To achieve this, the intermediate and finishing stand group has been equipped and rebuilt with four new hydraulically adjusted stands and associated automation and control system. In addition to that, the profile measuring device PROGAUGE has been integrated and new roll changing units were installed.
The semi-continuous medium section mill comprises furnace, high-pressure descaler and downstream breakdown mill stand. During reversing rolling, the positioning of rolled material into various roll grooves is realized by a displacement and bloom reversing device.
Laser light cut measuring
Compliance with the tolerances and the surface quality is scanned completely by means of non-contact PROGAUGE laser technology. Up to 500 scans per second are done. PROGAUGE controls the hydraulic adjustments of stands 11 and 12 in closed loops fully automatically to compensate deviations in the rolled material within fractions of a second. In addition to that, PROGAUGE provides a system for surface flaw detection called SurfTec.
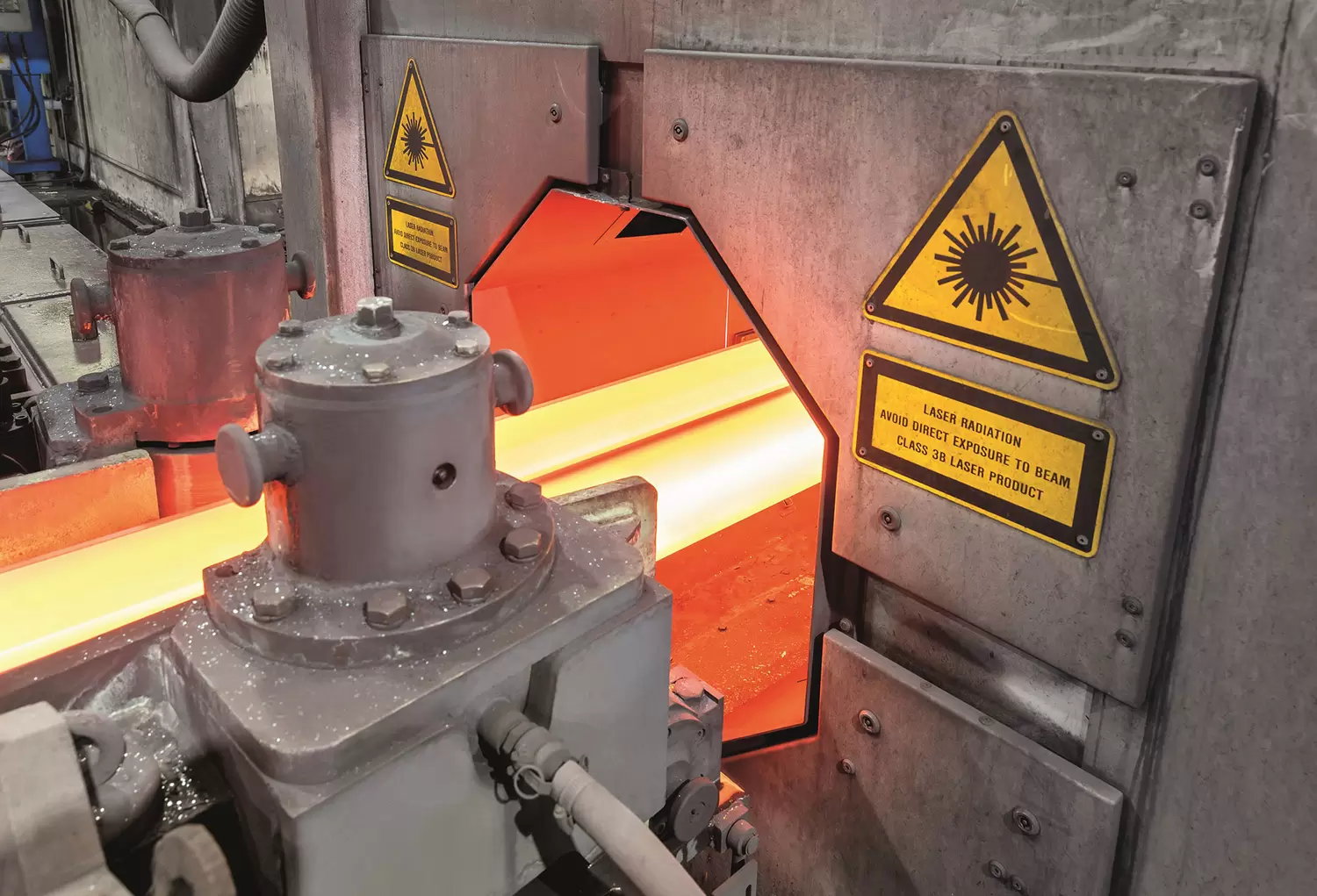