The production of modern AHSS (Advanced High Strength Steel) grades places high demands on the thermal process in annealing and hot-dip galvanizing lines. In particular, the automotive industry requires homogeneous properties of the steel strips not only over the entire length of the coils, but also from coil to coil. In order to achieve this, information on the steel structure is necessary to control the process and compensate possible deviations caused in the upstream processes.
Therefore, SMS group developed the I-Furnace including a smart annealing process and a production optimization model. Here, the combination of various tools leads to an optimized heat treatment and production process. Furnace control, online strength measurement and a model to predict the material properties after annealing are combined and linked. However, a closed-loop control of the process is not possible with a measurement system in the exit section of the line, far behind the process, because at that point the material already has its final mechanical properties.
Thus, a further measurement system including control model has been developed in addition to the already existing tools to complete the furnace. SMS group, Drever International and IMS Messsysteme jointly developed X-CAP (X-ray Controlled Annealing Process) permitting the steel structure to be measured within the annealing process and hence the mechanical properties to be controlled in the very process step where they are really determined.
Secondary phase determines strength
Finished AHSS grades consist of a combination of two or more phases to achieve the required material properties. During the heat treatment, the fraction of austenite before rapid cooling determines the amount of the secondary hard phases formed in the subsequent cooling stages. For AHSS, the secondary phase fraction is the main influence on the strength of the final product. With X-CAP, a system is now available for the real-time quantification of the austenite content during the annealing process. The new online measuring system uses X-ray diffraction to define the crystalline phase fraction, and hence the austenite content, upstream of the rapid furnace cooling section. The continuous measurement of the austenite content in the furnace allows to directly compensate process and material changes, which otherwise would lead to product quality deviations.
Improvement in material quality
A first system was installed, inside a specially developed protective housing, in the furnace of a hot-dip galvanizing line at Tata Steel in Liège, Belgium, in the SEGAL plant in summer 2017. The measurement results were compared to the final product strength. Various tests proved that with using X-CAP it is possible to significantly improve material quality. X-CAP can save coils and keep the characteristic material properties within the required range, which even experienced operators are unable to do. Producers of annealed and galvanized coldrolled steel strips are facing several challenges when it comes to modern AHSS grades. With the I-Furnace and X-CAP, innovative solutions have been developed to improve and control the complex process of AHSS production. Further information on the recent development will be provided to visitors as part of a lecture at ESTAD or at the SMS group booth at METEC.
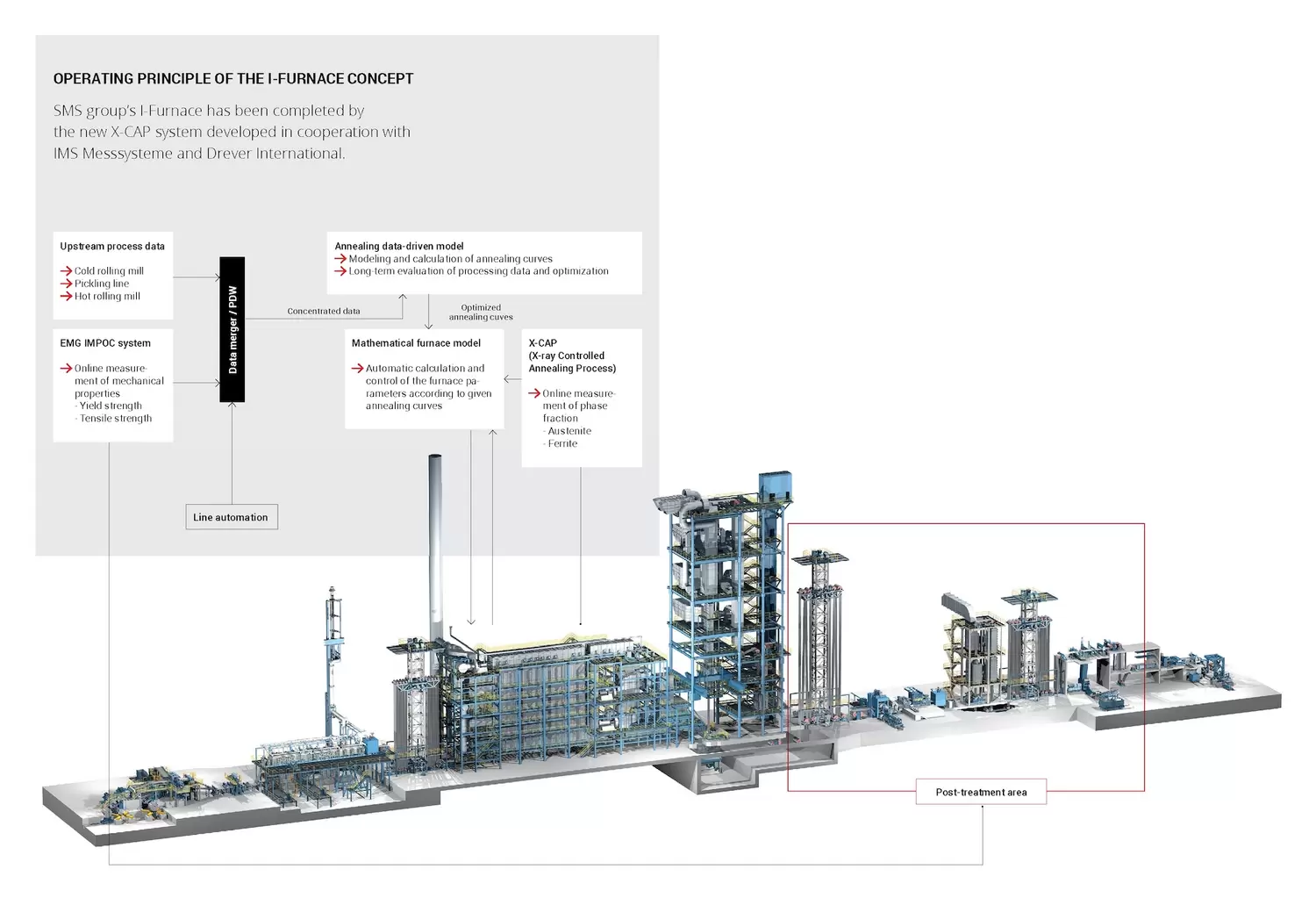