The function-optimized design and 3D-printed die spray heads have resulted in tremendous improvements in die maintenance during the production of aluminum forgings. What convinced the customer were the performance and effectiveness of these innovative spray heads. The ARWS1A forging roll as a preforming machine and the MP2500 closed-die forging press from SMS group forge chassis components for a well-known electric car manufacturer. The light, aluminum 3D-printed spray heads work without a hitch and boast a precise, first-class spray pattern. These excellent properties optimally support the fast cycle time of the process. The fast cycle time is achieved with an automatic walking beam system supplied by SMS group.
The decision to use the new type of spray heads here was mainly based on the low overall height of the 3D-printed variant, as this is where conventional sandwich-type plate spray heads would already have reached their limits. The new additively manufactured spray heads exhibit significant advantages over plate spraying heads. Due to the layering of the plates in conventional spray heads, the maximum operating pressure that can be applied is 3 bar. Otherwise, the plates could give in to the pressure and air and spray fluid could escape from the sides. By contrast with the round and flow-optimized channels of the 3D-printed variant, the square channels in the conventional plate spray heads tend to have a build-up of contaminates or graphite, which requires regular intensive cleaning.
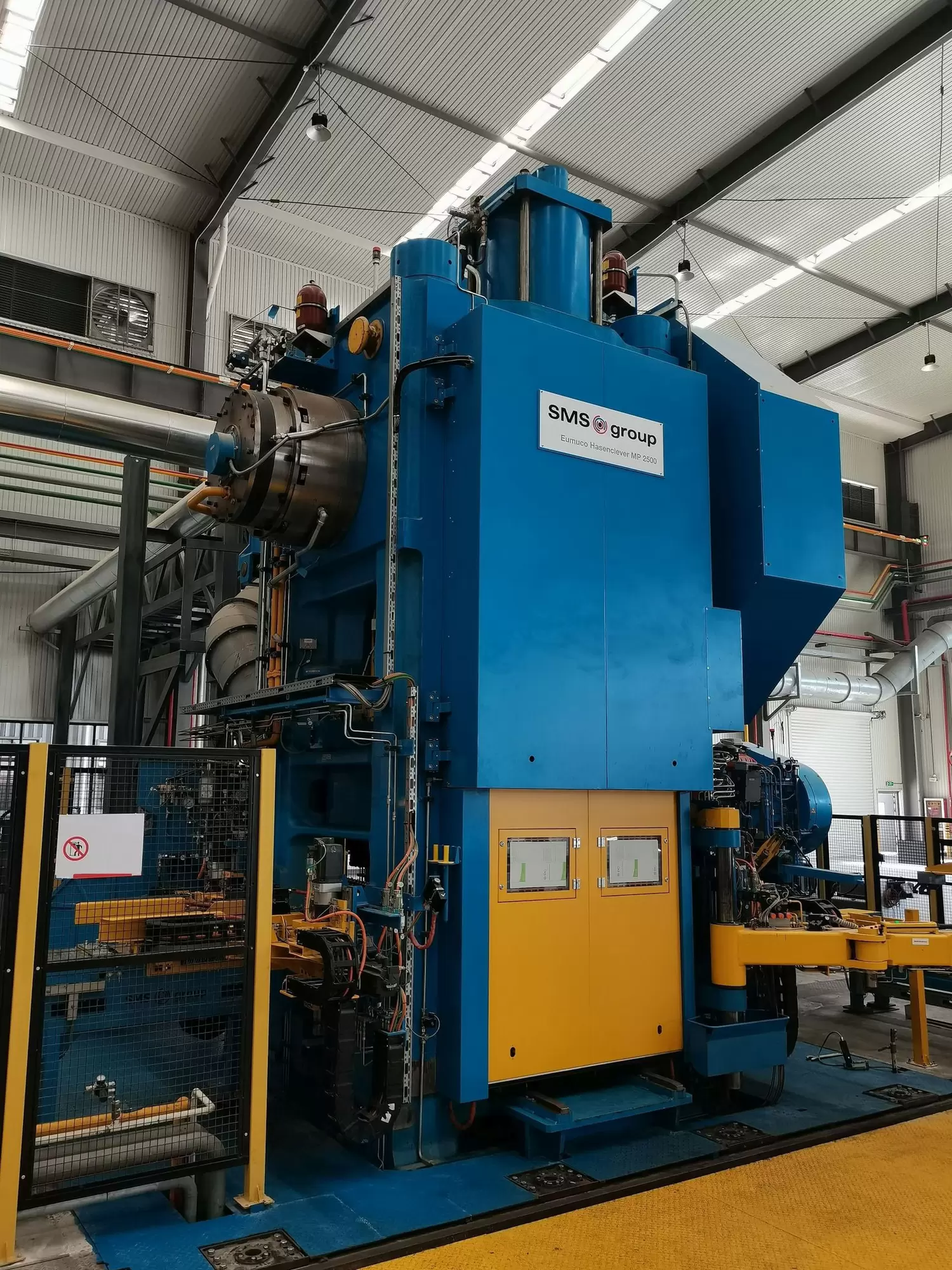
3D-printed spray heads: lighter, faster, more effective
This is not the case with our new 3D-printed spray head: it is almost maintenance-free and has far fewer parts. The 3D-printed spray head can withstand pressures of up to 10 bar. Thanks to the larger clearance, the aerosol can be precisely adjusted and positioned when setting the spray mist. Owing to the high pressure and optimized spray nozzle geometry, a larger quantity of spray fluid can also be applied if necessary. The streamlined channels prevent a build-up of deposits. The nozzle passages are thus always clear.
With the plate spraying head, the outlet funnel consists only of a chamfer inserted on the outer plates., the principle of the external-mixing air-mist nozzle is used for these spray heads, too. This guarantees that there is a uniform droplet size and that no separation can take place. Not only that, the 3D-printed version also has the advantage that the outlet form can be customized. With the plate's head, the outlet funnel consists only of a chamfer inserted on the outer plates.
The large spray heads have a circumferential channel (picture below, left). This supplies the spray head with what is known as the \"blow air\", which first removes the scale from the die when the spray heads are moved in and dries it when they are moved out. Here, too, the 3D-printed spray head stands out from the plate spraying head, which must always be surrounded by an additional blow air pipe.
A special feature of the spray heads in the Zhejiang plant is the first spraying head, which is responsible for the preliminary die. The nozzles are arranged at angles and spray diagonally upwards and downwards. The angles are chosen in such a way that the spray cones precisely wet the engraving of the preform dies. Additive manufacturing and the function-optimized construction associated with it are what make this design possible (picture below, right).
The spray heads are connected to printed polyamide blocks into which the connecting hoses of the medium supply are fitted. This saves weight, which increases the durability of the mechanical equipment in view of the high accelerations of the spray arm. The thing that all 3D spray heads from SMS have in common is their interrupted form. This means that no water puddles can gather and fall into the die during the fast return movement.