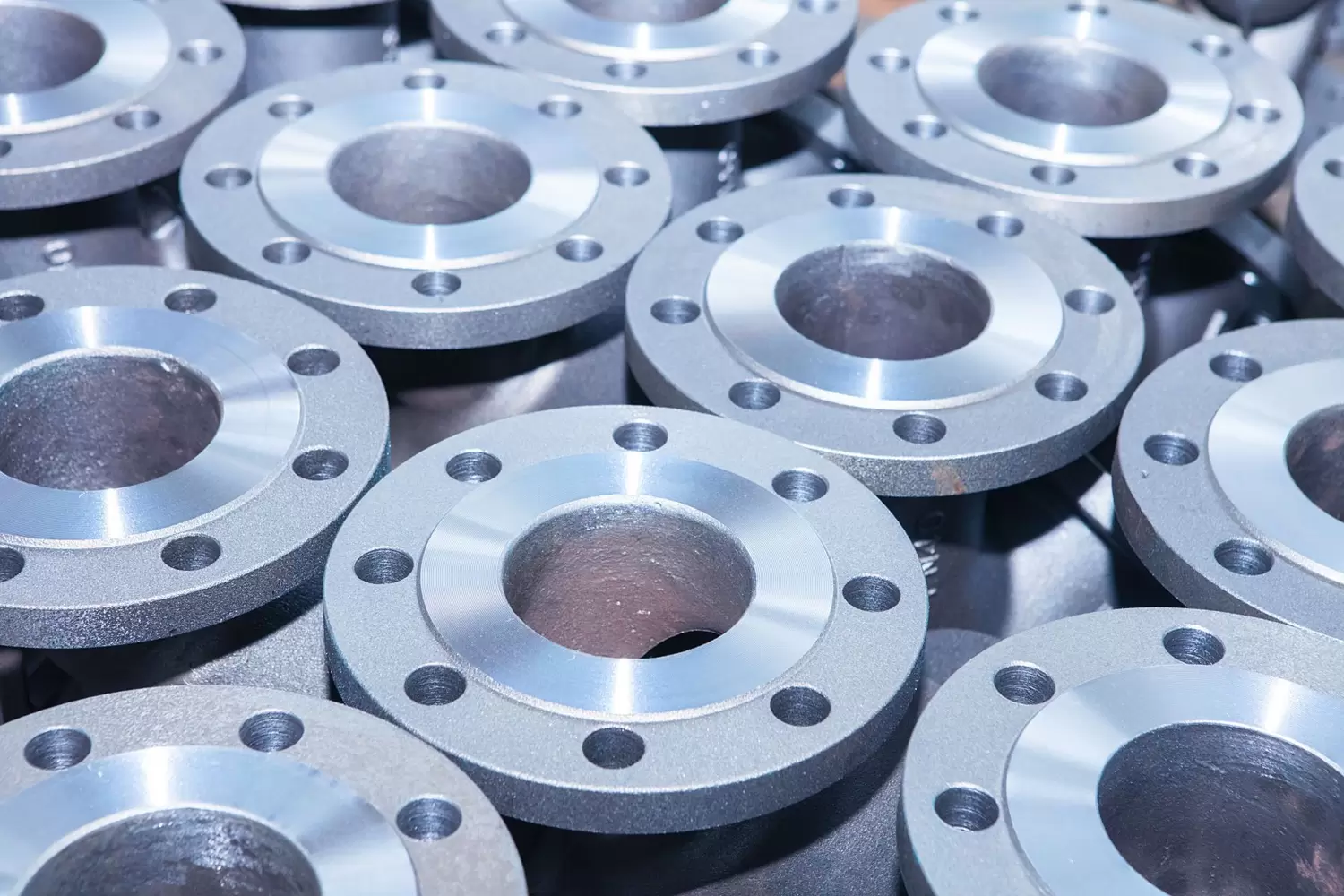
Medical technology also offers application examples for thermal spraying, for example for implants, which are better accepted by the natural body tissue due to the additional coating.
In practice, the thermal wire arc spraying process has proven to be extremely suitable for applications such as welded pipe seams. During thermal coating by means of an electric arc, two metallic wires are fed into a focus point as starting material, where the wire tips are fused by an arc. Droplets are formed which are accelerated by secondary atomization with a high-kinetic gas jet in the direction of the workpiece surface to be coated. The atomized particles on the workpiece form a finely structured, homogeneous coating featuring excellent mechanical properties such as improved hardness and/or abrasion resistance and oxidation and corrosion resistance even at high temperatures.
Thermal coatings score with corrosion protection in seawater
With thermal coating large steel structures in the offshore area can be protected permanently against seawater corrosion. A great advantage compared to varnishing exists in self-healing of thermal coating which means that minor surface damage heal independently due to the electrolytic effect between the base material and the zinc coating applied.
“The components employed in offshore wind turbines are usually made of low-alloyed structural steels. To be able to achieve long-lasting corrosion protection throughout the overall planned service life of 25 years, Duplex systems play a key role consisting of a combination of an arc-wire sprayed zinc-aluminium 15 (ZnAl15) coating and a suitable organic cover coat. For applying such coating, arc- wire spraying is the most commonly applied procedure, as it allows high melting rates and thus high area output,” said Dr. Frank Prenger, Grillo-Werke AG. For this application state-of-the-art arc-wire spraying systems offer top quality, tight coating tolerances and a sustainable corrosion protection.”
And in fact, corrosion protection is one the most frequent applications for thermal spraying. Within machinery and equipment corrosion protection provides for extended lifetime and thus ideally for a production advantage.
PERFECTly equipped: The wire arc spraying system of SMS group
Another application example is corrosion protection for pipelines to improve their durability and make them more resistant. At SMS group, we combine the process of wire arc spraying with a digital power/voltage source developed inhouse. The result is a product exceeding the possibilities of classical wire arc spraying. The coating gun is equipped with an innovative nozzle design which specifically generates atomizing air and thus provides for higher efficiency. Low wear and consistent electrical contact of the wires ensure a smooth spraying process. The gun offers maximum reliability together with a low-maintenance concept, whereby high-functional and long-lasting materials are employed.
The SMS group system is modularly structured providing several technical advantages – including the possibility to lead the flow at the wire ends well into the supersonic range or decelerate the gas to subsonic speeds. Ceramic inner flow contours adapted to the respective coating application have been designed according to gas-dynamic aspects and can be adapted to the desired gas volume and mass flow.
Processes for cost reduction in component production are under permanent development. With thermal coating, it is possible to “save” components which have been worn or damaged during the treatment process. Here, thermal coating offers a cost-effective solution. In addition to that, rejects can be reduced and productivity can be boosted.
Join our expert session
You want to learn more about wire arc spraying? Register for our webinar-on-demand.