Taking a step further
Similar to the eccentric presses built by SMS group, permanently activated synchronous engines respectively torque motors are used here. A torque motor has high torques at low revolution rates allowing operation without gear unit. This is possible due to a large number of motor pole pairs ensured by high-performance permanent magnets that are installed on the rotor. Torque motors have reached industrial maturity long ago, which is proven by the fact that this type of drive has been standard in the field of machine tools for years and has been used in a wide variety of applications whether for ship engines or drives for the basic materials industry. For application in the mechanical engineering sector, SMS group has gone even further and integrated all “electrically active parts” in the mechanical structure required anyway. In doing so, a highly efficient, compact, mechatronic engine was created that reduced the footprint of the coiler to half the size needed by the conventional solution. This application provides the advantage that the existing coiler mandrel bearings can also be used as motor bearings. For that purpose, the magnet-equipped rotor is mounted directly on the coiler mandrel shaft. The motor stator, consisting of laminated core and copper winding, is installed between the existing coiler end shields.
The result is a compact and energy-efficient engine that is very easy to maintain:
- no gearwheels
- no gear unit lubrication
- no external cooling
- no mechanical brake
- significantly fewer bearings.
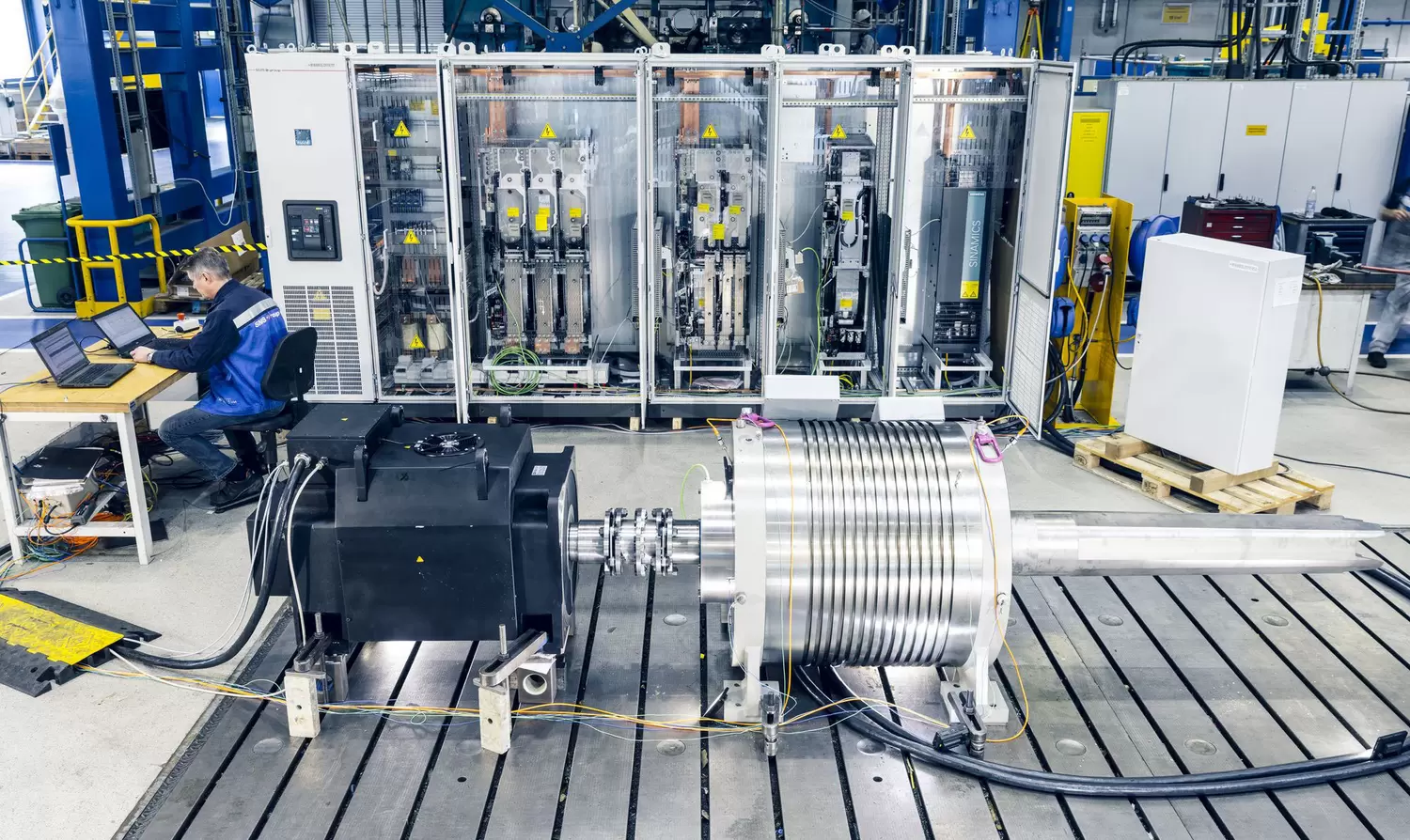
In addition to the ecological aspect, i.e. avoiding any gear oil and reducing the noise level to approx. 70 dBA (compared to more than85 dBA in the past), this drive concept comes with a particularly high effectiveness resulting from the abandonment of lossy converting stages and from saving ancillary equipment in the drive system. What’s more, the physical/electro-technical principle of a permanently excited synchronous motor makes it operate essentially more efficient than an asynchronous motor.
The innovative direct drive developed by SMS group allows the machine to achieve a total efficiency of 98 percent. In the design phase already, attention was paid to easy coiler maintenance and convenient repair incase of defects. Maintenance was reduced to lubricating two roller bearings. Another advantage showed during the tests: The control behavior of the direct drive was much better than that of an asynchronous motor drive version. So, the new solution has become path-breaking for further applications and offers the customers of SMS group numerous benefits in terms of little maintenance effort, of energy efficiency and environment protection of their plants
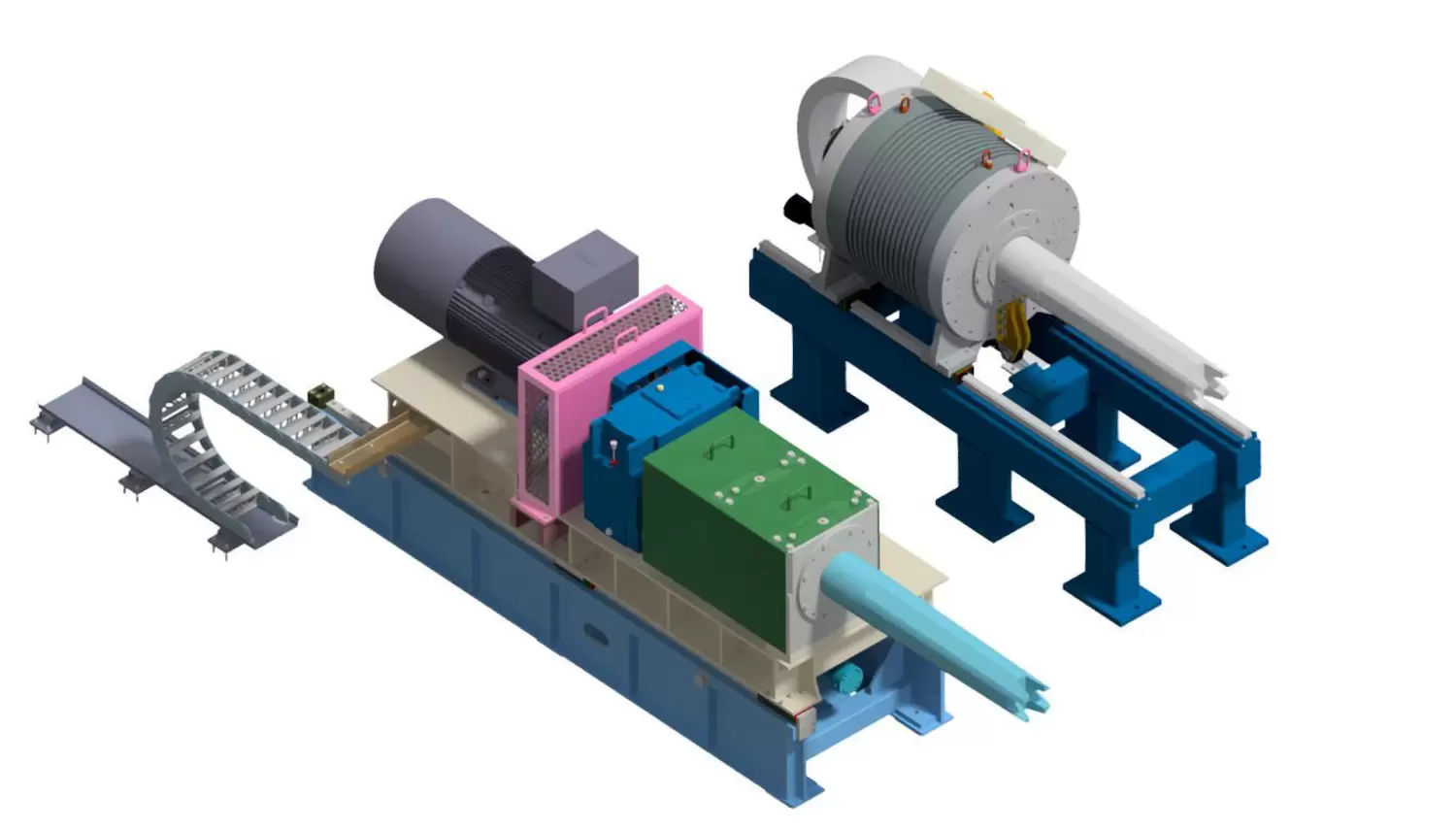