Digitalized documentation increases efficiency
By the end of the year 2017, digital applications in all process steps will have advanced the steelworks at Big River Steel to the first Learning Factory in the world.
This aim is backed, amongst others, by an electronic parts catalog mapping the plant documentation of the complete supply package of the project in a cloud solution. The database rests on a total of approx. 410,000 bills of material items, 30,000 drawings and 45,000 individual documents from the SMS group business units involved and from all further suppliers of single parts or assemblies which can now be called using a single tool after they have been consolidated and specially prepared in structure for this purpose. The new tool permits Big River Steel to identify and inquire parts quickly and easily. All data are continuously updated and, up to now, used by about 70 internal Big River Steel employees. Time-consuming searching for required information is a thing of the past. Further functions such as displaying identical parts throughout the entire plant, provide Big River Steel with the desired transparency and contribute to increasing efficiency and reducing the inventory.
Randy Martin, Warehouse Material Coordinator at Big River Steel, is enthusiastic about the electronic parts catalog: “The catalog is very helpful, and we use it in the warehouse several times a day. But also maintenance people ask for our help in finding parts with the new system and see obvious benefits from the program. We can search for parts by title, material information, SMS and Big River Steel material numbers, etc. The software is available around the clock seven days a week.”
In addition, the electronic parts catalog serves as the basis for further digital products. Being a virtual image of the plant, it permits digital services to be linked to purchasing actions. The required technical information is immediately available in all applications and can directly be transferred to the procurement process. If, for example, the condition monitoring system forecasts the failure of a component, it will be possible to simultaneously check information on identical parts, inventory and delivery times and to procure the wanted part.
The eService of SMS group makes Big River Steel fit for future challenges and satisfies all conditions to cope with the fourth industrial revolution – Industry 4.0.
To make sure that production at the Big River Steel plant continues to be successful, SMS group Technical Service offers a wide range of services.
SMS Technical Services (STS) has opened a new maintenance shop, only two miles away from the Big River Steel’s plant. STS performs all maintenance services on the continuous caster, on the molds, and the segments and rolling mill components for the CSP®-plant. In addition, SMS Technical Services is responsible for two local roll shops of the hot and cold rolling mills. Altogether about 75 service employees are working in the workshop and the roll shops.
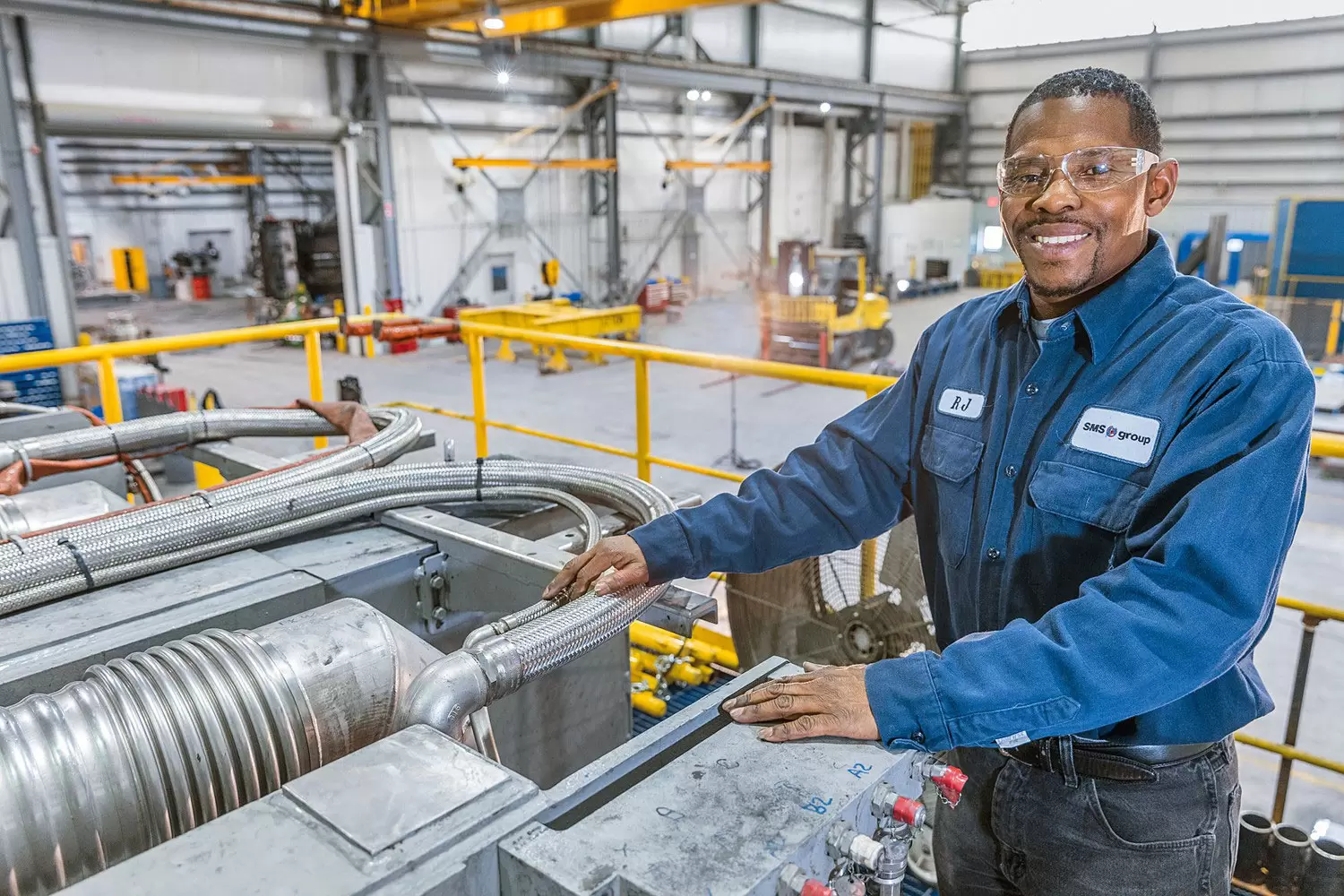
Repairs and coatings
In the STS workshop in Osceola, North American operators of continuous casters can use all services provided: starting with repair, overhaul, and maintenance through to servicing all plant components. Thanks to a large horizontal CNC machine with additional machining and turning capacities and blasting and painting booths, SMS Technical Services can also offer additional services. The full-service repair shop with its modern electroplating operations enables high-quality coating of copper plates. Also offered is local field service including the service activities e.g. laser scanning and alignment for plant equipment and machines.
Expert Training
Know-how boosts productivity – and that is just one of the mottoes according to which Big River Steel in Osceloa, Arkansas, USA operates the most modern steelworks in North America. The latest technologies and supremely trained staff make this possible, as they form the foundation for the competitiveness and safety of the production. When it comes to staff qualification, the steel group also relies on the SMS group and the comprehensive training offered by the SMS TECademy.
Big River Steel knows exactly what counts in practice. That is why the staff training courses were tailored individually to the wishes and needs of the steel group. A good balance had to be found between theory and practice. Theoretical know-how was therefore first presented graphically in extensive classroom training sessions. These were held in cooperation with the Arkansas Northeastern College (ANC) at its facilities in Osceola.
TRAINERS TRAINED IN GERMANY
In June last year, three lecturers from the ANC came to the SMS group in Germany to prepare themselves thoroughly for their future teaching duties in the field of modern steel processing under the SMS TECademy’s ‘Train-the-Trainer’ concept. They thereby furthered their know-how of the plants and processes involved in metallurgy and rolling mill technology, and were particularly impressed by the SMS TECademy’s “digital workshop” that allows a plant to be toured in real- time. Virtual reality simulates the entire process chain and depicts the production process dynamically. True to the motto: “A picture says more than 1000 words – and the digital workshop says more than 1000 pictures”. A similar methodology was subsequently integrated into the ANC curriculum.
After teaching the theory, the focus then turned to the practical application. Here the Big River Steel training participants were able to demonstrate their newly acquired know-how directly on the plant in the subsequent ‘hands-on’ training sessions. With an experienced trainer and technical experts at their side, they were able to put the theoretically acquired knowledge into practice and to immediately clarify any questions arising during the direct use. That gave the participants confidence. All the training courses were split into the two main topic areas, mechanical and electrical & automation. A further structuring of the material according to certain key topics provided the participants with a very detailed training plan.
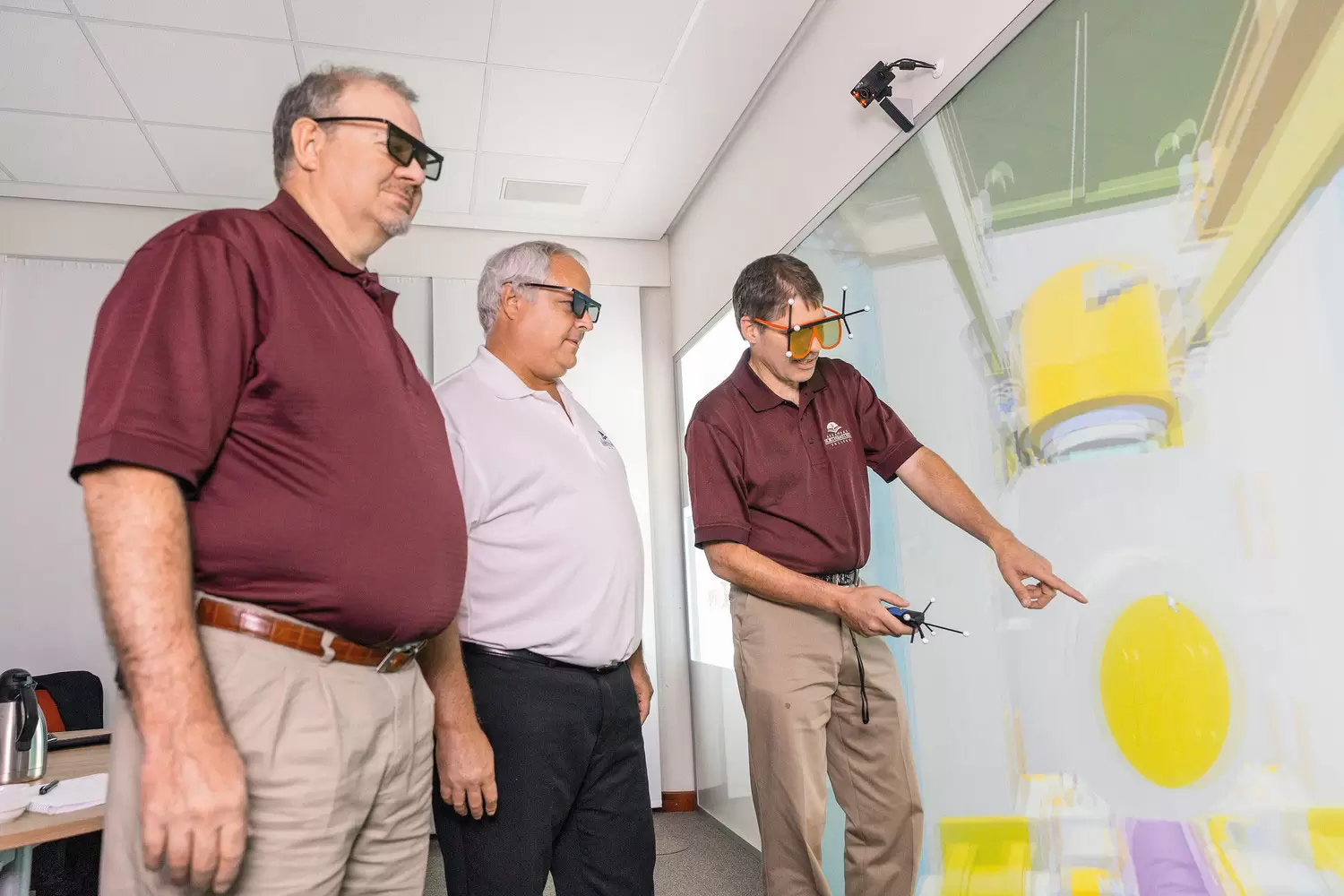
SMS TECademy evolves further
The most extensive order for the SMS TECademy to date required not only very detailed planning, but also great flexibility and commitment on the part of the TECademy team. “We are very proud that Big River Steel put their trust in us for the further training of their staff. The cooperation with Big River Steel has been a great asset to us, and has given us valuable input for the further development of the training we offer. Both sides have therefore benefited equally,” says Karsten Weiss, Head of the SMS TECademy. Big River Steel also draws positive conclusions. “We are very satisfied with the training. We can only achieve our ambitious goals for the future with the best trained staff. The SMS TECademy training courses were tailored so individually to our requirements and wishes that we had no doubt about the success of the measures. With the SMS group at our side, we get not only first-class plant engineering, but also outstanding service – and that is something we appreciate greatly,” says Lenore Trammell, Chief Compliance Officer of Big River Steel.
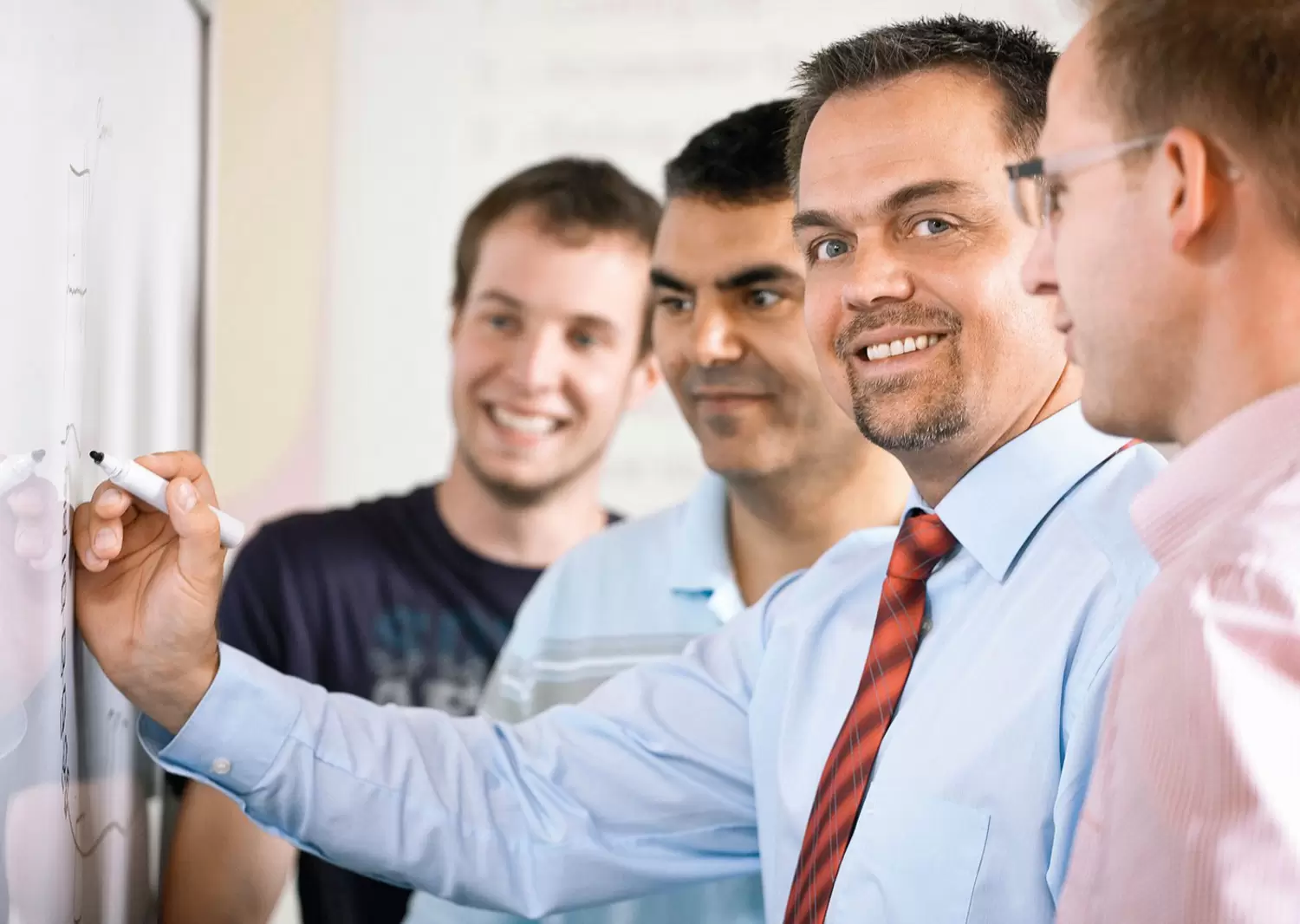