Vertical continuous and semi-continuous casters are in use worldwide to produce semi-finished products made of copper and copper alloys. Such semis are further processed into profiles in extrusion plants or into strips and foils in rolling mills. Typical fields of application are the electronics industry, seamless pipes in water lines and heat exchangers, the automotive industry and the plumbing trade.
Continuous casting plants for copper and copper alloys fulfill the following tasks: melting of the charge material followed by exact control of the temperature and the molten metal, controlled solidification inside a water-cooled mold to achieve the desired cast section and controlled withdrawal of the solidified strand. The cast strand is cut to the desired length either in the casting line or after having been removed from the line, depending on whether the caster operates continuously or semi-continuously.
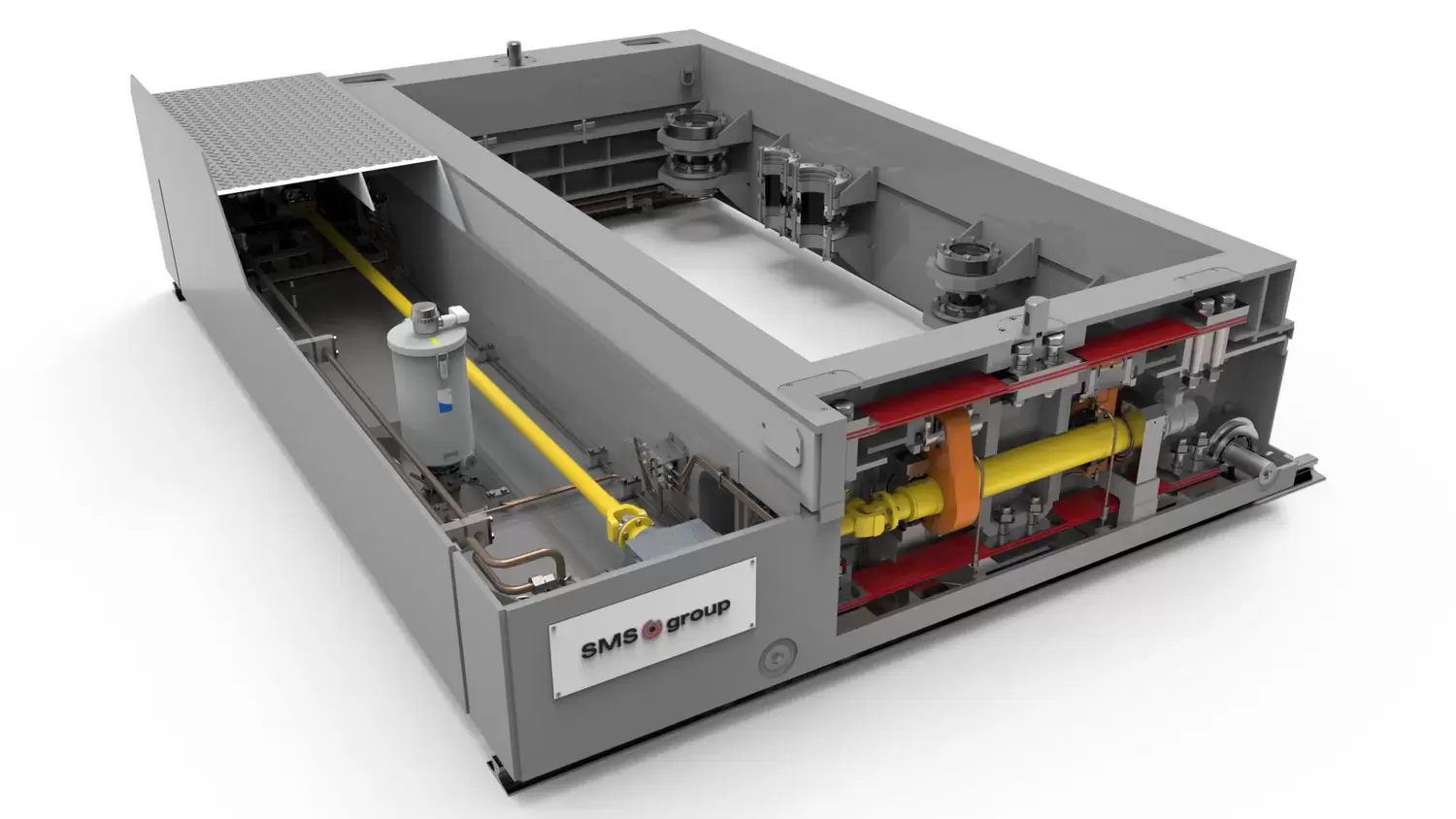
The conditions inside the mold are decisive for the quality of the cast product. The casting mold, which is open at both ends and has water-cooled side walls, and the downstream secondary cooling equipment determine the cast product’s microstructure and surface, both of which are crucial parameters for the quality of downstream processing steps.
The molten metal starts to solidify at the sidewalls of the mold. This initial solidified shell is very thin and sensitive and extremely susceptible to external effects. At this stage, care has to be taken to avoid any sticking to the mold walls in order to prevent the shell from breaking. In support of this, the mold oscillates up and down. Thus the casting result depends a lot on how precisely the mold is guided up and down and on the quality of the oscillation.
Design improvements of casting machines for copper
SMS group has significantly enhanced the original design of the casting machine. Previously, the machines used to be equipped with a centrally positioned eccentric. The lifting stroke was transferred to the mold by means of a complicated lever system that actuated coupling rods. This single-eccentric design has been replaced by a four-eccentric design. The four eccentrics act more straightforwardly on the mold and trigger the movement exactly where it is needed. This makes the support of the mold table more stable and the oscillation more sinusoidal, while eliminating the negative effect the wearing mechanical lever equipment would have had on the quality of the oscillation. As this arrangement has proved highly successful during the last few decades, it has been retained in the newly developed design.
The elements on the casting machine that used to actuate the movements of the mold have been replaced by a leafspring design. The maintenance- and play-free leaf springs have been designed specifically for this application and with a view to an extraordinarily long lifetime.
The leaf springs are arranged and aligned in such a way that they can move only in a perfectly vertical direction. This makes for a much more precise guidance of the oscillating movement and significantly improves the rigidity of the casting machine. Moreover, the new design increases safety while reducing the maintenance effort to virtually zero.
The eccentric drive features the same proven drive precision and enhancements based on experience gained in recent years. The drive acts on four positions of the frame. The oscillation frequency is adjusted by changing the drive speed. Due to the counter-rotation design, transverse forces are avoided. As an option, the eccentric can also be supplied with a system that allows the stroke height to be changed when the machine is in the idle mode.
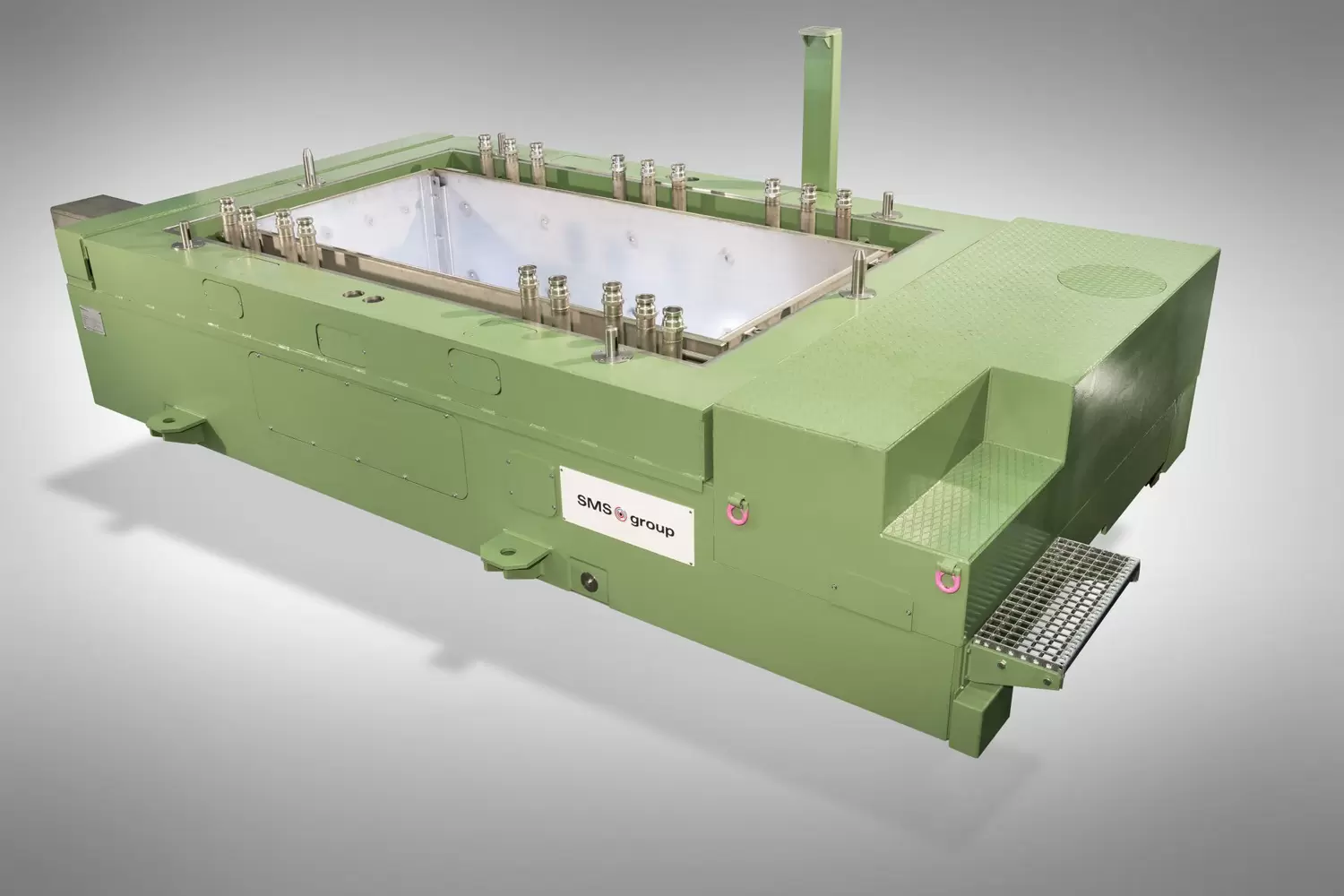
Advantages of new casting machine of leaf-spring design
- Highest-precision oscillation for top product quality
- Proven eccentric drive, available with stroke height adjustment as an option
- Maximum plant availability and improved operating reliability
- Wear-free design markedly reduces maintenance effort
- Can be installed in existing plants without major modifications
- Installation in existing plants can be accomplished during a single weekend
- Significantly reduced number of movable mechanical components
Quick-change design of the copper casting machine
The basic design of new casting machines comes with the same dimensions as the conventional one. This makes it very easy to replace conventional casting machines in existing vertical casting plants with those of the new, leaf-spring design without modifications. Even the drive mode (electric or hydraulic motor) can be retained. Thus the existing control system requires but minimal adjustments. Therefore, it is generally possible to accomplish the replacement of a casting machine during a single weekend.